Blade manufacturing technology
The manufacturing process of large directional crystallization blades for heavy-duty gas turbines includes the manufacturing of complex large-size ceramic cores and ceramic shells, parameter control during directional solidification, heat treatment and processing of blades, and preparation of long-life protective coatings. Among them, directional solidification technology is one of the key manufacturing technologies for large directional crystallization blades.
Figure 11 is a schematic diagram of the relationship between blade size and casting defects in directional solidification [11, 39]. In the directional solidification of the HRS process, as the blade size increases, the temperature gradient at the solid-liquid interface front continues to decrease. In order to maintain a stable temperature gradient at the solid-liquid interface and obtain a casting without solidification defects, the temperature of the liquid high-temperature alloy must be kept at a very high level and the solidification rate must be reduced (approximately the pulling rate of the directional solidification process). However, at 1500-1600℃, or even higher, the active liquid high-temperature alloy is in contact with the ceramic shell and core for a long time, and it is easy to react. The ceramic shell and core themselves are also prone to creep and fracture. Therefore, the process window of large directional crystallization blades is very small (the gray area in Figure 11), and it is easy to have defects such as equiaxed crystals, shrinkage cavities, and freckles. This also brings a series of problems to the shell, core, and blade post-processing [4, 11, 40].

In the 1990s, the international heavy-duty gas turbine market developed rapidly, and the demand for large directional crystallization turbine blades became more and more urgent. In order to solve the above problems faced by HRS technology in manufacturing large directional crystallization blades, Siemens, GE and Alstom all began to study the engineering application of high temperature gradient liquid metal cooling (LMC) directional solidification technology. By around 2000, Europe had completed the engineering research of LMC technology and mastered the batch production technology of large LMC blades. Since the LMC process uses low melting point alloys as cooling media, the temperature gradient of the entire directional solidification process is greatly improved, so the microstructure of the casting can be significantly refined and the pulling rate can be increased. In addition to the significant improvement of alloy structure and performance, another great advantage of LMC technology is reflected in the directional solidification manufacturing process of large blades. Since the temperature gradient of the solid-liquid interface in LMC directional solidification is always high, it is entirely possible to keep the temperature of the liquid high-temperature alloy at a low level, adopt a faster pulling rate, and avoid the problems that are easy to occur in the above HRS process in large-sized ceramic shells and cores. Reference [40] provides a relatively detailed introduction to the selection of cooling media for low-melting-point alloys in the LMC process, the optimization of LMC equipment parameters and process parameters, and the typical microstructure and mechanical properties of high-temperature alloys prepared by the LMC process.
In recent years, foreign countries have conducted further research on LMC technology in combination with numerical simulation. For example, Pollock et al. [41-43] used LMC technology to prepare the second-generation single-crystal high-temperature alloy, simulated the position of the solid-liquid interface during directional solidification, and the primary dendrite spacing of the single-crystal alloy, and studied the influence of process parameters on dendrite spacing and shrinkage cavity size and distribution. By comparing with the traditional HRS process, it is further confirmed that LMC technology can effectively refine the structure and reduce defects. Singer et al. [44-45] also found that the fatigue performance of the alloy was significantly improved because the size and volume fraction of shrinkage cavities in the alloy were significantly reduced by the LMC process.
In my country, Northwestern Polytechnical University has carried out a lot of research on alloy solidification theory by taking advantage of the high temperature gradient of LMC technology, and has conducted a relatively systematic and in-depth study on the solidification characteristics and microstructure of directional and single crystal alloys under high temperature gradient [46-50]. The Central Iron and Steel Research Institute has developed a directional crystallization gas turbine blade with a total length of about 300 mm using traditional HRS technology combined with numerical simulation [51].
