1.Precision billet technology
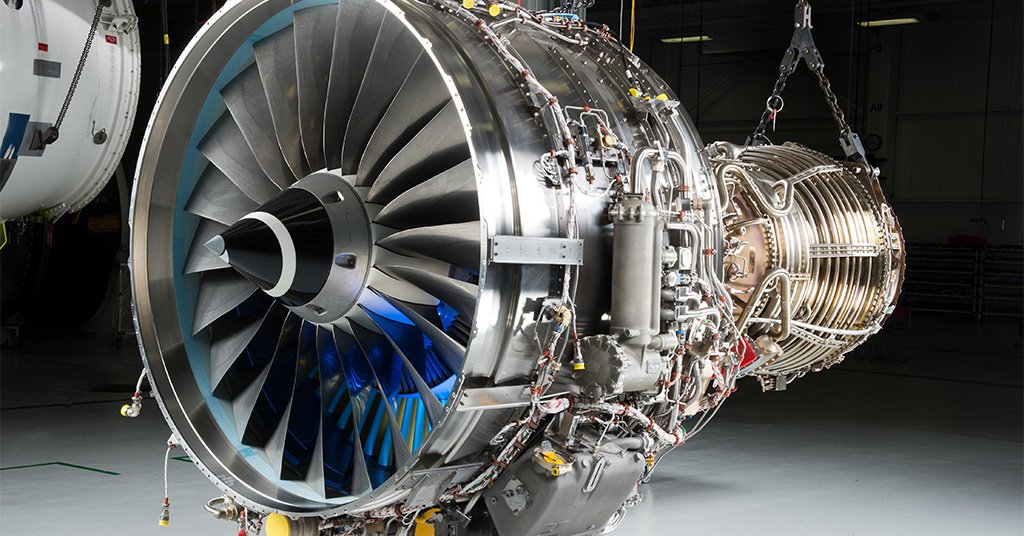
Precision billet technology includes precision forging billet, precision casting billet and 3D printing technology billet, which is a technology that provides “food” for modern aero engine manufacturing. The blank of traditional engine parts manufacturing is “black and thick”, and most of the materials in the blank are removed and consumed in subsequent processing. In the past 30 years, blade precision forging production line, isothermal forging process of blade disc parts and die forging process of box blank have been developed in the production of blade, blade disc and cartridge blanks of aero engine fan compressor. The lost wax precision casting method is used in the production of turbine blade, integral turbine disc and integral turbine guide. Integral precision casting technology in the fabrication of accessory casing and complex shell.
With the continuous development and maturity of 3D printing technology, more and more complex aeroengine structural parts with complex structure, small quantity and urgent supply in the development of aeroengines use 3D printing technology to manufacture and process blanks. Figure shows the whole blade disc blank test piece of 3D printing.
2.High efficiency and high quality welding technology
Component integration is a trend in the development of new aero engine component structure, and efficient welding technology is one of the most effective ways to realize component integration. Diffusion joint welding, linear friction welding and electron beam welding are the three key technologies for the integrated manufacturing of aeroengine components.
Diffusion welding is also known as SPF/DB technology, which is a combination of molding and welding technology, that is, diffusion welding in the process of superplastic molding, and superplastic molding in the diffusion welding. Wide chord hollow fan blades are manufactured using SPF/DB technology. With the development of wide chord hollow fan blade technology, the process difficulty and forming time of wide chord hollow fan blades are greatly increased, and the pass rate, mechanical properties, forming efficiency and cost of hollow fan blades are also significantly improved. And the criteria of qualified wide chord hollow fan blades are also developing.
