Turbine blade is the core hot end component of gas turbine, its research and development and manufacturing is an important reflection of the development scale and technical level of a country’s industry. The recent research progress of gas turbine blade preparation technology is reviewed. Based on the research of the research group, the research progress in the field of directional solidification of gas turbine blades is introduced, and the focus direction is put forward.
1.Directional solidification technology
Directional solidification technology refers to a technology that establishes a temperature gradient in a certain direction by forced means during the solidification process, so that the solidification proceeds along a certain direction. In the solidification process of a metal, there is a temperature gradient in a specific direction between the solidified part and the unsolidified melt, which causes the metal to solidify in the direction opposite to the heat conduction. By using directional solidification technology, columnar or single crystal with specific orientation can be obtained, and the columnar or single crystal blade can be prepared, and its performance can be significantly improved.
In the late 1960s, Versnyder et al. applied directional solidification technology to the production of superalloys, which better controlled the grain orientation of the solidification structure, eliminated the transverse grain boundaries, and greatly improved the mechanical properties of superalloys. Directional solidification technology after decades of research, developed exothermic powder (EP) method, power down (PD) method, high rate solidification (PD) method, Conventional techniques such as HRS [12] and liquid metal cooling (LMC). At present, the high-speed solidification method and liquid metal cooling method are widely used.
1.High-speed solidification method
High speed solidification method is a method to make castings move in one direction gradually away from the high temperature region to achieve single direction solidification. This method improves the problem that the temperature gradient decreases gradually in the solidification process. The principle of high-speed solidification method is shown in Figure 1(a). An adiabatic baffle is set at the bottom of the furnace, and a mouth slightly larger than the casting is opened on the baffle. The interior of the furnace is kept heated. During the solidification process of the metal, the shell is slowly pulled down, so that the part of the metal exposed to the outside begins to cool and solidify, while the metal melt located in the furnace is still in a heated state, thus establishing an axial temperature gradient. The high speed solidification method has a high and stable temperature gradient and cooling rate, and can obtain a long columnar crystal and a fine structure, thus greatly improving the mechanical properties of the castings, but the temperature gradient of the method is still insufficient, and casting defects such as freckles and impurities are still prone to occur during directional solidification of thick and large castings.

Fig. 1 Schematic diagram of directional solidification process
2.Liquid metal cooling method
In order to further improve the temperature gradient in directional solidification, the researchers developed a liquid metal cooling method based on the rapid cooling method. This method uses liquid metal to cool castings, that is, the extracted castings are immersed in liquid metal with high thermal conductivity, high boiling point and low melting point (Sn is used in the mainstream) (see Figure 1(b)) to increase the cooling effect. Liquid metal cooling method can improve the cooling rate of castings and the temperature gradient of the solid-liquid interface, up to 200 K/cm, and can maintain a stable temperature gradient, so that the crystallization process is stable, so that the dendrite spacing can be significantly reduced, and the probability of various solidification defects can be reduced. However, the liquid metal cooling method also has some limitations, such as: the equipment required by the method is complex, and it is not simple enough in practical operation; The cooling medium Sn is a harmful element, and when the casting is immersed in low-melting metal such as Sn, Sn liquid is easy to penetrate and pollute the casting. In recent years, people have optimized the process from the aspects of shell preparation, and improved the shortcomings of liquid metal cooling process, which has been applied to the production of single crystal turbine blades for aero engines and large size single crystal turbine blades for ground gas turbines.
In addition, new ways of increasing the temperature gradient are constantly being explored, such as: Gas cooled casting directional solidification technology, electromagnetic constrained forming directional solidification technology, supercooling directional solidification, SDS), laser rapid solidification (LRM), fluidized bed quenching directional solidification technology, two-dimensional directional solidification technology (bidirectional solidification, BDS), thin shell casting directional solidification technology. However, these new technologies are still immature and have not been applied in directional solidification of gas turbine blades.
3.Liquid metal spray enhanced cooling method
In order to overcome the problems such as casting may be contaminated by liquid metal coolant and casting defects easily formed by liquid metal cooling method, our research group developed liquid metal spray cooling (LMSC) directional solidification technology, and developed industrial directional solidification equipment. The design structure and object of LMSC directional solidification furnace are shown in Figure 2. LMSC technology is based on LMC technology from the original way of directly dipping shell and casting into liquid metal liquid for cooling, to the use of liquid metal liquid for spray cooling of shell and casting. The technology has the characteristics of strong heat dissipation, uniform cooling and good heat insulation between the insulation zone and the cooling zone. LMSC technology not only retains the advantages of strong cooling capacity of LMC technology, but also solves the disadvantages of LMC technology. Due to the controllable flow rate of the liquid metal liquid sprayed, combined with the adjustment of the withdrawal rate, columnar crystals or single crystals with good structure and smaller dendrite spacing can be obtained, which can reduce or even avoid the formation of solidification defects in superalloy. LMSC directional solidification technology is very important for the development and industrial production of superalloys.


