This is a case of turbine customization for an American customer. What the customer needs is the customization of gas turbine turbines. He has provided us with relevant requirements of drawings and materials, requiring us to manufacture turbines by casting, and requiring us to meet their drawing requirements with accuracy to ensure subsequent use. Successfully produced and delivered, the following is our casting process:
1. Material preparation
- The customer will first give us the drawings, we will have professional and technical personnel to analyze, and communicate with the customer about the relevant details, after confirming, we will start production.
- Material selection: Like the forging process, the casting of gas turbine turbines usually uses high-temperature alloys, such as nickel-based alloys, cobalt-based alloys, etc., to meet the performance requirements of high temperature strength, oxidation resistance and corrosion resistance.According to the requirements of this customer, we choose nickel base alloy.
- Smelting: The metal material of choice is put into a furnace to melt. The furnace type can be electric arc furnace, induction furnace or vacuum induction furnace, etc., according to the specific material and casting requirements to choose the appropriate furnace type.
- Alloying: According to the design requirements, different proportions of alloying elements are added to the melted metal, such as chromium, nickel, cobalt and other elements to improve the oxidation resistance, corrosion resistance and high temperature strength of the material.
- Molten metal treatment: Molten metal requires treatment before pouring, such as the removal of gases, impurities and inclusions to ensure the internal quality of the casting.
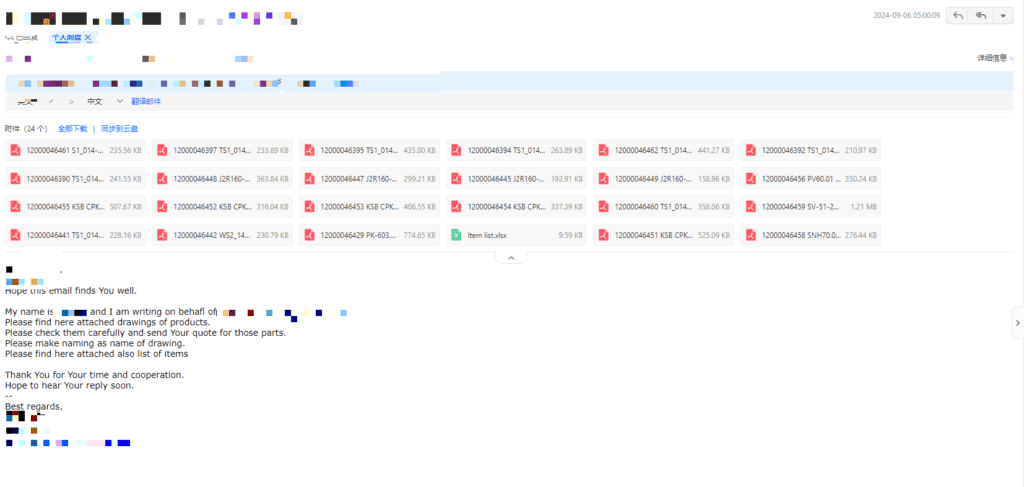
2. Mold preparation
- Mold preparation
- · Mold design: Design and manufacture of casting molds according to the final shape and size of turbine components. Mold materials usually use high-temperature and corrosion-resistant materials, such as steel, ceramics, etc.
- · Mold making: The process of mold making includes: mold processing, surface treatment, assembly, etc. In order to obtain high-precision castings, the accuracy and surface finish of the mold are very high.
- · Mold preheating: Before pouring, the mold needs to be heated to a certain temperature to ensure that the cooling rate and solidification process of the casting can be controlled.
3. Pouring
- Molten metal pouring: Molten metal is injected into the mold and ensures that the metal is evenly distributed in the mold to obtain the desired shape and size.
- · pouring temperature control: the pouring temperature needs to be strictly controlled, too high temperature will lead to porosity and cracks in the casting, too low temperature will lead to the casting can not fill the mold.
4. Cool and release
- Casting cooling: the casting is cooled and cured in the mold. The cooling process requires control of the cooling rate to avoid stress and cracks in the casting.