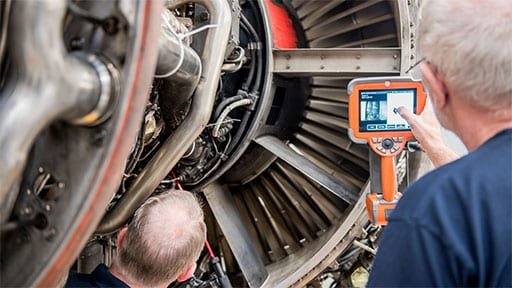
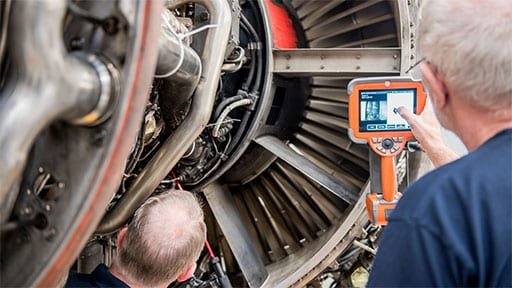
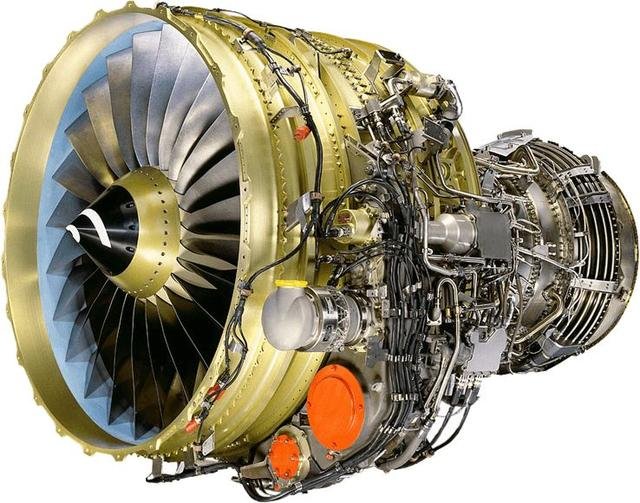
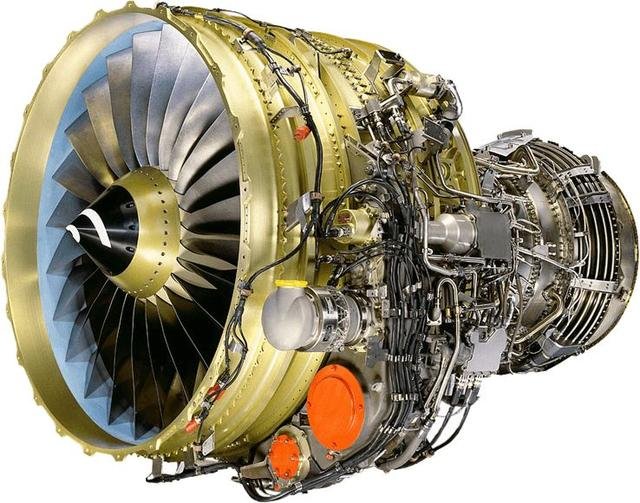
Linear friction welding is developed on the inertial friction welding technology. It uses the mutual motion between two contact workpieces to generate heat, plastic deformation occurs in the area near the contact surface, when the temperature of the friction heating area reaches a certain requirement to stop vibration and relative friction movement, and the two workpieces are solid-state connected together. The linear friction welding technique welded the hollow blade and the wheel together, which made the whole hollow blade disc of the aero engine.
Electron beam welding uses the energy of electron beam with high power density to realize welding of various material parts. The welding process is controlled by computer to ensure the controllable range of welding thickness and welding accuracy . Electron beam welding (EBEW) combines two or more stages of aero-engine monolithic disk into serial monolithic disk, which not only reduces the weight of the component instead of bolted connection, but also improves the rigidity and strength of the rotor assembly.
One Company uses electron beam welding to realize the welding of medium pressure compressor and high pressure compressor rotor assembly; Pratt & Whitney used electron beam welding to weld the PW400 booster drum, high-pressure compressor rotor assemblies of stage 2 to 8, and rotor assemblies of stage 9 to 11, and low-pressure turbine discs of stage 2 and stage 4 with the labyrinth ring. In China, in the manufacture of advanced aero engine, electron beam welding has been used to realize the welding of 5~7 grade superalloy blade disc assembly of high pressure compressor.
