Affected by political, military and economic factors, the development of aircraft engine technology is faster than that of gas turbines. Gas turbines and aircraft engines have a wide range of technical commonalities, and can be shared in design systems, manufacturing systems, talent systems and test systems. Therefore, based on the huge market demand and obvious application advantages of gas turbines, it has become an industry consensus to develop gas turbines based on high-performance, mature aircraft engines and advanced industrial technologies and design methods. There are two ways to transfer aircraft engine technology to gas turbines, as shown in Figure 1: one is to directly modify and derive mature aircraft engines to form aero-derivative gas turbines; the other is to transplant aircraft engine technology to heavy-duty gas turbines and research and develop a new generation of heavy-duty gas turbines.

Development History of Aero-derivative Gas Turbines
Along with the development of aviation engine technology and the application of advanced cycle technology, the technical development process of aero-derivative gas turbines has gone through the technology exploration stage, technology development stage and advanced cycle application stage, realizing the development of aero-derivative gas turbines from simple modification to high-performance core engine optimization design, from simple cycle to complex cycle application, from inheriting the mature design system and material system of aviation engines to the design of new components and the application of new materials, which has enabled the design level, performance, reliability and life of aero-derivative gas turbines to achieve considerable development.
Technology exploration stage
In 1943, the world’s first aero-derivative gas turbine was successfully developed. After that, Rolls-Royce, GE and Pratt & Whitney designed the first batch of aero-derivative gas turbines based on mature aircraft engine modifications, including industrial Avon, industrial Olympus, Spey gas turbines, LM1500 and FT4. At this stage, the technology of aero-derivative gas turbines was in the exploratory period. The structure directly inherited the core of the aircraft engine, and the output power was achieved by equipping a suitable power turbine; the overall performance of the machine was not high, and the cycle efficiency was generally less than 30%; the initial temperature before the turbine was less than 1000℃, and the pressure ratio was 4 to 10; the compressor was generally subsonic; the turbine blades used simple air cooling technology; the material used was the initial high-temperature alloy; the control system generally used a mechanical hydraulic or analog electronic adjustment system.
Technology Development Stage
With the mature application of aeroengines, high-performance, high-reliability parent machines and advanced design technologies have been provided for the rapid development of aeroderivative gas turbines. At the same time, the demand for advanced aeroderivative gas turbines by the navies of the United Kingdom, the United States and other countries has also provided a broad application stage, which has enabled aeroderivative gas turbines to develop rapidly and significantly improve their performance. A series of aeroderivative gas turbines with good performance and high reliability have been launched. . Such as LM2500 series, industrial Trent, FT4000 and MT30, etc., are widely used in ship power, power generation and other fields.
The hot end components of aero-derivative gas turbines in the technological development stage generally use super alloys and protective coatings to improve temperature resistance, and apply advanced air cooling technology and low-pollution combustion technology; the initial temperature before the turbine reaches 1400°C, the power can reach 40-50MW, the thermal efficiency of a single unit exceeds 40%, and the combined cycle efficiency can reach 60%; a digital electronic control system is used, and the control accuracy and control performance are significantly improved.
Apply advanced cycles
As the requirements for high performance of aeroderivative gas turbines, especially fuel consumption, output power and other indicators, increase, advanced cycle aeroderivative gas turbines have gained widespread engineering practice. Adding an intercooling or intercooled heat recovery cycle on the basis of the gas turbine thermal cycle can significantly improve the output power and low operating condition performance of the aeroderivative gas turbine. For example, the power level of the LMS100 intercooled gas turbine reaches 100MW and the efficiency is as high as 46%. The thermal efficiency of the WR21 inter-cooling recuperation gas turbine at low operating conditions is much higher than that of a simple cycle gas turbine. As a ship power, it greatly improves the ship’s economy and combat radius.
The output power of advanced cycle aeroderivative gas turbines using intercooling or intercooled heat recovery cycles has been greatly increased, and the thermal efficiency in all operating conditions has been improved. For example, the power level can reach 100MW, and the thermal efficiency at the design point is as high as 46%; the low operating condition performance has been significantly improved, The thermal efficiency can reach 40% under 50% load; intercooling reduces the specific power of the high-pressure compressor, and the design pressure ratio of the whole machine can reach more than 40.
Technology development model
Looking at the development history, aero-derivative gas turbines have technical development models such as pedigree development, serial development, adoption of advanced cycle technology and application of combined cycle mode.