The Institute of Metal Research, Chinese Academy of Sciences, began to explore the engineering application of LMC technology in 2003, and made breakthroughs in key technologies such as heat shock resistant mold shells and low-melting point metal pollution control. In 2009, it successfully developed a large-scale LMC equipment that can meet the development of 750 mm long directional crystallization blades, laying the equipment and technical foundation for the development of large directional crystallization turbine blades for heavy-duty gas turbines [52-53]. In recent years, using LMC technology, a relatively systematic work has been carried out on the directional solidification process [35, 54-55], microstructure [56], heat treatment process [57], typical properties [58-59] and casting process performance [60] of directional and single crystal alloys. Studies have shown that LMC technology can obtain significantly refined directional solidification structures, and some alloys can even be used directly in the cast state, avoiding problems such as recrystallization caused by subsequent solution heat treatment. In particular, in large directional crystallization castings that are difficult to fully achieve homogenization heat treatment, the LMC process can significantly improve the fatigue performance of the alloy [61].
The development of hot-end components for heavy-duty gas turbines started relatively late in China. In recent years, the Institute of Metal Research of the Chinese Academy of Sciences, the China Iron and Steel Research Institute, and other institutions have cooperated with relevant domestic enterprises to develop a variety of equiaxed crystal turbines and guide blades for heavy-duty gas turbines. At the same time, they have also carried out research and development work on large-scale directional crystallization turbine blades[62].
In recent years, the Institute of Metal Research has successfully developed a 430 mm long solid directional blade; based on breakthroughs in key technologies such as large-size heat shock resistant shells, complex cores, and directional solidification, it has successfully developed a 450 mm long large-scale DZ411 directional crystallization turbine blade with a complex cooling inner cavity structure using LMC technology.
