Turbine blades are extremely critical and important components in gas turbine units, which work in high temperature, high pressure and high load environment. The deterioration or failure of blade performance will have a significant impact on the integrity and reliability of gas turbine units . The main causes of turbine blade failure are thermal engine fatigue, corrosion fatigue, high cycle fatigue, creep fatigue, overtemperature, or the combination of the above failure modes. At the same time, due to the differences in working temperature, speed, working mode, total service time and manufacturing process, the deterioration or failure degree of different blades is very different.
At present, a variety of advanced techniques have been used to study the causes of turbine blade failure: the EDM direct reading spectrum can be used to measure the chemical composition of the blade; X-ray diffraction technique helps to determine the metallurgy of blade materials; Scanning electron microscopy (SEM) can be used to study blade fracture morphology, cracks and their propagation. At the same time, a variety of numerical simulation techniques have emerged, and computational fluid dynamics has been widely used to calculate blade temperature field and aerodynamic field to judge the location of blade failure. The finite element analysis is used to calculate the stress field, deformation and elongation of the blade.
The research object of this paper is the first stage turbine blade of a gas turbine unit. The power of the unit is 30 MW, the fuel is heavy oil, the turbine inlet temperature is about 1 050 ℃, the equivalent operating hours (EOH) of the unit has exceeded 5 000 hours, and the operation mode is once every 3 days. During an overhaul inspection, it was found that the coating peeling phenomenon appeared on the surface of the first-stage turbine rotor blade when the service time was far below the allowable service life. In order to avoid similar situations in the future, this paper uses a variety of technical means to conduct physical and chemical analysis of the failed blade, and adopts numerical simulation method to reproduce the temperature field and stress field of the blade during operation, so as to analyze the cause of the failure of the blade.
1. Test analysis
The first-stage rotor blade of the turbine is cast equiaxed crystal, made of IN738 alloy. The outer surface of the blade is coated with thermal barrier coating (TBC), and the inner blade has a complex cooling structure. In this paper, two turbine blades with peeling coating were selected for physical and chemical inspection, chemical composition analysis and microstructure analysis.
1.1 Appearance Check
First use acetone to clean the oil, and then use alcohol to clean. At the same time, in order to carry out more detailed appearance inspection, the blade surface is sandblasted and cleaned, and the grit diameter is 20~ 50μm.
The inspection results of blade appearance are shown in Figure 1. As can be seen from Figure 1, most of the ceramic layer on the outer surface of the turbine blade has been peeled off, and only part of the ceramic layer remains in the pressure surface and the middle of the suction surface near the inlet side of the blade body. Most of the metal bonding layer near the inlet side of the pressure surface has also been consumed (Figure 1a). At the same time, the surface of the blade is obviously discolored, which may be related to the sediment and corrosion products left by the unit during operation. Multiple cracks exist at the pressure surface of the blade surface and the transition R of the trailing edge (FIG. 1b)).
1.2 Chemical composition analysis
Grind to a depth of 4 mm on the surface of the blade, and measure the chemical composition of the blade material with an electric spark direct reading spectrometer. The alloy composition is shown in Table 1. The results showed that the leaf material was consistent with IN738.

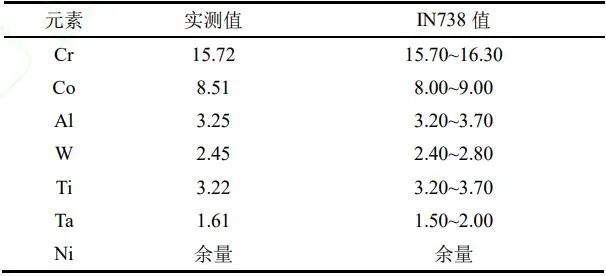
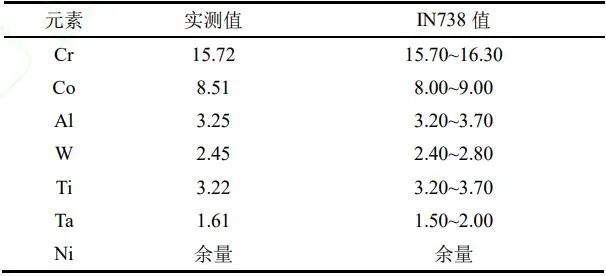
Tab.1 Alloy composition of the blade material
The samples were taken from 4 areas on the blade surface, and the energy spectrum probe of Quanta FEG-450 field emission scanning electron microscope (FE-SEM) was used to analyze the energy spectrum of the 4 samples. The four areas are respectively located at the transfer between the bottom of the blade suction surface and the platform, the bottom of the blade pressure surface near the trailing edge, the middle of the blade pressure surface near the leading edge, and the bottom of the blade pressure surface near the leading edge, as shown in Figure 2.