- · Stripping: After the casting has cooled, the casting is removed from the mold. The demoulding process requires careful handling to avoid damaging the casting.
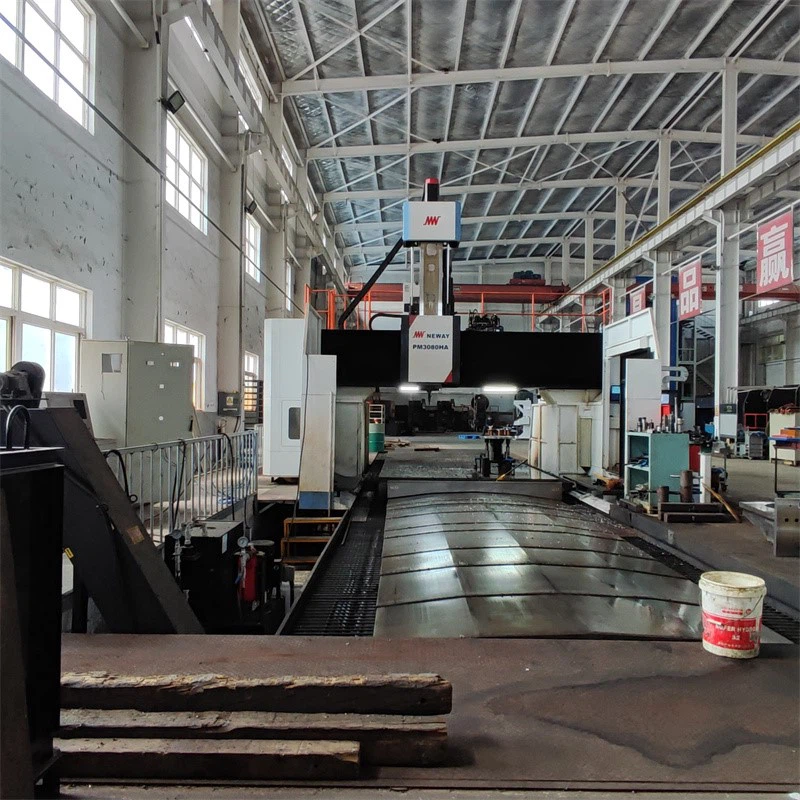
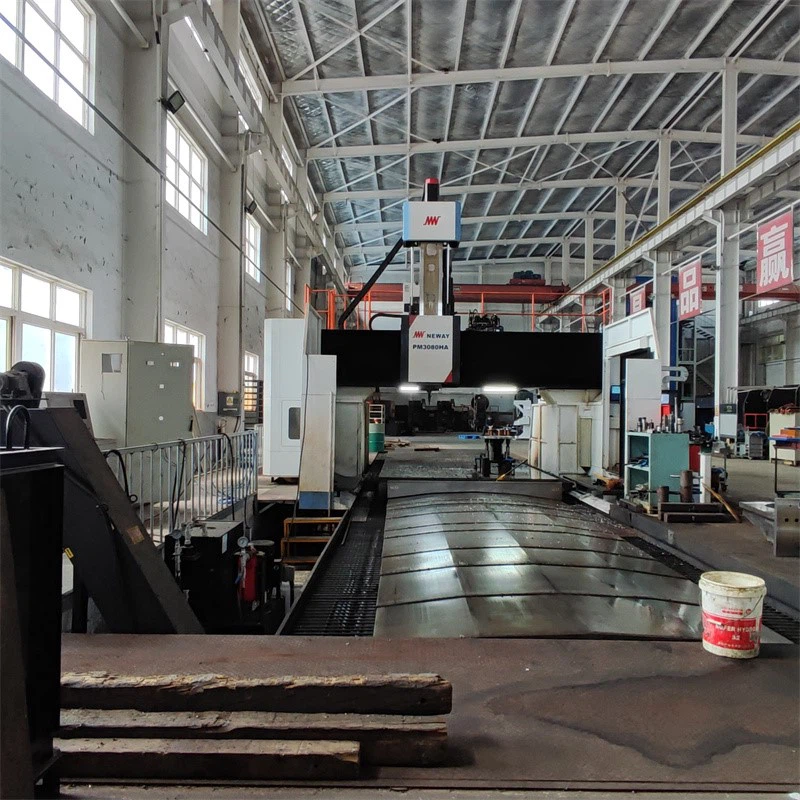
5. Follow-up Procedure
- Cleaning: clean the sand core, gate and flash on the surface of the casting.