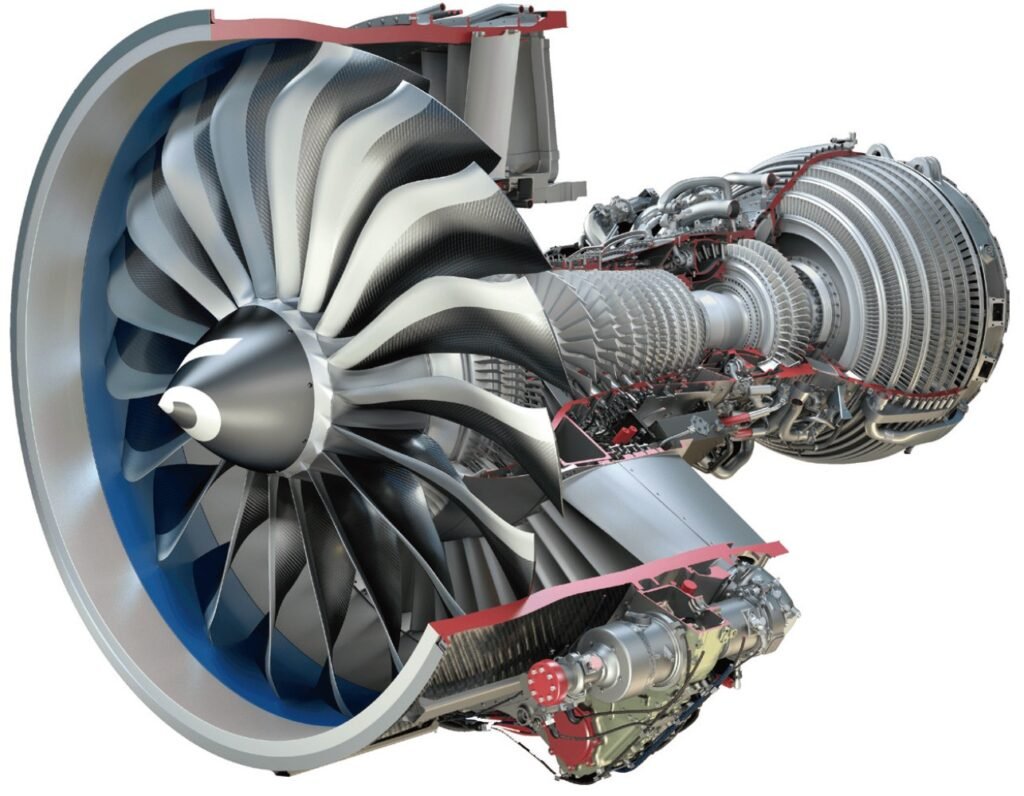
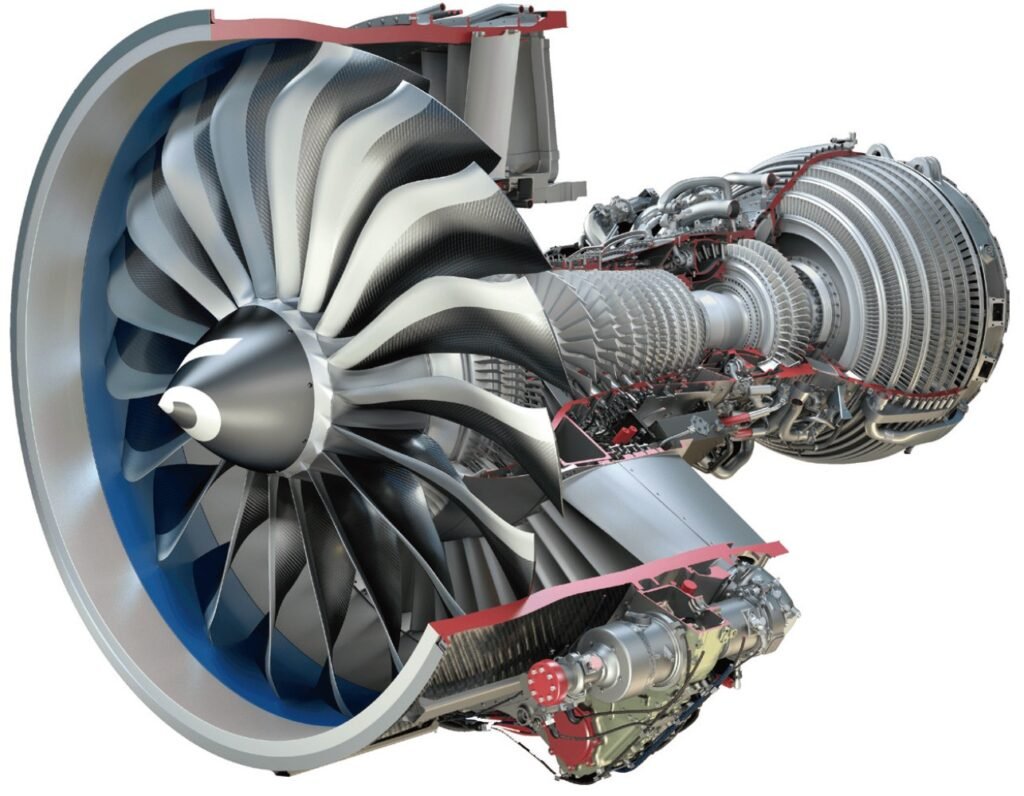
3.Tool, machine tool, component integration technology
Almost all the parts on the aeroengine need to be machined, and machining cannot be done without tools and machine tools. Modern aero-engine manufacturing technology has made the tool technology and machine tool functions develop rapidly. In recent years, in order to realize the efficient and low-cost manufacturing of aero engine parts, the research on manufacturing technology of workpiece, tool and machine tool as a whole system from the perspective of kinematics, vibration and mechanics has been carried out at home and abroad, that is, the integrated manufacturing technology of tool – machine tool – component has made great progress.
As the most direct and most important tool for cutting, the tool plays a vital role in cutting machining materials such as titanium alloy, superalloy and stainless steel for aircraft engines. However, the traditional tools can no longer meet the requirements of modern aero-engine efficient processing, and