The results of energy spectrum analysis are shown in Figure 3. As can be seen from FIG. 3:1) the content of Zr in region 1 is very high, and there is a certain content of Y in region 1; 2) The content of Zr in region 2 is very high, and there is a certain amount of Mg, Al, Si, S, V, Fe; 3) The content of Zr in region 3 is very high, and there is a certain amount of Mg, Al, Si, S, V; 4) There is a certain amount of Mg, Al, Zr, S, Ti and V in region 4.
According to the chemical composition of leaf material, ceramic layer, binder layer and heavy oil, the following conclusions can be obtained: 1) there is a surface ceramic layer in region 1, 2 and 3, the main component is Zr; 2) There is a metal bonding layer in regions 2, 3 and 4, the main component of which is Al; 3) There are heavy oil combustion products in zone 2, 3 and 4, and the heavy oil contains V and S, which form compounds attached to the blade surface after combustion; 4) Mg is added to heavy oil, which is mainly used to inhibit the corrosion of V and S elements on the coating and matrix materials.
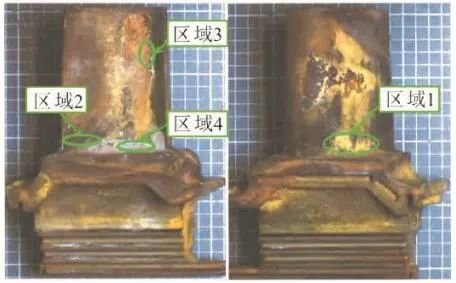
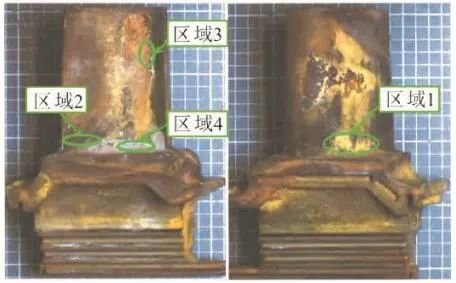
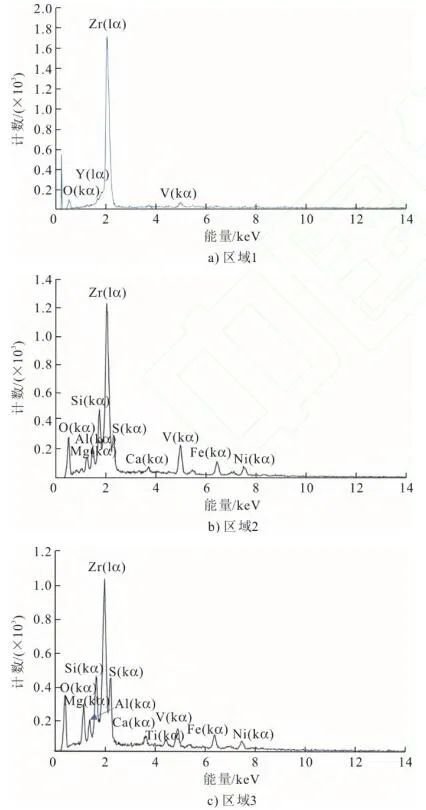
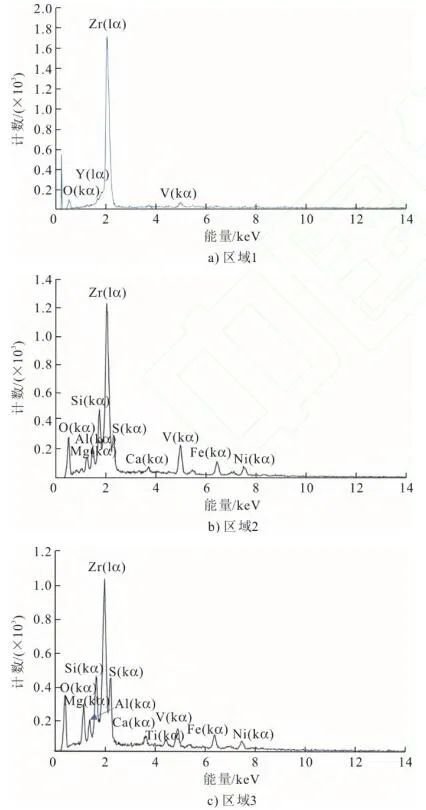
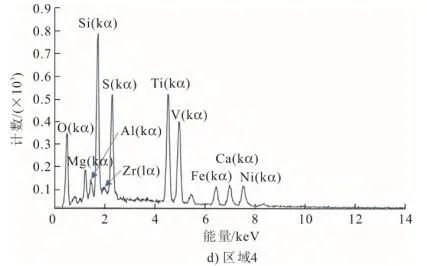
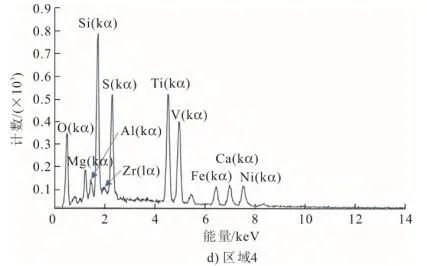
1.3 Microstructure analysis
The leading edge and trailing edge of turbine blades were sliced to prepare samples, and the microstructure of the coating on the blade surface was observed by scanning electron microscopy (SEM), as shown in Figure 4. As can be seen from Figure 4, there is no remaining ceramic layer on the blade surface, but the metal bonding layer is relatively intact. The measured thickness of the metal bonding layer is about 159.73 μm, and the thickness of the diffusion layer is about 10~15 μm, which meet the requirements of the thermal barrier coating (FIG. 4c). FIG. 4d) is