Fig. 2 LMSC directional solidification furnace
4.Regulation of the solidification structure of superalloy by magnetic field
The application of electromagnetic field in the metallurgical process can strengthen the metallurgical reaction process, implement process control and prepare new materials through electric, magnetic, thermal, and force effects, which opens up a new way for controlling and improving the organization and properties of metal materials. Around the magnetic field metal refining, solidification control, solid phase change structure control, etc., Shanghai University, Northeastern University, etc., carried out a lot of research, and achieved a number of innovative results.
The magnetic field can produce multiple effects in the process of directional solidification, thus affecting the microstructure and composition distribution, so as to improve and control the solidification microstructure and composition distribution. Therefore, directional solidification under magnetic field has important academic significance and practical application value.
5. Influence of magnetic field on heterocrystal defects
The application of static magnetic field can significantly affect the nucleation process. Li et al. found that the application of static magnetic field will increase the surface tension of melt, and the resistance needed to overcome nucleation will be greater, thus effectively inhibiting the nucleation process. The results show that the application of strong static magnetic field can effectively inhibit the formation of heterocrystals in single crystal superalloy. As can be seen from FIG. 3 and 4, whether in the initial area of seed remelting of the leaves or in the platform area of variable cross-section, the application of enhanced static magnetic field at a certain pulling speed can effectively inhibit the nucleation and growth of heterocrystals and obtain relatively complete dendrite structure. The reason is that the strengthening of static magnetic field can effectively increase the nucleation subcooling degree of superalloy melt, thus inhibiting the formation of impurity crystals, which opens up a practical and effective way to control the microstructure defects of single crystal superalloy.


Fig. 3 Microstructures near melt-back interface for superalloy with and without an 8 T magnetic field


Fig. 4 Microstructures near the solid-liquid interface for superalloy with and without a 12 T magnetic field
2. Influence of thermoelectromagnetic flow on solidification structure
The results show that the thermal current will be formed at the solidification interface due to the existence of temperature gradient. When the magnetic field is applied, the thermal current and the magnetic field are coupled to produce thermoelectric magnetic convection (TEMC), which then causes various solidification phenomena. The solidification evolution of nickel-based single crystal superalloy under static magnetic field has been systematically studied in terms of dendrite, γ ‘γ’ phase, eutectic and element segregation. As for the evolution of dendrite structure, our research group [30] found that applying a magnetic field of 5 T can reduce the primary dendrite spacing of PWA1483 and CMSX-4 monocrystalline alloys, and the results are shown in Figure 5. The decrease of primary dendrite arm spacing (PDAS) is caused by thermo-electromagnetic convection between dendrites under high magnetic field. For the evolution of γ ‘γ’ phase, it was found that the application of 5 T magnetic field could reduce the size of γ ‘γ’ phase in PWA1483 and CMSX-4 single crystal alloys by 26% to 30%, and the γ ‘γ’ phase remained cubic, as shown in Figure 6.


Fig. 5 Transverse microstructures of superalloy PWA1483 and CMSX-4 without and with a 5 T magnetic field


Fig. 6 Morphologies of the γ′γ′ phase in the dendrite core of superalloy PWA1483 and CMSX-4 without and with a 5 T magnetic field
For element segregation, Khine et al. believe that the rate of thermoelectromagnetic convection can completely reach the order of magnitude of redistribution of solute elements in the microscopic scale. When our research group studied magnetic field assisted directional solidification of nickel-based single crystal superalloys, it was found that the solute distribution of the samples solidified in static magnetic field was more uniform along the longitudinal section. At the same time, the application of magnetic field also plays a regulating role in the segregation of elements in different parts of the dendrites, and the application of magnetic field makes the segregation coefficient of most elements gradually close to 1(see Figure 7).


