1. Concept of Steam Turbine Water Hammer
Turbine water hammer, that is, the accident caused by water or cold steam (low-temperature saturated steam) entering the steam turbine, is one of the most dangerous accidents in steam turbine operation. Such accidents occur frequently at home and abroad and will cause serious consequences, so boiler and steam turbine operators are required to pay great attention to them. Once such an accident occurs, it must be handled correctly, quickly and continuously to avoid serious damage to the steam turbine equipment. First of all, the phenomena of steam turbine water hammer are:
- (1) The main reheat steam temperature drops by 50 degrees or more within 10 minutes;
- (2) The cylinder is combined at the main valve flange, the valve stem is adjusted, and white steam or water droplets are splashed at the shaft seal;
- (3) There is water hammer sound and strong vibration in the steam pipe;
- (4) The load decreases, the sound of the steam turbine becomes heavier, and the vibration of the unit increases;
- (5) The axial displacement increases, the thrust bearing temperature increases, the differential expansion decreases or negative differential expansion occurs.
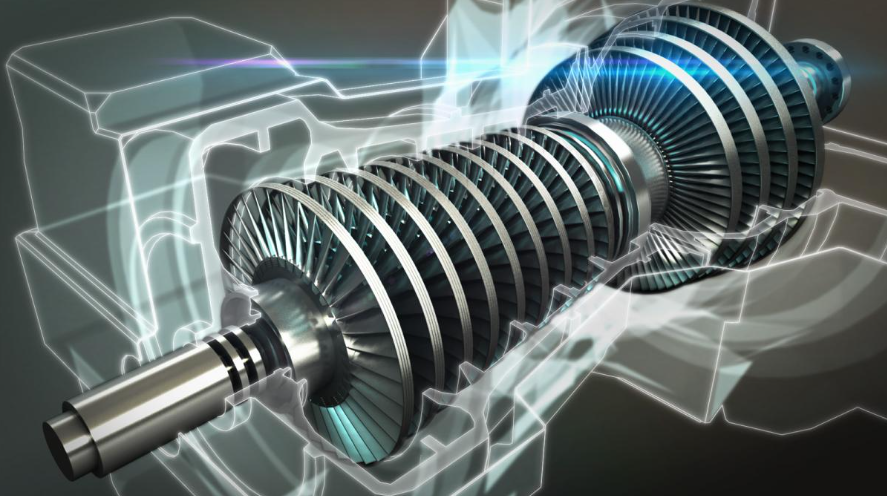
2. Hazards of water impact
(I) Collision between moving and static parts
When water or cold steam enters the turbine, the metal parts at high temperature suddenly cool down and shrink sharply, generating great thermal stress and thermal deformation, causing a sharp change in relative expansion, strong vibration of the unit, and axial and radial collision between moving and static parts. Severe radial collision may cause a large shaft bending accident.
(II) Damage and fracture of blades
When the amount of water entering the flow part of the turbine is large, the blades will be damaged and fractured, especially for longer blades.
(III) Burning of thrust bearings
The density of water or cold steam entering the turbine is much greater than that of steam, so it cannot obtain the same acceleration as steam in the nozzle, and the absolute speed when leaving the nozzle is much smaller than that of steam, making its relative speed inlet angle much larger than the relative speed inlet angle of steam, and the airflow cannot enter the moving blade channel in the correct direction, but impacts the back arc of the moving blade inlet edge. In addition to generating braking force on the moving blade, this also generates an axial force, which increases the axial thrust of the turbine. In actual operation, the axial thrust can even increase to 10 times the normal situation, causing the thrust bearing to be overloaded and burn out.
(IV) Leakage from valve or cylinder joint
If the valve and cylinder are subjected to total rapid cooling, the metal will be permanently deformed, resulting in leakage from the valve or cylinder joint surface.
(V) Cause metal cracks
When the unit is started and stopped, if water or cold steam often enters, the metal will crack under the action of frequent alternating thermal stress. For example, the rotor surface at the steam seal is affected by the steam supply system of the steam seal.
