If the aviation engine and ground gas turbine are the “crown jewels” of modern industry, then turbine blades are the “jewels in the crown”. Turbine engines generate thrust by impacting turbine blades with high-temperature gas, driving the rotor at high speed. Among them, the ability of turbine blades to withstand high temperatures has a very large impact on the performance of the entire engine, because the higher the temperature that turbine blades can withstand, the greater the energy that can be obtained from doing work. Research shows that if the temperature at the front end of the turbine is raised by 100℃, the engine’s thrust can be increased by 10%.
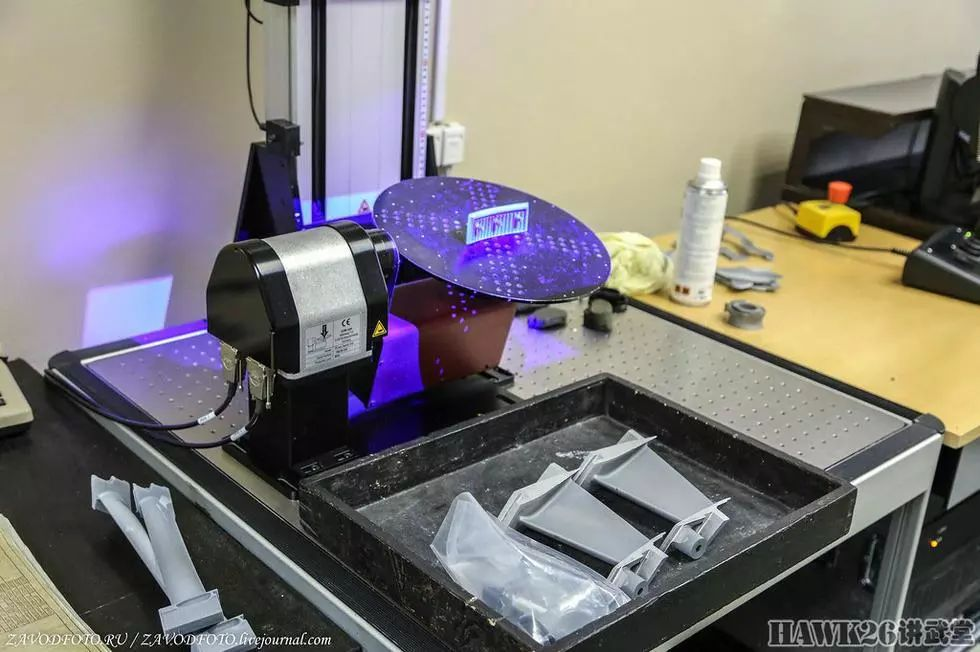
So, how can the turbine blade’s resistance to high temperatures be improved? There are mainly two approaches: improving the material’s heat resistance and the cooling technology of the blade. Therefore, one of the research directions is the development of single-crystal high-temperature alloys, as single crystals have no grain boundaries and can significantly improve the metal’s resistance to high temperatures. Consequently, the corresponding single-crystal casting technology has become a key factor in the production of turbine blades. The other is the hollowing technology for turbine blades.
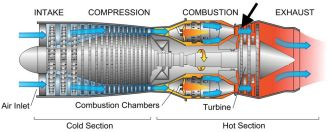
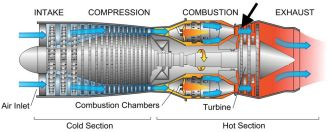
The use of hollow turbine blades in engines not only achieves lightweighting, but more importantly, provides internal cooling channels to prevent blade overheating. In the casting process of hollow blades, it is necessary to place the ceramic core at the center of the mold to achieve the formation of the cooling channel inside the blade. However, there are extremely high temperatures and large thermal stresses during the casting process, which pose a severe challenge to the performance of ceramic cores. Therefore, ceramic cores need to have at least the following performance aspects:
- High refractoriness, no softening or deformation occurs during pouring and casting solidification processes. The fire resistance of general civilian ceramic cores needs to reach 1400 ℃ or above; In the single crystal casting technology of turbine engine blades, it is necessary to withstand a high temperature of 1600 ℃, and the insulation time is generally more than 30 minutes.
- Low thermal expansion rate and stable size. The accuracy of the core directly affects the accuracy of the casting, and ceramic cores are expected to have minimal and almost no deformation at high temperatures. In addition, due to the brittleness of ceramics themselves, thermal deformation can easily cause cracking of the core, usually with a thermal expansion coefficient of less than 4 × 10-6/K
- Good chemical stability. At high temperatures, the core material cannot react with the casting material or oxygen.