Fig. 7 Segregation coefficients of alloy elements in the superalloy PWA1483 and CMSX-4 samples produced without and with a 5 T magnetic field
3. The control of magnetic field on the microstructure of superalloy heat treatment
During the solidification process of superalloy, due to the different solubility of solute elements in the solid phase and the liquid phase, the positive segregation elements are enriched in the liquid phase, and the negative segregation elements are enriched in the solid phase. As a result, a large number of (γ+γ ‘γ+γ’) eutectic phases, carbides, Laves phases and topologically close-packed (TCP) phases are generated between dendrites and grain boundaries, which reduces the mechanical properties of superalloys. The composition segregation can be effectively improved by heat treatment, and the harmful phases such as eutectic, Laves phase and TCP phase can be eliminated. However, with the gradual increase of refractory elements in high generation alloys, coupled with the difficulty of heat and mass transfer in thick and large blades and the increase of stress, new problems have been raised for heat treatment. By placing the workpiece in the furnace equipped with electromagnetic field heat treatment, the magnetic effect of electromagnetic field affects the element distribution of the material, so as to improve the microstructure and material properties, and shows a broad prospect for development.
This research group studied the effects of heat treatment under static magnetic field (SMF) and alternating magnetic field (AMF) on the microstructure and properties of nickel-based superalloys. The mechanism of microstructure and properties of heat treatment under magnetic field is discussed. The results show that magnetic field has significant influence on microstructure and properties of heat treatment of nickel-based superalloy. By applying a static magnetic field to DZ483 heat treatment, it is found that SMF can reduce the average size of γ ‘γ’ phase. According to precipitation hardening theory, Orowan process is the main deformation mechanism of DZ483 superalloy, so after heat treatment under SMF, it shows better mechanical properties, Vickers hardness and tensile strength increase (see Figure 8 and Table 1). The change of the shape and size of γ ‘γ’ phase is mainly due to the decrease of the diffusion rate of alloying elements. After aging treatment of DZ417G under strong static magnetic field, it was found that the precipitated γ ‘γ’ phase was small and dispersed, the size was reduced by about 12%(see Figure 9), and the microhardness was finally increased by about 8.4%.
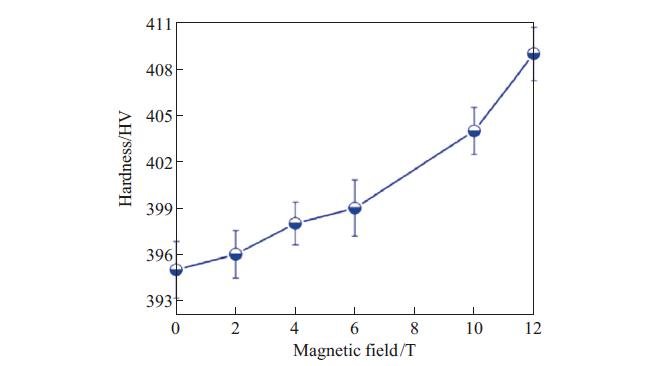
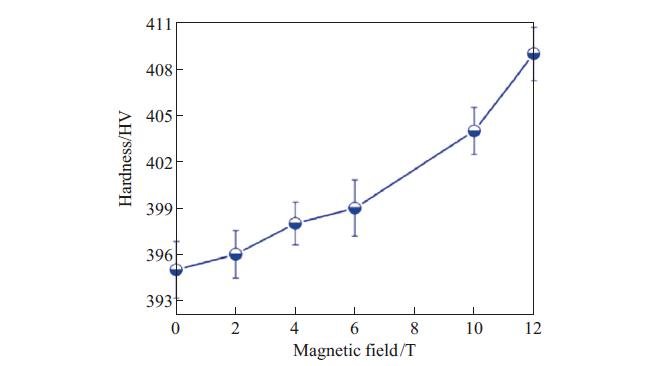
Fig. 8 Variation of the Vickers hardness of DZ483 with the SMF intensity
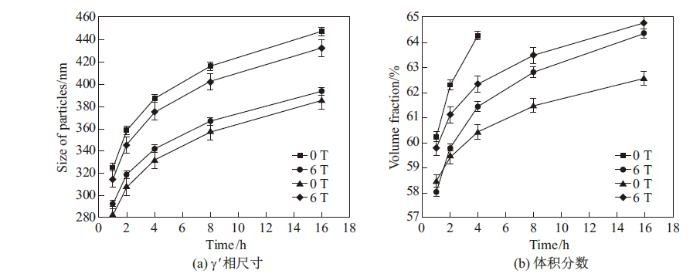
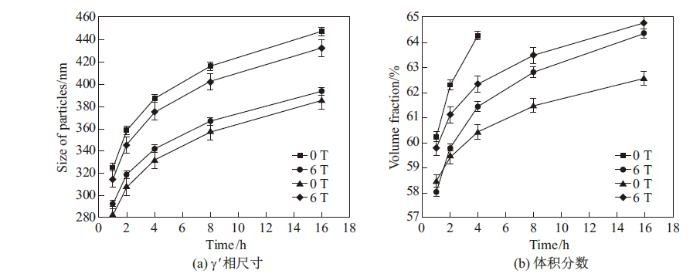
Fig. 9 Dependence of size and volume fraction of γ′γ′ phase on the time of ageing treatment with and without magnetic field