A local amplification of FIG. 4c), and the results show that corrosion has occurred on the surface of the metal bonding layer (region A), which indicates that the dense oxide layer α-Al2O3 on the surface of the metal bonding layer has been lost . At the same time, due to the large loss of Al elements, the remaining β-NiAl phase in the metal bonding layer will be transformed into a γ ‘phase (Ni3Al) , which further reduces the oxidation corrosion resistance of the metal bonding layer (Figure 4d) area B).
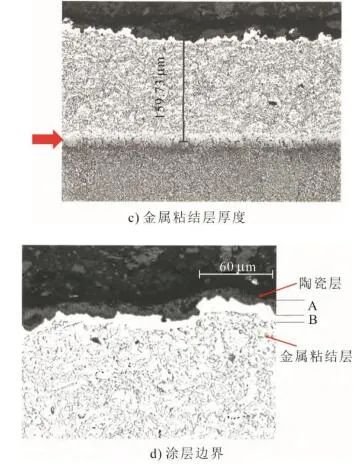
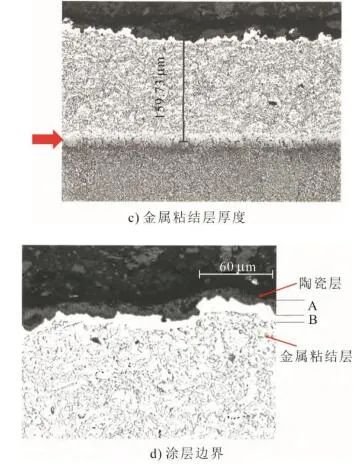
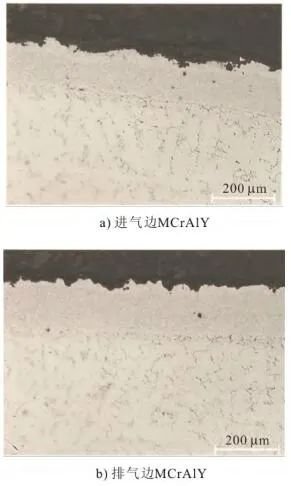
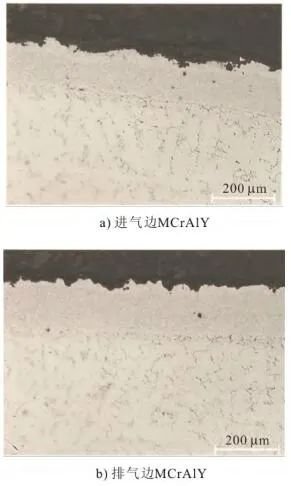
2. Temperature field analysis
2.1 Calculation of temperature field
The commercial software CFX was used to simulate the flow field outside the blade. During the calculation, a blade flow path was selected for steady state analysis, and the tip clearance was considered. The blade surface was set as an adiabatic non-slip rotating wall, the shroud surface of the gas flow path was set as a stationary wall, the radial distribution function of the absolute total pressure and absolute total temperature flow Angle at the gas inlet and the radial distribution function of the static pressure at the gas outlet were given. When CFX software is used, shear stress transfer (SST) two-equation turbulence model is selected, turbulence transition simulation is checked, and the influence of viscous work term on flow field is considered. The high precision solution method is selected to simulate the convection term and boundary layer turbulence.
After the flow field calculation results are obtained, the heat transfer coefficient of the outer surface of the blade can be analyzed and extracted. The heat transfer coefficient of the outer surface of the blade can be obtained by referring to the classical layer and turbulent flow and heat transfer