- · Heat treatment: Heat treatment of castings to improve the mechanical properties of the material, such as improving strength, toughness, wear resistance, etc.
- ·CNC machining: Mechanical processing of castings, such as turning, milling, grinding, etc., to obtain the desired final size and accuracy.
- · Inspection: The cast turbine parts are inspected to ensure that they meet the design requirements and quality standards.
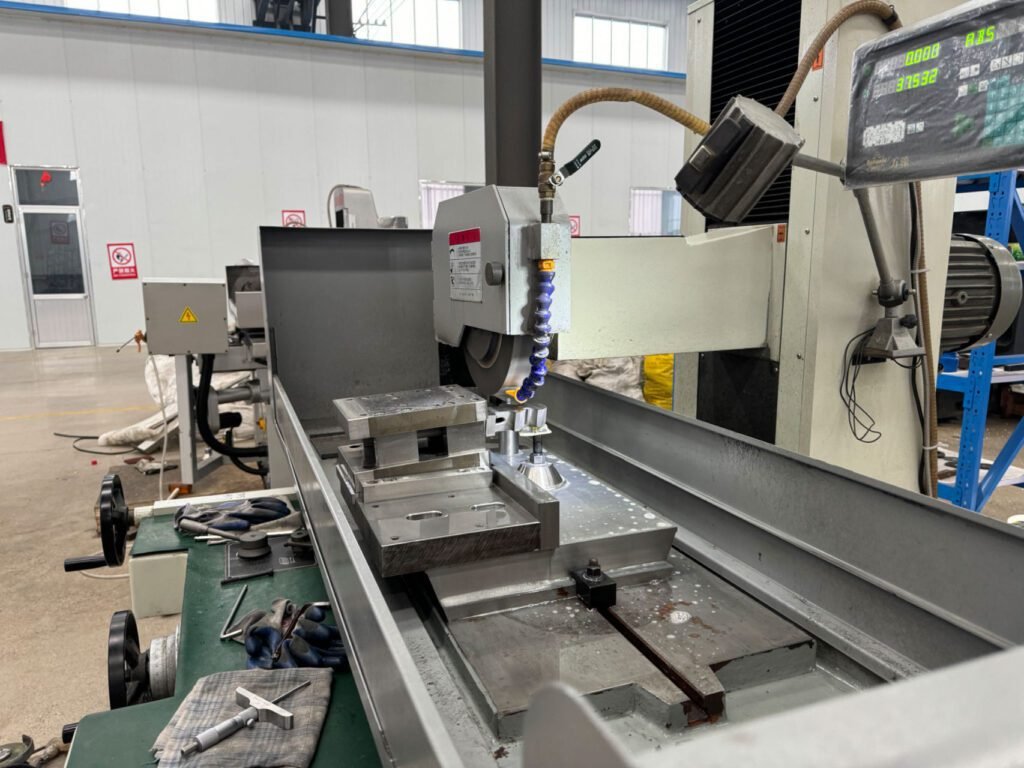
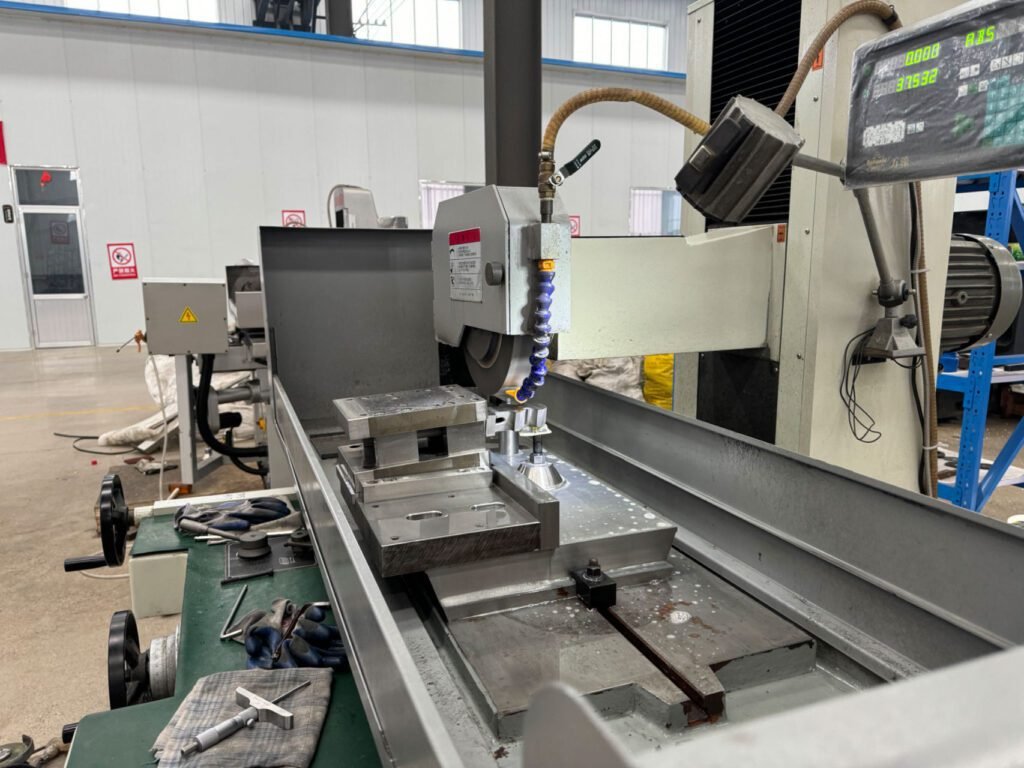
6.Cooperative communication and feedback
- Timely communication: In the casting process, we have been actively feedbacks to customers about the current progress, and ask customers’ opinions