the tools are developing and improving in the direction of “high precision, high efficiency, high reliability and specialization”. At the same time, special tools for composite material processing and intelligent tools equipped with tool life prediction have also begun to be applied.
CNC machine tool development originated from solving the processing problem of aviation parts, and almost all parts of aviation engines are manufactured by CNC machine tools. High precision, high speed, compound, intelligent and environmental protection are the inevitable direction of the future development of machine tools.
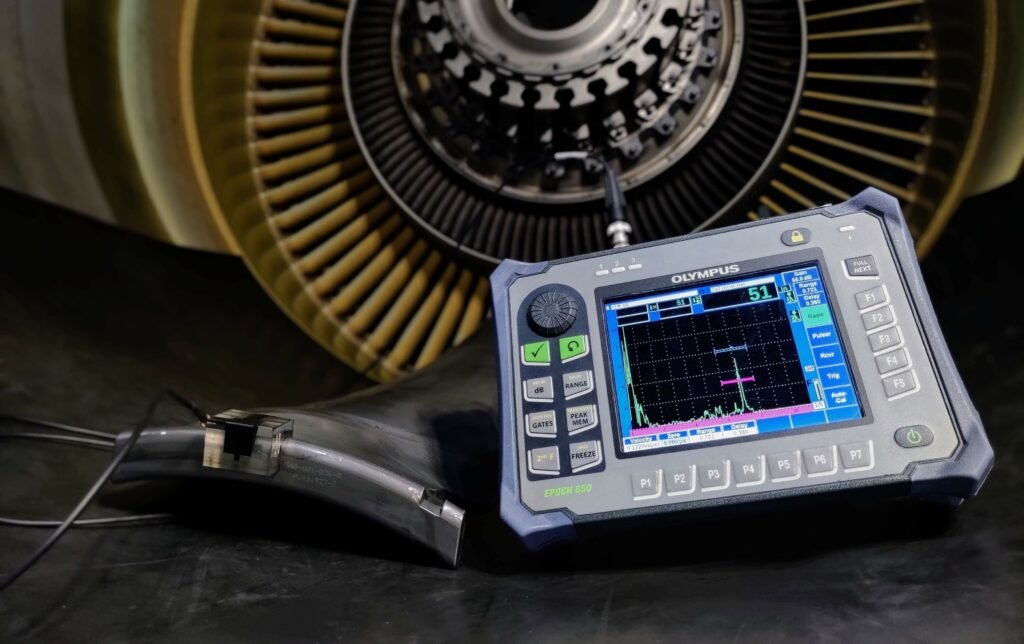
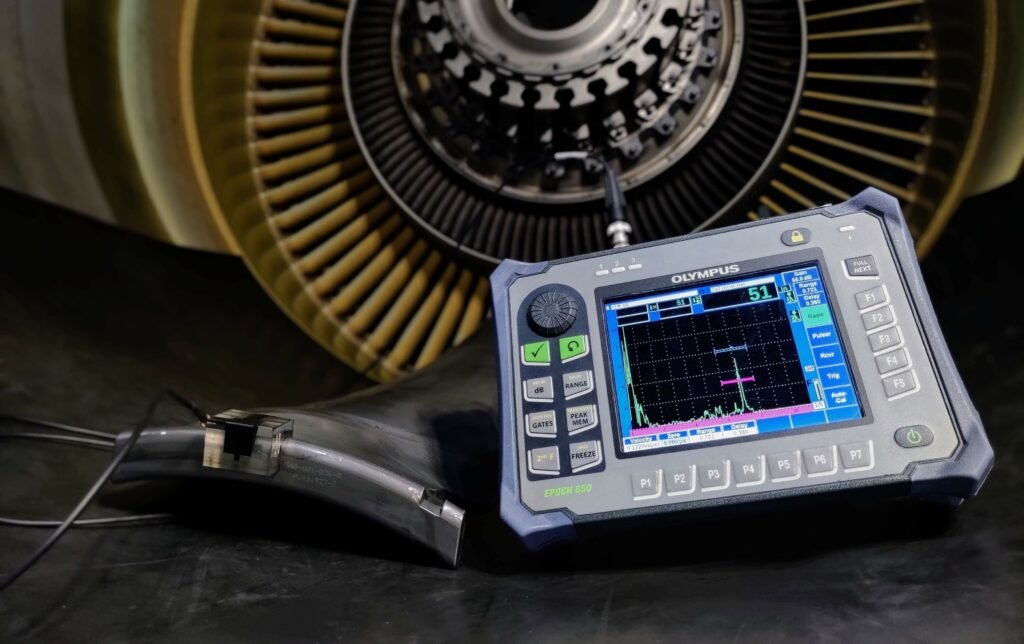
4.Development and application of basic database
Simulation technology is widely used in foreign aero engine design, testing and manufacturing to simulate the characteristics of related parts, components or engine complete machine, to simulate the deformation of forgings, solidification of castings, connection of welding parts, cutting process of materials in parts processing, etc. In order to develop high-performance aero engines, engine research institutes and colleges and universities have introduced a large number of simulation software from abroad, but the matching process database is not sold in China, and the individual database is sold but the price is very high, and some prices exceed the price of simulation software several times.
China’s engine design and manufacturing basically rely on experience. Due to the shortage of engine manufacturing personnel, the performance of the aircraft engine developed could not be compared with that of the United States and Britain, and the price of manufacturing remained high. Therefore, the development of aero engine manufacturing is closely related to the common and special materials cutting, welding, casting, forging process database, especially in the cutting process, to promote the combination of tool manufacturing technology research and material cutting technology research, general tool development and special tool development and other basic manufacturing technology research is imperative.