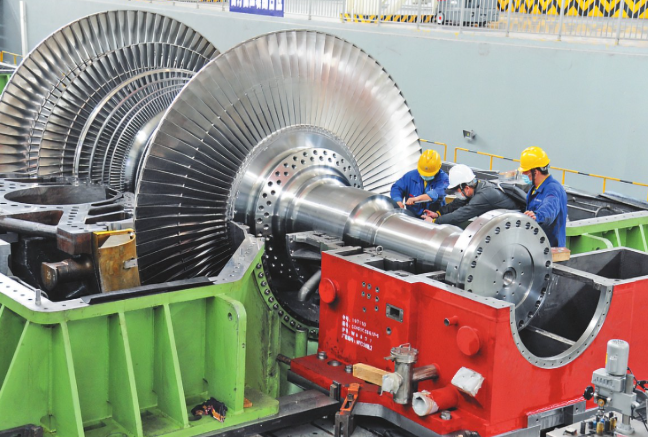
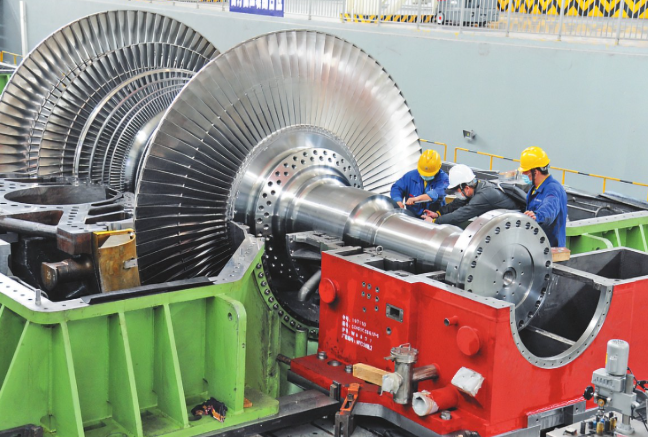
3. Causes and prevention of water hammer
There are many reasons for water hammer in steam turbines, but they can be summarized as follows:
(I) Boiler
- (1) Excessive or uneven evaporation of the boiler, improper chemical water treatment causing steam and water to boil together.
- (2) Leakage or improper adjustment of the boiler temperature and pressure reducing valve, improper air pressure adjustment
- (3) Too fast pressure increase during startup, or too fast pressure reduction and temperature reduction during parameter shutdown, causing the steam superheat to decrease or even approach or reach the saturation temperature, resulting in condensate accumulation in the pipeline.
- (4) Misoperation by the operator and the water supply automatic regulator cause the boiler to be full of water.
(II) Turbine side
During the turbine startup process, the steam-water system does not warm up the pipes for long enough, the water is not drained completely, and the operator operates improperly or negligently, causing cold water vapor to enter the turbine.
(III) Other side
- (1) When the reheat steam cold section adopts water spray cooling, due to improper operation or loose valves, the cooling water accumulates in the reheat steam cold section pipe or flows back into the high-pressure cylinder. When the unit is started, the accumulated water is brought into the turbine by steam.
- (2) The water level of the turbine reheat system heater is high and the protection device fails, causing water to return to the turbine through the steam extraction pipe, causing water hammer.
- (3) The deaerator is flooded with water, causing water to enter the shaft seal system through the deaerator steam balance pipe.
- (4) During startup, the shaft seal pipe is not fully ventilated and drained, which may also bring accumulated water into the shaft seal; when shutting down, the standby shaft seal steam source is switched, and the shaft seal steam supply carries water due to improper handling.
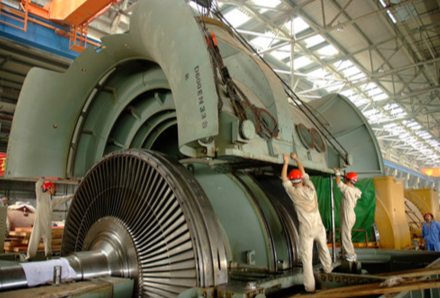
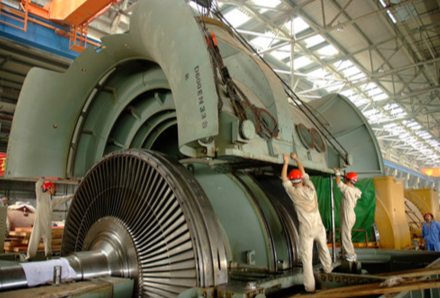
Contact us
Thank you for your interest in our company! As a professional gas turbine parts manufacturing company, we will continue to be committed to technological innovation and service improvement, to provide more high-quality solutions for customers around the world.If you have any questions, suggestions or cooperation intentions, we are more than happy to help you. Please contact us in the following ways:
WhatsAPP:+86 135 4409 5201
E-mail:peter@turbineblade.net