The combustion chamber of an aeroengine works under high pressure and temperature, and after working for a period of time, it will become brown or even burnt, but after a series of maintenance processes, it can not only look like new, but also behave like new.
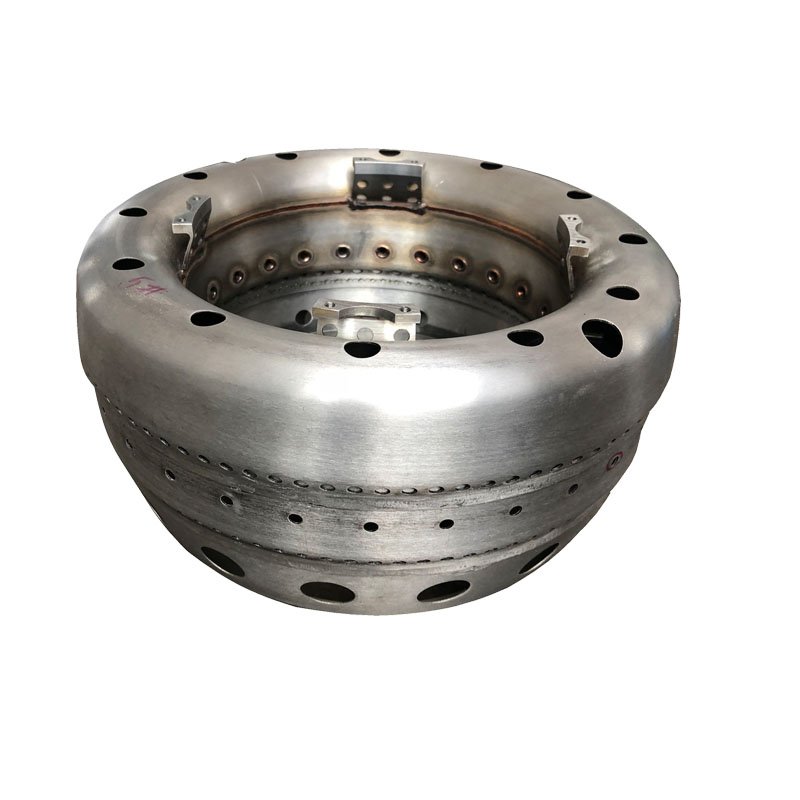
Take V2500 and CFM56-3 turbofan engines as an example. The combustion chamber is a short ring structure, and 20 vortex fuel nozzles spray fog fuel and air from the high-pressure compressor, which is ignited by the ignition nozzle to produce a constant combustion mode of low thermal stress.The V2500 combustion chamber is connected by the inner and outer rings through a tight fit. The dome of the outer ring is equispaced with 20 fuel nozzle guide rings, and matched with 20 coated tiles. The inner and outer rings are divided into 5 layers, each layer has 10 coated tiles, and the tiles are closely arranged so that the entire inner cavity is covered by the coating.
The top of the outer ring is near the No.7 ~ 8 fuel nozzle, that is, at the position of 4 ~ 5 o ‘clock, two ignition nozzle guide rings are successively distributed. There are 5 holes with bushing on the top side of the outer ring, which serve as the position for fixing the front end of the combustion chamber.The gas introduced by the large holes in the inner and outer ring walls is mainly used to reduce the inlet temperature of the high-pressure turbine except for a small part of the combustion. The gas entering from the small holes in the side walls is used to cool the walls and tiles through the comb gap behind the tiles.The inner ring is connected with the body through a flange, and the combustion chamber outlet is close to the first stage guide blade of the high-pressure turbine.




The CFM56-3 combustion chamber is composed of an inner ring, an outer ring, an inner cover, an outer cover and a dome cover. It is divided into 5 configurations according to whether the outer ring and the outer cover are welded or bolted, and whether there is a buffer. The dome covers 20 fuel nozzle guide rings distributed in two stages. The inner and outer covers are used to stabilize the flow.The inner and outer rings are an integral design, each lined with several layers of paneling, and the paneling is cooled by the gas introduced by the holes equidistant from the root.The outer ring has an ignition nozzle guide ring at 4 o ‘clock and 8 o ‘clock respectively, the interior of the combustion chamber is covered by coating, the front end is not fixed, and the connection mode of the back end (combustion chamber outlet) is the same as that of the V2500.
Step 1: Disassemble
The inner and outer rings of the V2500 combustion chamber are fitted together and easily disassembled. The shingles are individually replaceable and are bolted to the inner and outer rings.The fuel nozzle guide ring has two parts inside and outside, and it is necessary to polish off the two joint solder joints before they can be unscrewed, which is also the first step to completely decompose the outer ring.
The CFM56-3 combustion chamber needs to be removed only if the defect exceeds the scope of service or if a component needs to be replaced or repaired, which starts with polishing off the solder joints that hold the external bolts, which have 40 bolts in one configuration and 80 in the other.When these bolts are removed, the combustion chamber is broken down into 5 or 4 parts (with the outer ring welded together with the dome cover). Other parts, including the paneling, are welded structures and cannot be simply disassembled.