Table 1 Tensile properties of DZ483 samples heat treated with and without the SMF of 12 T
The results show that the application of alternating magnetic field can increase the diffusion rate and improve the macroscopic and microscopic segregation states. Based on the characteristics of AMF, the research group carried out a study on the precipitation and segregation behavior of γ ‘γ’ in the heat treatment of DZ483 superalloy under AMF. The results in FIG. 10 show that the application of AMF significantly improves the diffusion coefficient of elements for solid solution treatment; In the subsequent aging treatment, the overall segregation level decreased. This indicates that AMF can effectively reduce the composition segregation of alloying elements.
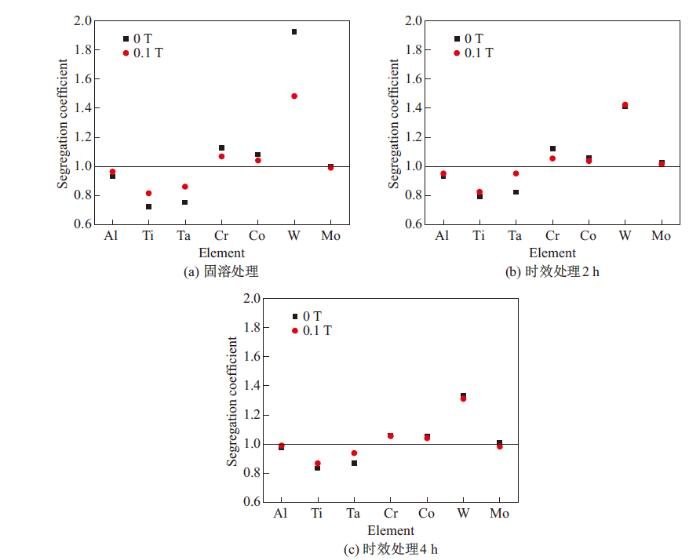
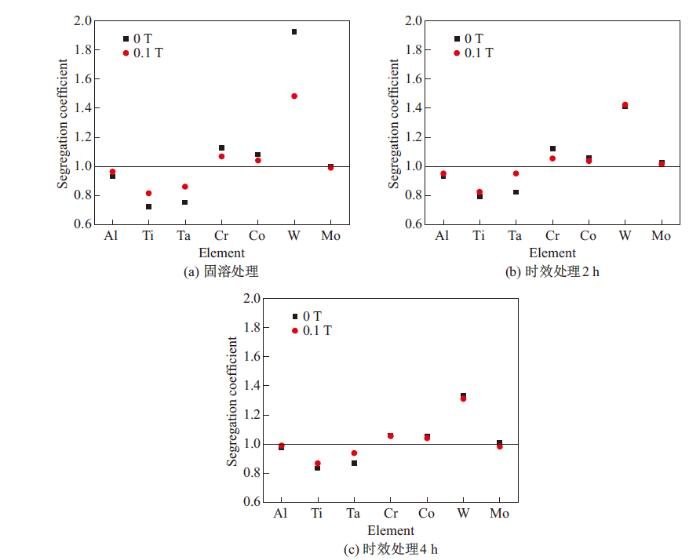
Fig. 10 Segregation coefficients of alloying elements in the DZ483 superalloy after solution treatment with and without AMF
Solution treatment and aging treatment under alternating magnetic field can effectively reduce the micropore size and volume fraction of single crystal samples. As shown in FIG. 11, compared with the condition without magnetic field, The micropore size and volume fraction decreased from 15.6μμm, 0.126%(0 T) to 12.2 μμm and 0.081%(0.1 T), respectively, after applying 0.1T magnetic field, indicating that heat treatment under magnetic field can effectively improve the microstructure properties of superalloys and obtain longer service life. As for the evolution of phase and eutectic structure, our research group found that with the increase of magnetic field intensity, the cubic degree and volume fraction of γ ‘γ’ phase in the alloy increased, while the content of residual eutectic decreased (see Figure 12).