theory of the plate outflow boundary. The change of the outer heat transfer coefficient of the blade profile in the middle section with the absolute arc length is shown in Figure 6. In this paper, the external heat transfer coefficients of the four sections of the blade, namely 10%, 50%, 75% and 95% sections, are calculated.
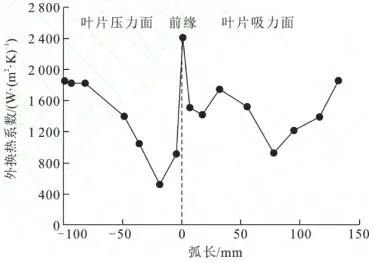
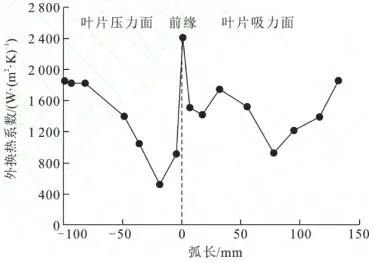
The mesh division of the blade was carried out, and the fine features of the cooling structure inside the blade were encrypted. The minimum local mesh size was 0.02 mm. Finally, the total number of meshes generated was 14 million and the number of nodes was 2.8 million. The heat transfer coefficient of the cooling channel inside the blade is calculated by using the relevant formula and referring to the relevant literature.
2.2 Analysis of Results
Load the obtained heat transfer coefficient of the inner and outer surfaces of the blade to the corresponding surface, and use CFX to solve the thermal conductivity problem of the blade, the three-dimensional temperature field of the blade can be obtained, as shown in Figure 7. As can be seen from FIG. 7, the temperature distribution of the pressure surface of the blade body is divided along the axial direction, and the highest temperature of the blade body is located in the leading edge (FIG. 7a) in region 1, reaching 858.4 ℃, which is caused by the strong external heat transfer coefficient. The temperature in front of the blade compressive force at 2/3 arc length is low (region 2 in FIG. 7a), because the heat transfer coefficient outside is small; After 1/3 of the pressure surface, the heat transfer coefficient of gas gradually increases towards the tail edge of the blade, while the heat transfer coefficient of the internal cold air is almost unchanged, resulting in a gradual increase in the metal temperature(Region 3 in Figure 7a).