Step 2: Wash
The V2500 can be cleaned with hot water. If it is very dirty, it can be soaked in alkali solution (82 ~ 93℃) for 30 ~ 90min, and then cleaned with hot water. According to the level of maintenance, decide whether to do FPI.
The CFM56-3 is recommended for steam cleaning (100 ° C), which is available in stationary and portable types.
Step 3: Check
The V2500 combustion chamber can be disassembled into inner and outer rings, cleaned and sent for inspection. Damage to the inner and outer rings is usually cracks or ablation, which can be repaired by welding.The size of the place where the inner and outer rings are matched and the place where the outer rings are matched with the body should meet the requirements, and a certain roughness should be maintained, otherwise spray repair should be carried out. Whether the tile is well connected to the inner and outer rings should be determined by measuring the gap between them, and the Angle of the fuel nozzle guide ring and the plane is between 9°52 ’30 “and 13°52′ 30”.
The radial movement range of the fuel nozzle guide ring must be greater than 3.048mm, otherwise it should be replaced.The inspection methods for CFM56-3 combustion chamber cracks, ablation and coating loss are similar to those for V2500. However, if the coating is damaged, the tile cannot be replaced like the V2500, and can only be re-sprayed.
A model of the combustion chamber, the outer cover are brazed connections, if there is damage to the vacuum brazing repair.The first stage fuel nozzle guide ring must be able to rotate freely, but the rotation range cannot exceed 360°, otherwise it must be repaired.
The stage 2 fuel nozzle guide ring is stationary. Each sealing edge of the inner and outer rings can be repaired by spraying or welding if damaged.After the combustion chamber is divided into several parts, each part should be installed on its own inspection fixture to check the size and position.These parts of the combustion chamber are easily deformed and can be corrected with specialized tools (such as hydraulic devices).


Step 4: Repair and coating
V2500 interior and outer ring repair: when cracks or ablation of the inner and outer ring wall exceeds the range of direct welding, it is necessary to repair the stitching.The repaired material may be made of the same material and thickness as the ring wall, or may be cut from the same location of other available combustion chambers.
To polish off the cracked or ablated part of the repair part first, the cut sheet must be made into the same shape as the damaged part (the gap between the sides of the damaged part should be kept within 0.381mm), and then fixed by spot welding method. After welding and polishing, drill holes should be drilled. Existing holes can be used as templates to mark the location of drilling holes. Then use laser drilling, drilling machine or EDM and other ways to drill, you can also make the same hole as the original by hand.


Finally, the heat treatment is to release the stress (the maximum temperature is 990℃), and do FPI inspection.Combustion chamber servicing of CFM56-3 involves a lot of welding repairs because component replacement is done by welding.As a thin-walled part, it must be installed to prevent deformation during welding. This section describes the repair of TBC(Thermal barrier coating) applied to the inner, outer ring and dome cover lining.The coating of the lining consists of two layers: the base coating CP6023(nickel chromium aluminum yttrium) and the surface coating CP6024(zirconium yttrium). There are 2 ways to remove the coating:
The first is to remove the two coatings at the same time with high-pressure water (138 ~ 410kN/m2), allowing 5% of the bottom coating residue and 0.03mm of the base material to be removed per repair. It is then annealed to enhance the weldability of the part and restore its ductility.The second removes the top coating with alumina dry blown sand. After cleaning, do annealing treatment.


Then prepare a solution to remove the bottom coating: mix equal parts of hydrochloric acid solution and nitric acid solution at 16℃, and then soak the parts for 3 ~ 4h(21℃), and then rinse with cold and hot water and dry. If necessary, the residual coating is removed with alumina dry blown sand.
Coating spraying: First of all, protect the position that is not sprayed, clean the sprayed surface with alumina dry blown sand, plasma spray the bottom coating (0.1 ~ 0.15mm), spray the surface coating (0.20 ~ 0.30mm) within 2 hours after spraying the bottom coating, or 0.33 ~ 0.43mm for thick coating spraying.
Thank you for your interest in our company! As a professional gas turbine parts manufacturing company, we will continue to be committed to technological innovation and service improvement, to provide more high-quality solutions for customers around the world.If you have any questions, suggestions or cooperation intentions, we are more than happy to help you. Please contact us in the following ways:
- WhatsAPP:+86 135 4409 5201
- E-mail:peter@turbineblade.net