As a digital engine to accelerate the development of aircraft engines, the full three-dimensional simulation technology of the whole engine can realize high-precision and rapid prediction of the full three-dimensional performance of the whole engine in the virtual digital space, solve the problem of engine matching, shorten the R&D cycle, reduce development risks and costs, realize the paradigm shift from traditional design to predictive design, and accelerate the development process of aircraft engines.

The development of traditional aircraft engines adopts a serial development model of “design, test verification, design modification, and re-testing” that is repeated and iterated. In particular, the performance of the whole engine needs to be verified through a large number of tests, which will lead to a long verification cycle, high test costs and risks, and cannot meet the current needs of rapid development of aircraft engines [1-2]. At present, the whole engine performance evaluation method mainly remains in the one-dimensional stage. The parameter transfer accuracy and dimension between various components are relatively low, which greatly affects the accurate evaluation of the engine performance parameters [3]. With the rapid development of computational fluid dynamics (CFD) technology and information technology, full three-dimensional simulation of the whole engine has become possible. This technology can predict the whole engine performance under steady-state conditions, estimate the matching working state between components, guide the integrated design between components, and provide a technical basis for component design. At the same time, whole engine simulation work helps to promote the development of aircraft engine whole engine research and development from one-dimensional to three-dimensional design, greatly improve the overall design accuracy and level of aircraft engines, and further improve the aircraft engine design system.
Study plan
In order to quickly form the full three-dimensional simulation capability of the whole machine and accelerate the transformation and application of the whole machine simulation technology in the engine engineering development, it is urgent to improve the simulation accuracy and speed up the simulation progress. To this end, the innovation team proposed a research plan for the CFD simulation method of the whole aircraft engine in accordance with the idea of forward development of aircraft engines, as shown in Figure 1. On the one hand, in order to improve the simulation accuracy of the whole machine, a set of whole machine simulation methods and tools suitable for engineering use are formed by conducting research on complex model modeling methods, grid generation technology, high-precision solution algorithms and other methods of the whole machine; on the other hand, in order to speed up the simulation progress and shorten the whole machine simulation cycle, a set of standardized whole machine simulation platforms are developed to optimize the simulation process, integrate core algorithms, and solidify simulation experience. Finally, a full three-dimensional simulation design system for the whole machine is established to support the rapid development of aircraft engines.
Key technologies
The key technologies of full 3D simulation of the whole machine mainly include high-fidelity model construction technology, component interface data transmission technology, full 3D matching technology of the whole machine, and integration technology of the whole machine CFD simulation platform. In order to overcome the above key technologies, the following 6 research works have been carried out.
High-fidelity geometry modeling and meshing
In order to improve the fidelity of the whole engine model, a study was conducted on the method of quickly acquiring the high-fidelity geometric model of the whole engine. In order to improve the accuracy of the model, the real technical status of each component of the engine was comprehensively sorted out, such as the root tip clearance of the adjustable guide blades of the fan and compressor, the axial and radial clearances of the turbine blades, the adjustable nozzle throat area, etc., to improve the fidelity of the engine model. The rapid processing method of the high-fidelity physical model of each component of the whole machine was mastered. The impeller components directly use customized blade output files, and the output is converted into a standardized format through program conversion. The combustion chamber, afterburner, nozzle, etc. use computer-aided design (CAD) software to generate three-dimensional entities, and the detailed structure is appropriately simplified. This method solves the key technology of high-fidelity geometric modeling of the whole machine complex model, and completes the interface division of the whole machine complex model and the construction of the internal flow domain model.
Subsequently, a study on the rapid meshing method of the whole machine geometric model was carried out. The meshing of conventional compressor flow paths and turbine flow paths can be generated using a templated full hexahedral meshing tool, but for some very complex geometric models, such as the engine duct, combustion chamber, afterburner and nozzle, an unstructured mesh generation tool is required. By deeply studying the meshing strategy of complex structure meshes, the influence of key parameters of geometric structures on the meshing results is refined and summarized, and finally an automated meshing script file is generated to achieve automated and rapid meshing of hundreds of millions of grids. This method completes the meshing of complex models of various components of the whole machine, and completes the mesh model of the whole machine in series, as shown in Figure 2.
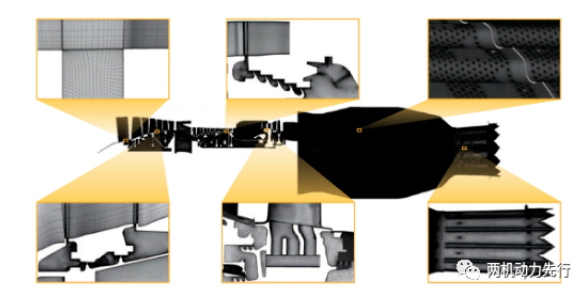
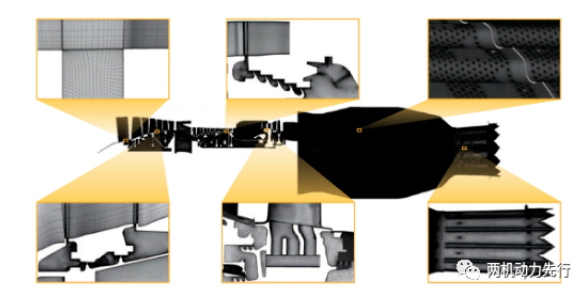
High-precision coupled simulation of compressible and incompressible flows
In order to solve the problem of simulation of coupling of compressible flow and incompressible flow, the simulation method of coupling between high-speed compressible flow of engine fan, compressor, turbine and low-speed incompressible flow of combustion chamber and component disc cavity was studied. The focus was on the study of solution method of coupling between combustion chamber and turbine components. From the simulation results of coupling between engine combustion chamber and turbine, it can be seen that the velocity in the core area of the main combustion chamber is very low, which belongs to incompressible flow, and the turbine guide vane area is a high-speed compressible flow. Through multi-dimensional selection of turbulence model parameters and setting of interface data transfer parameters, we finally realized the high-precision coupling simulation of the main combustion chamber and turbine (see Figure 3), and obtained the high-precision coupling data transfer method of incompressible flow and compressible flow parameters.