The high heat transfer coefficient in the transition area of the suction surface of the blade body leads to a higher blade temperature (region 5 in FIG. 7b), but the temperature near the transition area of the suction surface is lower (region 8 in FIG. 7b), which is mainly related to the discrete cooling channel inside the blade being closer to the suction surface and its large flow of cold air. The lower heat transfer series downstream of the transition zone results in lower blade temperatures (Area 6 in Figure 7b). The high heat transfer coefficient, small trailing edge radius and almost no cooling at the blade trailing edge result in a higher trailing edge region temperature (area 7 in Figure 7b). The suction surface has a distinct temperature triangle (area 9 in FIG. 7b), because aerodynamic calculations and heat transfer calculations at 75% and 95% sections show that the fluid forms a strong tip leakage vortex and heat transfer there. This is consistent with the color distribution of the outer surface of the leaves.
3. Stress field analysis
3.1 Calculation of stress field
One of the blade/disk sector models was intercepted for non-linear finite element calculation. The stress distribution of blade and wheel under steady state condition is analyzed, and the finite element model is shown in Figure 8.
The blade base material is IN738 and the coating material is TBC. The adhesive layer is also a metal material with a thickness of only 0.1mm. Therefore, the adhesive layer and the substrate are combined in the calculation. Surface coating is used to simulate the ceramic layer with a thickness of 0.3mm. BKIN constitutive model was adopted for blade matrix during calculation, as shown in Table 2.
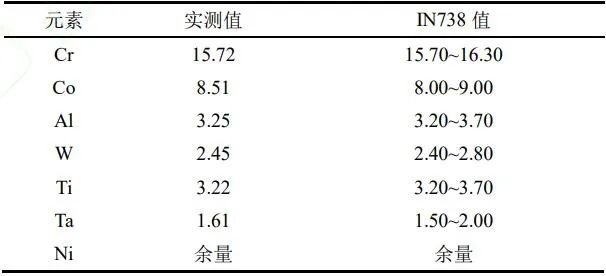
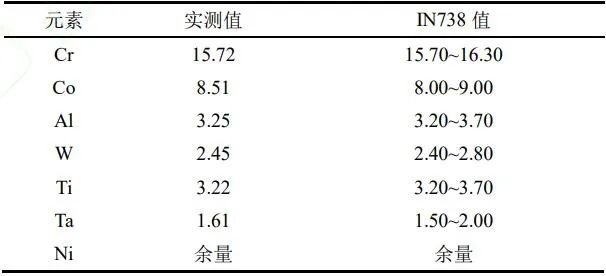
Tab.2 The In738-BKIN model
The boundary conditions are as follows: 1) blade applied temperature field; 2) The temperature field applied by the wheel; 3) Blade and wheel applied speed; 4) A contact pair is arranged between the blade root and the blade groove; 5) Apply axial and circumferential displacement constraints at the end teeth of the wheel, and apply radial displacement constraints at the disk center. The temperature and load cycles are shown in Figure 9.
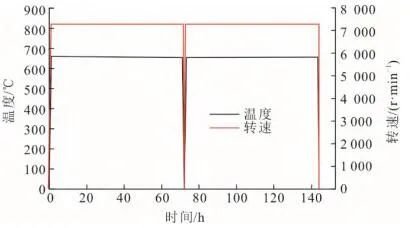
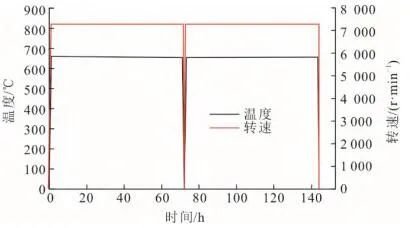
3.2 Result Analysis
The overall stress distribution of the blade matrix is shown in Figure 10. As can be seen from FIG. 10, the maximum blade stress is located at the trailing edge transition R, the stress value is 690 MPa, and the temperature is 775 ℃. The maximum stress position is consistent with the failure position of the trailing edge in FIG. 1b. At the same time, the direction of the first principal stress is radial along the blade and perpendicular to the crack cracking direction at the failure point of the blade. Due to the frequent start and stop of the unit, a large alternating stress is generated here, and cracks are caused by fatigue. The stress level in the rest area of the blade body is not high.