Genealogical development
Genealogical development is the development of gas turbines of different types and power levels based on the same aircraft engine, which fully reflects the characteristics of aviation-derivative gas turbines: “one machine as the basis, meeting multiple uses, saving cycles, reducing costs, deriving multiple types, and forming a spectrum.”
Taking the CF6-80C2 aircraft engine as an example, the LM6000 gas turbine directly uses the core engine of the CF6-80C2 and maintains the maximum versatility of the low-pressure turbine; the LMS100 inherits the core engine technology of the CF6-80C2, combines the F-class heavy-duty gas turbine technology and intercooling technology, and has a power of 100MW; the MS9001G/H fully adopts the mature technology of the CF6-80C2 aircraft engine, and through the combination with the heavy-duty gas turbine technology, the temperature before the turbine is increased from 1287℃ of the F-class to 1430℃, and the power reaches 282MW. The successful development of the three types of gas turbines has enabled the aviation-based development of the CF6-80C2 aircraft engine to achieve “one machine with multiple types, developing gas turbines of different types and powers”.
Series development
The serial development is to continuously upgrade and improve, improve performance and reduce emissions on the basis of a successful gas turbine, so as to achieve the serial development of aero-derivative gas turbines, among which the LM2500 series is the most typical, as shown in Figure 2. The LM2500 gas turbine uses the core engine of the parent engine TF39/CF6-6, and changes the low-pressure turbine of the parent engine to a power turbine; the LM2500+ gas turbine adds one stage in front of the compressor of the LM2500 gas turbine, so as to improve the air mass flow and output power; the LM2500+G4 increases the gas turbine air flow rate by improving the compressor blade profile and increasing the turbine throat area on the basis of the LM2500+, so as to achieve the purpose of continuously improving the output power. With the serial development of the LM2500, the product is continuously upgraded and improved, with a power range of 20 to 35MW, and the number of equipment worldwide exceeds 1,000 units, making it the most widely used model to date.


Due to the difficulty of development and production, the serial development based on the successful gas turbine is an important technical development model for aero-derivative gas turbines, which is to continuously upgrade and improve, improve performance and reduce emissions. The serial development of aero-derivative gas turbines is similar to the pedigree development, which can not only shorten the development cycle, but also ensure better reliability and advancement, and significantly reduce the design, development, testing and manufacturing costs.
Efficiency
The goal of efficiency improvement is to continuously improve the performance of the entire machine, especially the output power of the entire machine and the thermal efficiency under all operating conditions. The main ways are as follows.
One is the application of advanced cycles. The application of advanced cycles can continuously improve the performance of aeroderivative gas turbines, such as reheat cycle, steam reinjection cycle, chemical recuperation cycle, wet air cycle, series wet air advanced turbine cycle and Kalina cycle, etc. After applying the advanced cycle, not only the performance of the aeroderivative gas turbine unit will be improved, but the power and thermal efficiency of the entire unit will also be significantly improved, and nitrogen oxide emissions will be significantly reduced.
The second is high-efficiency component design. High-efficiency component design focuses on high-efficiency compressor design and high-efficiency turbine design. High-efficiency compressor design will continue to overcome the technical difficulties of high speed and high efficiency and low speed and high surge boundary faced by compressors. As shown in Figure 3, the design of turbines will continue to develop in the direction of high efficiency, high temperature resistance and long life.