Due to the slower stretching rate and lower solidification rate, the primary dendrite spacing of large directional crystallization castings manufactured by the conventional HRS process is about 350-550 μm[63-64], and defects such as freckles caused by macro segregation are prone to occur in the blades[65]. Analysis of the as-cast microstructure of large directional crystallization blades prepared by the LMC process shows that both the primary dendrite spacing (PDAS) and the secondary dendrite spacing (SDAS) increase with the increase in the distance from the cooling base. At the blade extension section and the tenon position, the PDAS is the largest, about 320 μm (Figure 12). The statistical results of the eutectic size and volume fraction at different positions of the as-cast blade are shown in Figure 13, and the casting shrinkage cavity size and volume fraction are shown in Figure 14. Since the higher temperature gradient of the LMC process reduces the segregation in directional solidification, defects such as freckles that are prone to occur in large castings are not found in all blades.
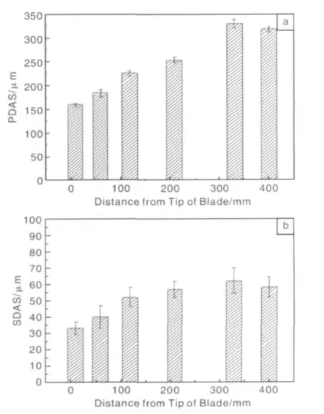
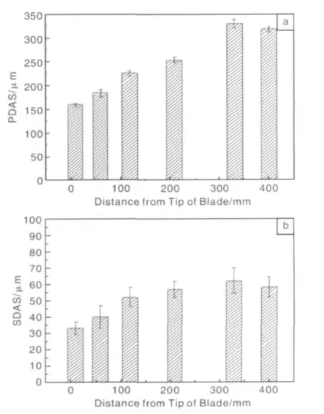
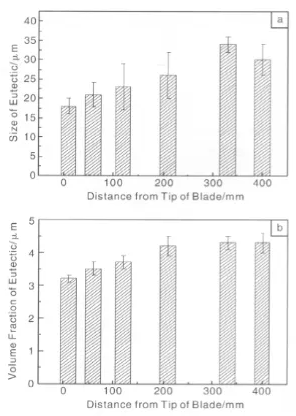
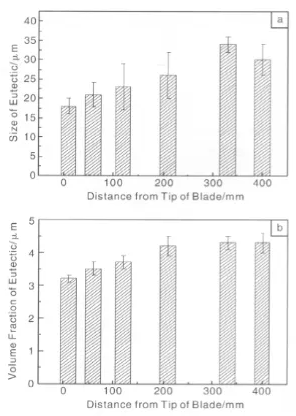
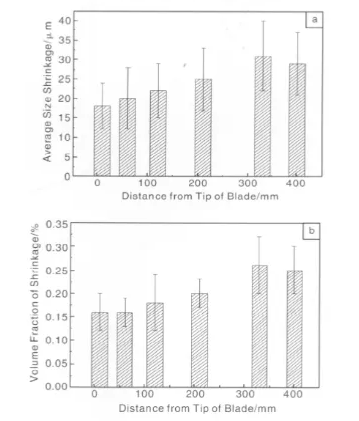
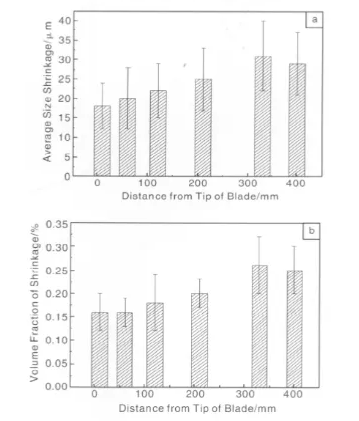
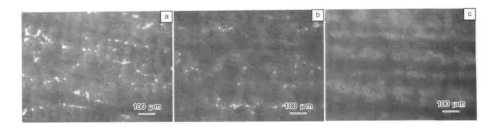
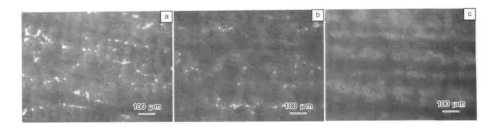
The solution treatment temperature has a great influence on the microstructure of the DZ411 alloy. Figure 15 shows the typical microstructure of the blade extension section sampled after solution treatment at different temperatures. It can be seen that with the increase of the solution temperature, the residual eutectic between the dendrites in the alloy gradually decreases. A higher solution treatment temperature can completely dissolve the eutectic between the cast dendrites and achieve full homogenization of the alloy. However, a higher solution treatment temperature may also cause defects such as recrystallization and initial melting [6]. After solution and aging heat treatment, a γ’ phase with good cubicity and a size of about 300 nm was precipitated in the matrix. In the γ matrix channel, a fine secondary γ’ phase was also precipitated (Figure 16).
Based on the above work, the Institute of Metal Research has also carried out the research and development of large single crystal blades in recent years. Combining computational simulation technology, by rationally designing the single crystal blade casting system and accurately controlling the directional solidification parameters, a large single crystal blade with a length of 300 mm was successfully prepared (Figure 17).
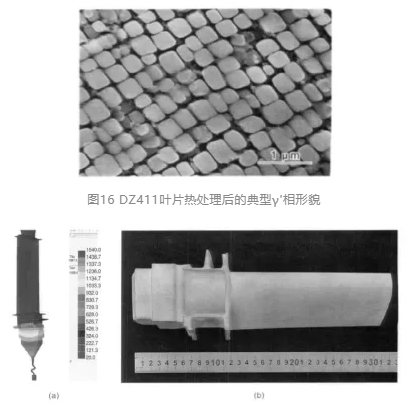
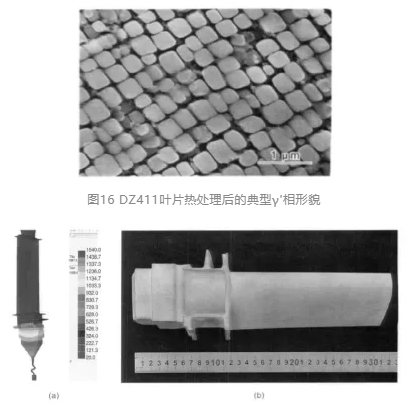