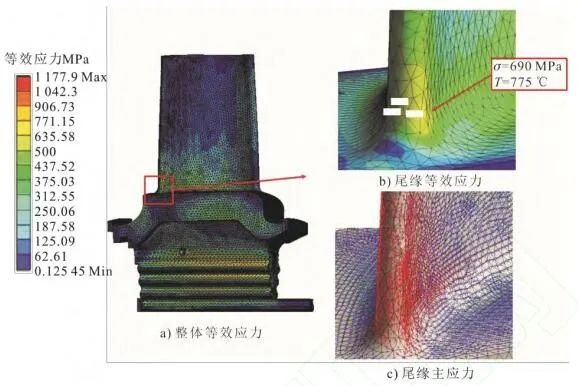
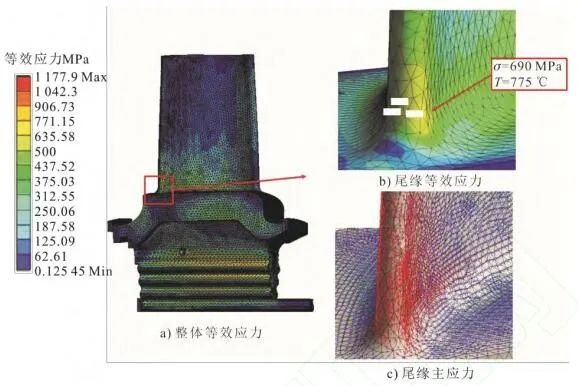
4 Failure Analysis
Based on the results of physical and chemical analysis and numerical simulation, the failure mechanism of turbine blades is analyzed, and the following conclusions are drawn.
1)The fuel of the gas turbine unit is heavy oil, which contains a large amount of S and V in its composition. When the heavy oil enters the combustion chamber, it reacts to form sulfate at high temperature. The sulfate molten at high temperature has fluidity and can pass through the voids or cracks in the ceramic insulation layer to reach the surface of the bonded substrate and react, thus causing the coating to fall off. The reaction equation is shown in equations (1) – (5). The V contained in heavy oil will react to form metal vanadate at high temperature. A large number of research results show that when it coexists with sulfate, the corrosion effect will be further enhanced, and the corrosion efficiency after mixing can be increased by more than 10 times compared to the normal state. As a result, the top coating on most blade surfaces falls off well below the allowable service life.
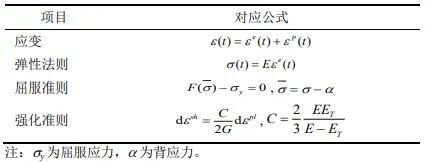
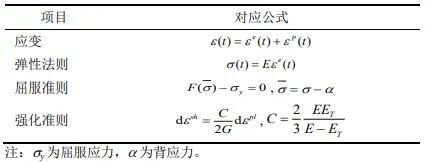
2) The calculation results of blade temperature field show that the temperature distribution of blade body is divided along the axial direction. In region 1, the external heat transfer coefficient is strong, so the blade temperature is high, which intensifies the sulfate fluidity, thus accelerating the corrosion of the ceramic layer, which causes the ceramic layer coating near the leading edge to fall seriously; In zone 2, lower metal temperature and lower gas scour rate allow the ceramic layer coating in this region to be preserved; In region 6, the suction surface of the blade body leaves the downstream of the transition zone of a certain width, the metal temperature is low, and the ceramic layer coating in this region is also retained.
3) The simulation results of blade stress field show that the maximum stress at the transfer R of blade trailing edge matrix is 690 MPa and the temperature is 775 ℃. Due to the frequent start and stop, fatigue damage occurs, which leads to fatigue crack initiation.
In this paper, physical and chemical analysis and numerical simulation are carried out to analyze the coating peeling and fatigue cracks at the trailing edge transition R of a turbine turbine moving blade, and the failure mechanism of the blade is obtained.
Thank you for your interest in our company! As a professional gas turbine parts manufacturing company, we will continue to be committed to technological innovation and service improvement, to provide more high-quality solutions for customers around the world.If you have any questions, suggestions or cooperation intentions, we are more than happy to help you. Please contact us in the following ways:
- WhatsAPP:+86 135 4409 5201
- E-mail:peter@turbineblade.net