Guide vanes are critical components in gas turbine engines, responsible for directing the flow of hot, high-pressure gases onto the turbine blades. Their precise design and exceptional material properties are paramount to the engine’s efficiency, power output, and lifespan. At BLAZE, we specialize in the design and manufacture of high-performance guide vanes, utilizing the superior characteristics of Inconel 939 to deliver unparalleled performance in even the most demanding applications.

Inconel 939: A Superior Material Choice
The selection of material for guide vanes is crucial, as these components face extreme temperatures, pressures, and corrosive environments within the gas turbine. Inconel 939, a nickel-based superalloy, stands out as a superior choice due to its exceptional combination of properties:
- High-Temperature Strength: Inconel 939 maintains its structural integrity and strength at extremely high temperatures, far exceeding the capabilities of many other alloys. This allows for efficient operation at elevated temperatures, maximizing the power output of the gas turbine engine. The alloy’s excellent creep resistance ensures dimensional stability even under prolonged exposure to high temperatures, preventing deformation and maintaining the precise airflow management crucial for optimal performance.
- Exceptional Oxidation Resistance: In the harsh environment of a gas turbine, oxidation is a significant concern. Inconel 939’s exceptional oxidation resistance minimizes material degradation, extending the service life of the guide vanes and reducing the need for frequent replacements. This translates to significant cost savings and reduced maintenance downtime.


- Excellent Corrosion Resistance: Exposure to corrosive gases and combustion byproducts can lead to premature failure of guide vanes. Inconel 939 provides exceptional resistance to corrosion, ensuring the long-term reliability and durability of the components. This resistance to corrosion ensures that the guide vanes maintain their structural integrity and performance characteristics over extended periods.
- Superior Fatigue Strength: The guide vanes are subjected to cyclical loading and stress during engine operation. Inconel 939’s high fatigue strength ensures that it can withstand these stresses without cracking or fracturing, thus contributing to the extended lifespan of the gas turbine.
- Excellent Weldability: This characteristic simplifies the manufacturing process, allowing for complex geometries to be efficiently fabricated and ensuring consistent material properties throughout the component.
The Manufacturing Process: Precision and Quality Assurance
The creation of high-performance guide vanes from Inconel 939 demands a meticulous manufacturing process, incorporating advanced techniques to ensure exceptional quality and precision:
- Investment Casting: This process allows for the creation of complex geometries with excellent surface finish, vital for efficient airflow management. The investment casting process utilizes ceramic molds to achieve the intricate details necessary for optimal aerodynamic performance. Subsequent machining processes then refine these castings to precise tolerances.
- CNC Machining: Computer Numerical Control (CNC) machining ensures precise shaping and tolerances, critical for the accurate control of gas flow. This advanced machining technique enables the creation of highly accurate and intricate guide vanes, ensuring that the final product precisely meets the demanding specifications of gas turbine applications. High-precision machining minimizes surface imperfections that could hinder performance or contribute to premature wear.
- Advanced Surface Treatments: Surface treatments, such as shot peening or thermal barrier coatings, are often employed to further enhance the durability and resistance to corrosion and erosion. These treatments are critical to extending the operational lifespan of the guide vanes in the harsh environment of the gas turbine engine.
- Non-Destructive Testing (NDT): Rigorous NDT methods, including ultrasonic testing and dye penetrant inspection, ensure the structural integrity and freedom from defects of each guide vane before it is deployed. This commitment to quality control ensures the reliability and longevity of our products.
- Quality Control: Throughout the entire manufacturing process, we maintain stringent quality control measures to ensure that each guide vane meets the highest standards of precision and performance. These measures, encompassing everything from raw material inspection to final product testing, guarantee the exceptional quality and reliability of our guide vanes.


BLAZE: Your Partner for High-Performance Guide Vanes
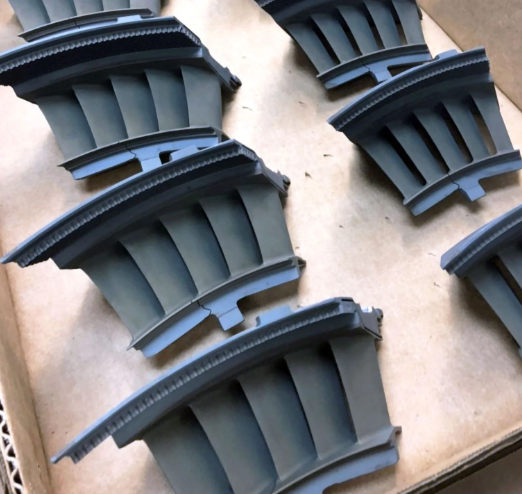
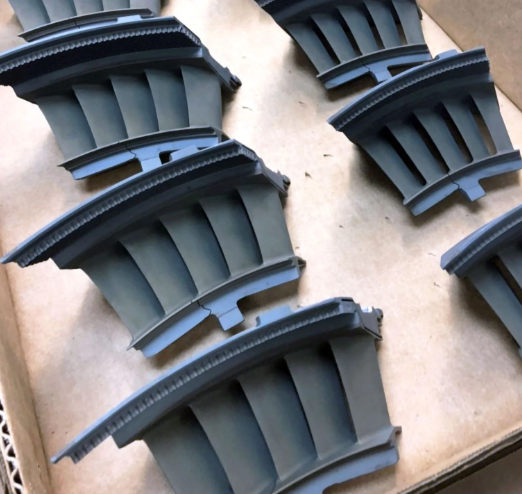
At BLAZE, we are dedicated to providing superior guide vane solutions that maximize the performance, reliability, and longevity of gas turbine engines. Our commitment to utilizing premium materials like Inconel 939, combined with our advanced manufacturing processes and stringent quality control measures, ensures that our customers receive products that exceed their expectations. Contact us today to discuss your specific guide vane requirements and discover how we can help you optimize your gas turbine’s performance.
Contact us:
Partner with BLAZE to elevate your gas turbine performance. Our commitment to utilizing premium Inconel 939, coupled with our advanced manufacturing processes and rigorous quality control, ensures superior guide vanes that maximize efficiency, extend lifespan, and minimize downtime. Contact us today to discuss your specific needs and discover how we can help optimize your gas turbine operation.