- Sufficient strength. Uneven temperature during casting can generate thermal stress, and uneven thermal deformation can cause additional stress, etc. These are all factors that need to be considered.
- Easy to remove. After the casting is completed, the ceramic core needs to be easily removed, and the core must have a suitable porosity (20%~40%).
Hollow turbine blades and their single crystal casting technology have always been regarded as confidential by various countries, and domestic research has been ongoing in the face of foreign technological blockades. In 2013, AVIC initiated the research on this engine as a joint technical breakthrough project between turbine blade factories, and carried out research work including ceramic core technology, corundum shell technology, single crystal selection and directional solidification technology, and ceramic core positioning technology. They have accumulated a large amount of data and experience in ceramic material manufacturing and formulation, crystal pulling speed, process route adjustment, and many other aspects, making the casting technology of hollow single crystal blades increasingly perfect. At present, the single crystal hollow blades independently developed and produced by AVIC have a domestic price of about 100000 yuan/piece, which can significantly reduce the cost of using gas turbines in power plants, passenger planes, special ships, etc. compared to the imported unit price of 1.12 million yuan from abroad.
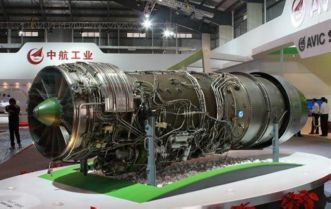
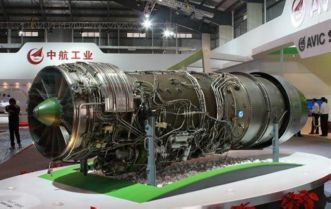
In addition to the casting technology of single crystal turbine hollow blades in the military field, advanced ceramic cores were also used in the CJ-1000A engine of China’s first civil aircraft C919. Morgan Advanced Materials provides technical support for the research and development of ceramic cores. It is reported that Morgan has partnered with AVIC Commercial Aircraft Engine Co., Ltd. to achieve precise dimensional control of internal cooling channels during casting. The ceramic core is made of alumina based ceramic material, which can withstand the high temperature during the casting process and ensure the dimensional accuracy and smoothness of the hollow blades. In addition, this ceramic core also has the characteristic of easy removal. Once the casting is completed, the ceramic core will be filtered out, making the blades hollow.
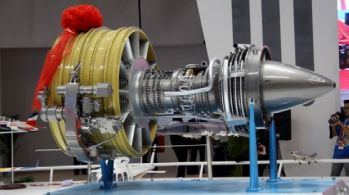
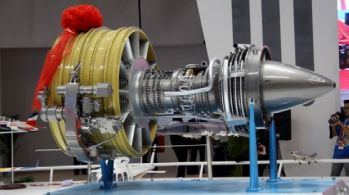
In fact, Morgan has been continuously working on casting ceramic refractory materials. In 2017, two advanced ceramic materials, P-57 and P-59, were released, both of which are silicon-based ceramic materials composed of 97% silicon dioxide and 3% zirconium, as well as trace amounts of iron, bismuth, lead, silver, antimony, tin, and zinc. These two ceramic materials can be used to make ceramic cores with a minimum contour thickness of only 0.30mm (0.01 inch), which still have sufficient stability and rigidity at high temperatures. Among them, P-57 can be used for forming thin cross-sectional parts, which can obtain exceptionally fine cross-sections and is suitable for casting aircraft wings; The P-59 is suitable for the application of extremely precise castings, and the surface of the castings will be exceptionally smooth, making it suitable for precision casting of turbine blades. In addition, both materials are easy to remove after casting and can be directly chemically dissolved.
Overall, China places great emphasis on the manufacturing technology of single crystal turbine blades, and the accompanying ceramic cores have a significant impact on the performance of the final castings. At present, the materials for ceramic cores are still mainly aluminum oxide and silicon oxide ceramics. However, as the demand for castings continues to change, for example, silicon-based ceramic cores cannot be used in the casting of stainless steel parts (due to the high-temperature activity of silicon oxide), resulting in the emergence of magnesium oxide ceramic cores; The hot pressing casting of titanium alloys requires higher requirements for the fire resistance and thermal shock resistance of the core, hence the emergence of zirconia based ceramic cores. For many years, research on ceramic cores in developed countries has been kept highly confidential and not made public. In order to avoid being controlled by others, research on materials and preparation techniques for ceramic cores still has a long way to go.