Fig. 11 Microporosity distribution of the cast sample and solution heat treatment sample
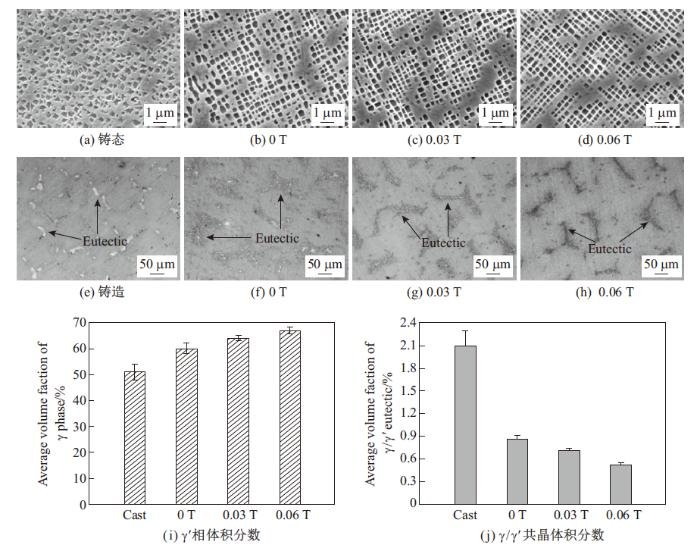
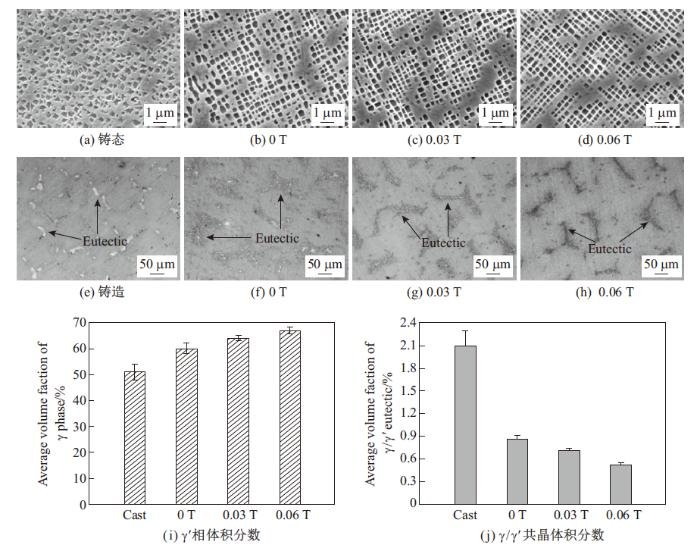
Fig. 12 Morphologies of γ′γ′ precipitate of cast sample and heat treatment samples with various alternating magnetic fields
The application of electromagnetic field greatly improves the heat treatment structure, not only improves the performance of the material, but also improves the heat treatment efficiency, showing unique advantages. The results of this research group show that the electromagnetic field can significantly reduce the thickness of the recrystallization layer, and even eliminate the recrystallization layer. Therefore, the heat treatment of superalloys under electromagnetic field has a broad application prospect and is being continuously developed.
Application of magnetic field in heat treatment can significantly improve the properties of superalloys. The 0.06T alternating magnetic field was applied to the alloy PWA1483 during solution and aging treatment, and the results were shown in Figure 13. Compared with the sample heat treated without magnetic field, in 980. The creep rupture life at C and 250 MPa is increased from 62 h to 106 h, which is due to the enhancement of element diffusion and decrease of segregation during heat treatment under alternating magnetic field, and the decrease of internal porosity of the sample, thus increasing the creep life of the sample.


Fig. 13 Creep curves of heat treatment samples without and with a 0.06 T alternating magnetic field at 980 ∘∘C/250 MPa
Thank you for your interest in our company! As a professional gas turbine parts manufacturing company, we will continue to be committed to technological innovation and service improvement, to provide more high-quality solutions for customers around the world.If you have any questions, suggestions or cooperation intentions, we are more than happy to help you. Please contact us in the following ways:
- WhatsAPP:+86 135 4409 5201
- E-mail:peter@turbineblade.net