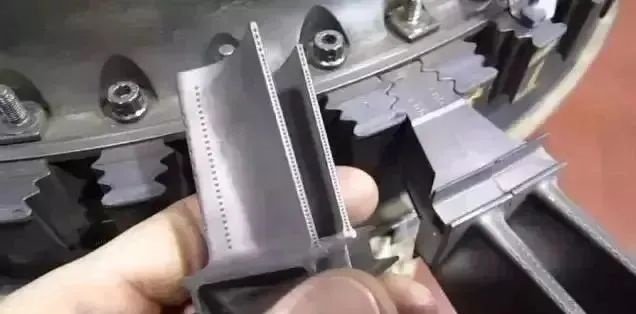
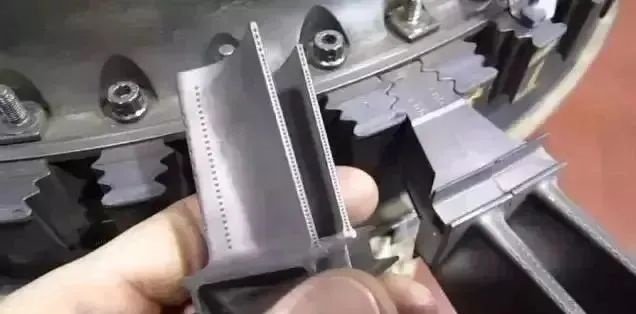
5.Engineering application technology of navigation mark, national mark and national military mark
In recent years, in cooperation with the development of new aircraft, although the majority of aviation manufacturing experts, material experts have developed and developed a large number of aviation beacons, national standards, and national military standards, which have made important contributions to the development of new aero engines, but due to the limitations of the conditions at that time, the relevant standards are not coordinated enough, and some problems have been found in engineering applications. For example, the same grade material (imitation material) according to the current standard forging parts of the blank processing deformation, low manufacturing efficiency, and according to the American standard forging parts of the blank in the subsequent processing almost no processing deformation problems; The hardness index range of some stainless steel heat treatment is very wide and even exceeds the upper limit of mechanical cutting. And these are not isolated phenomena. Therefore, it is necessary to carry out standard engineering research closely related to aero engine manufacturing as soon as possible.
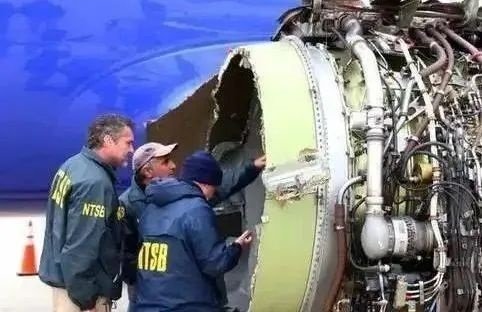
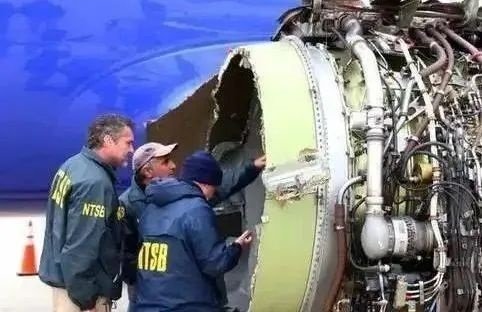
6. Processing waste recovery and reuse technology
High strength and high temperature resistant materials are required for high-performance aero engines. Ultra-heat resistant alloys based on nickel and cobalt are used in a large number of compressor and turbine components near the combustion chamber, while titanium alloy and superalloy materials are used in a large number of fan and compressor blades, casing and discs. These materials are precious metals, on the one hand, the value of these metals themselves is very expensive; On the other hand, national reserves and mineral deposits are limited. With the passing of time, the sharp contradiction between the demand and stock of titanium alloy and super heat-resistant alloy in the manufacture of aircraft engines will become more and more prominent.
In the process of engine parts manufacturing, the pouring gate of the casting, the “fat head and big ears” of the forging blank, the blade disc and the overall component processing remove almost 60% to 90% of the chips, etc., and the recovery rate is very low, and the reuse rate is even lower, resulting in extremely serious waste. The recycling and reuse of process removals is carried out at the national level in foreign countries, while most of these removals in China are sent to waste recycling stations. According to statistics and analysis, 50% of the cost of aircraft engine parts comes from the material itself. How to systematically recycle. How to remove H, O and other impurity elements in recycled materials is a difficult technical and hot issue to solve the recycling of recycled materials.
Thank you for your interest in our company! As a professional gas turbine parts manufacturing company, we will continue to be committed to technological innovation and service improvement, to provide more high-quality solutions for customers around the world.If you have any questions, suggestions or cooperation intentions, we are more than happy to help you. Please contact us in the following ways:
- WhatsAPP:+86 135 4409 5201
- E-mail:peter@turbineblade.net