inhibition technique
The excellent properties of single crystal superalloy are mainly due to the elimination of grain boundaries of single crystal blades, and recrystallization will significantly reduce the high temperature resistance of the original single crystal alloy. After single crystal blade casting, it is necessary to carry out gas film hole processing, tenon tooth grinding, edge plate side milling, blade tip casting process hole welding, heat treatment, assembly and other follow-up processing work. In the process of engine operation, the blade is subjected to hot and cold air impact and high temperature, huge load and violent vibration during high-speed rotation, and recrystallization is possible. There have been several turbine blade failures. Therefore, in recent years, research at home and abroad has adopted pre-recovery heat treatment, carburizing, coating and removal of surface deformation layer and other related methods to inhibit recrystallization and add boundary strengthening elements to the recrystallization repair work.
3D printing technology
3D printing, also known as additive manufacturing, integrates CAD, CAM, powder metallurgy, laser processing and other technologies. Using 3D printing technology, we can turn the thinking of the “brain” into a three-dimensional entity, and print the image of a part on the computer into a “real” part. 3D printing technology has made a “revolutionary” change in manufacturing technology and processing concept. Monash University in Australia has successfully produced the world’s first 3D printed jet engine. At the same time, it is also working with Boeing, Airbus Group and Safran Group to provide 3D printed engine prototypes for Boeing and others for flight testing. With 3D printing technology, the manufacturing time of engine parts can be reduced from three months to six days.

In China, 3D printing technology was used to repair and reuse the blade tip wear parts of turbofan engine high-pressure compressor rotor blades. 3D printing technology has been used to manufacture non-bearing parts and static parts on the engine, but the mechanical properties of the parts are being actively evaluated, at the same time, the use of 3D printing technology to manufacture engine rotor parts, bearing parts, etc., has also carried out extensive research.
Blade exhaust edge (front and rear edge) processing technology
The machining quality of inlet and exhaust edge of aero engine blade is one of the key factors affecting the aerodynamic performance of aero engine. The inlet and exhaust edge is also the defect prone part of the blade and the defect sensitive area of titanium alloy. A large number of engine failure events are caused by the machining defects of the inlet and exhaust edge of the blade. Because the inlet and exhaust edge of the blade is the thinnest part of the blade and the edge of the blade, its rigidity is poor and the processing deformation is large, and the inlet and exhaust edge of the blade processed often appears square and pointed. In the mass production of engine blades, the key technological problems of high efficiency and high quality blade inlet and exhaust edge processing have not been completely solved.
Adaptive processing technology
Adaptive machining technology is divided into three forms, namely, adaptive planning of tool position trajectory, adaptive control of numerical control system and adaptive machining combined with digital detection [3]. In China, adaptive machining technology has been successfully applied in precision forging/rolling blade machining, damaged blade repair and linear friction welding monolithic blade disc machining. Although adaptive machining technology has made breakthroughs and development in theory and practice, the engineering application of adaptive machining technology is still a hot research technology in aero engine manufacturing.
Anti-fatigue manufacturing technology
Material fatigue and surface machining defects have become the main causes of aero engine parts failure, and the failure has become a growing trend, so “anti-fatigue manufacturing” has become a hot technology in aero engine manufacturing. Anti-fatigue manufacturing technology refers to the manufacturing process that improves the fatigue life of parts by changing the organization and stress distribution of materials in the manufacturing process of parts without changing the material and section size. The fatigue life is mainly affected by thermal treatment, environmental corrosion, surface quality, stress concentration, surface stress and other factors. The main method of anti-fatigue manufacturing is to reduce stress concentration and improve the surface strength of parts. Reducing stress concentration is to ensure the integrity of the machined surface, and the best way to improve the surface strength of parts is shot peening. In the process of aircraft engine anti-fatigue manufacturing, a variety of new shot peening media have been developed in the traditional shot peening process, and the new technologies of laser shot peening, ultrasonic shot peening and high pressure water shot peening have been widely used.
Bird strike prevention technology
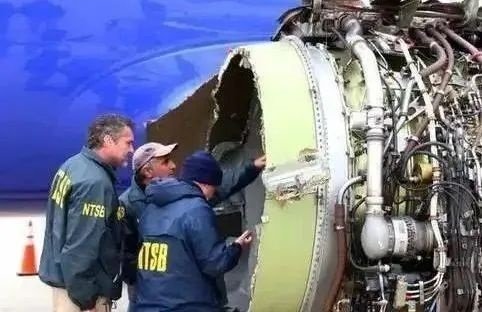
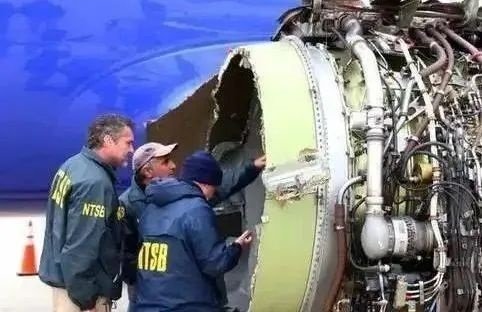
The frequent occurrence of bird strikes has become an unavoidable problem in the development of aero engines, and extensive research has been carried out at home and abroad. In July 2015, the United States FAA issued the “Bird strike Requirements for transportation aircraft” notice, which not only put forward specific requirements and regulations for the future bird strike prevention and foreign object injury prevention of aircraft engines, but also pointed out another new research direction for the development of new engine materials and new structure manufacturing technology.