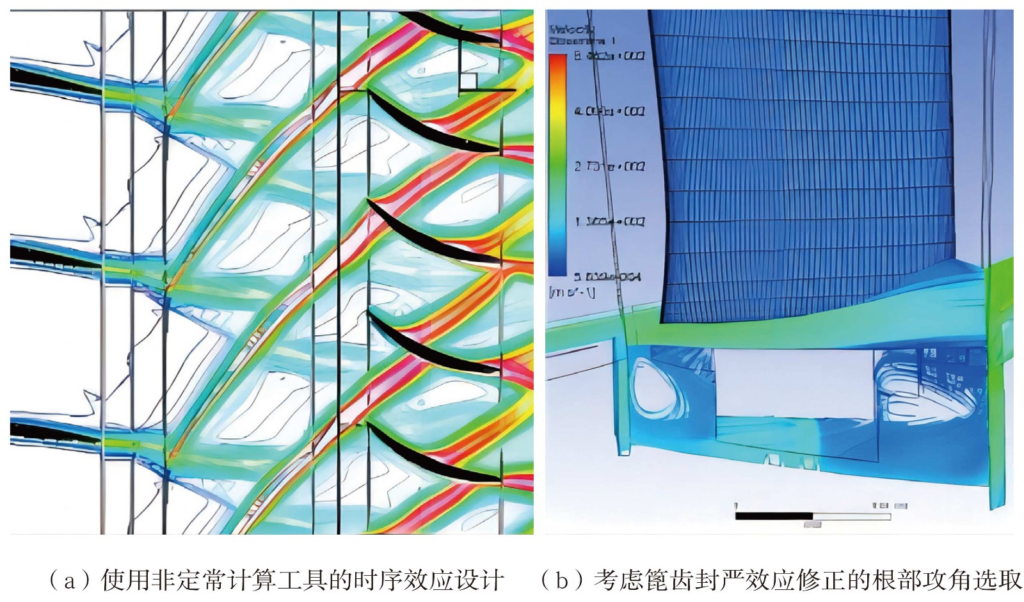
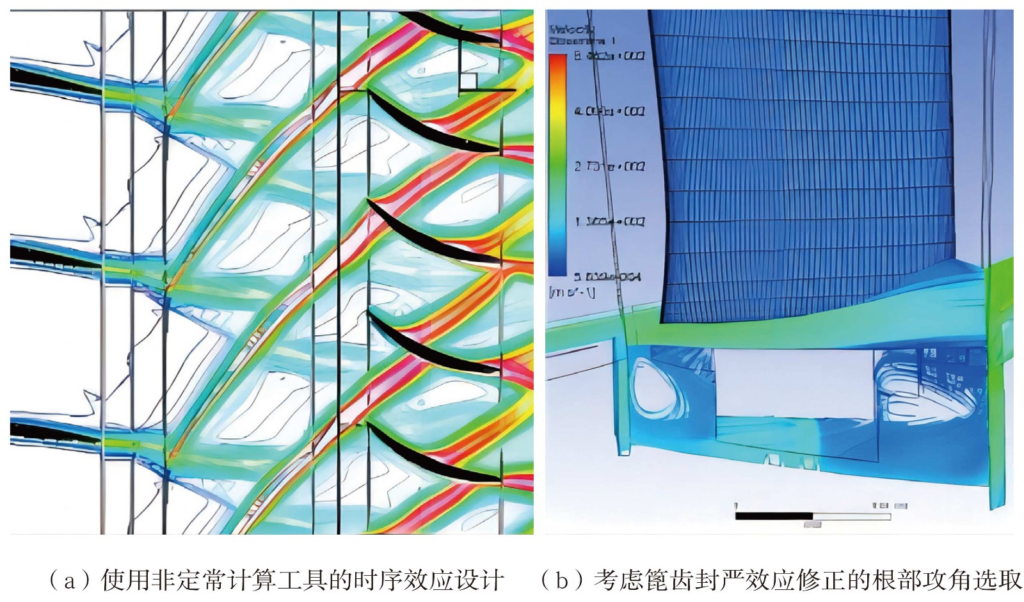
The third is the design of efficient air systems. The technical development directions of efficient air systems include the development of low-leakage, wear-resistant and efficient sealing technologies, such as honeycomb seals, thin-leaf seals, brush seals and combined seals; efficient drag reduction design technologies to improve air flow performance, such as de-swirl drag reduction design and flow efficient controllable design; advanced pre-swirl design technologies to further improve pre-swirl efficiency, such as aerodynamic pre-swirl hole design and cascade pre-swirl hole design; uncertainty quantification analysis methods that can improve the robustness and reliability of air systems, etc.
Conclusion
Aero-derivative gas turbines are widely used in ship power, electricity, mechanical transmission, offshore oil platforms, tank power and distributed energy due to their wide power range, high thermal efficiency, good maneuverability, long life and high reliability. With the rapid development of aviation engine technology and the continuous application of new designs and technologies, aero-derivative gas turbines will develop rapidly in the direction of high efficiency, low carbonization, new quality and digital intelligence. The design and manufacturing technology of aero-derivative gas turbines will also make great progress, gradually improve in terms of economy, low pollution emissions, reliability and maintainability, and the application prospects will inevitably be broader.