- · Problem solving: In the process of mold making and machining, we timely communicate with customers about tolerances and other problems, and seek effective solutions to ensure the smooth progress of the project.
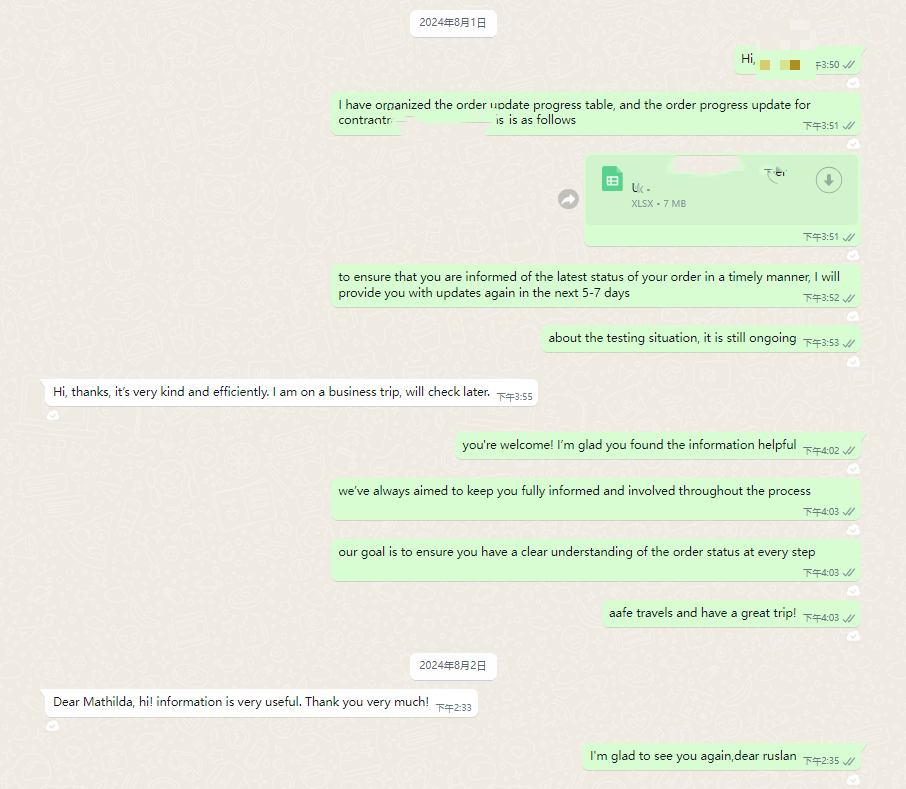
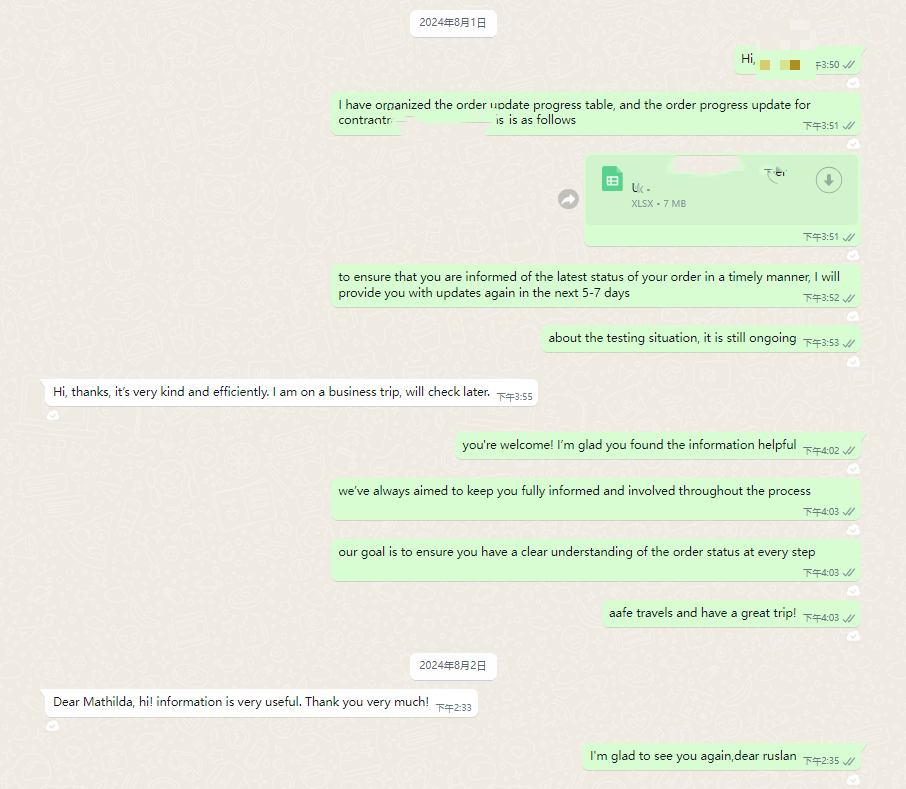
7. Advantages:
- Shape complexity: The casting process can manufacture parts with complex shapes that are difficult to process, such as turbine impellers with complex blade structures.
- Cost advantage: Compared with the forging process, the cost of the casting process is relatively low.
- Short production cycle: the production cycle of the casting process is shorter than that of the forging process. The casting process does not need to go through multiple pre-forging and precision forging like forging, and the cooling time of casting is also relatively short, so the production cycle is shorter and the market demand can be met faster.
- High material utilization rate: the casting process can effectively use materials and reduce material waste.
- Can manufacture large parts: casting process can manufacture large turbine parts, such as large gas turbine impeller. The forging process will encounter certain difficulties in manufacturing large parts, because it requires larger forging equipment and greater forging pressure.
We have advanced casting technology, specializing in the manufacture of various gas turbine turbine components, to meet your strict requirements for complex structure, high strength, high temperature resistance, corrosion resistance and other aspects. If you need it, contact us today for a customized solution!