The aviation gas turbine engine (hereinafter referred to as the engine) is a rotating mechanical product that integrates high temperature, high speed, high pressure and complex vibration environment. How can a high-speed rotating machine working in such a harsh environment have high reliability, safety, economy, comfort (low noise and low vibration) and long life, while also having excellent structural efficiency? The answer must rely on the strength design technology of the aviation gas turbine engine.

- Engine strength design technology includes: theories and methods for quantitatively describing the structural deformation, dynamic response, fatigue, creep, oxidation corrosion, plastic deformation, fracture and impact damage behaviors of the engine and its components under the use environment and load; design theories, methods and technologies for giving the engine structure the expected safety, durability and reliability during the entire life cycle of engine development and use, taking into account the engine use environment, load, structure and material process characteristics and their dispersion; providing theories, methods and technologies for improving the engine strength required for engineering design analysis efficiency.
- Engine strength design technology covers a wide range of areas, from the whole machine load, whole machine rigidity and whole machine vibration, to the static strength, deformation and rigidity, stability, vibration and life of parts, all of which are areas that engine strength design technology must participate in.
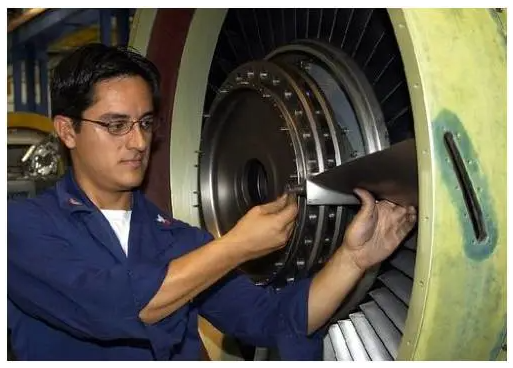
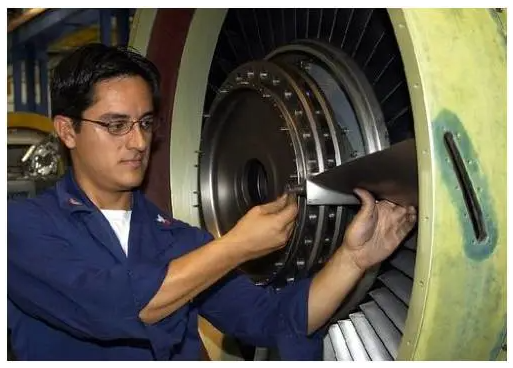
Therefore, as a branch of mechanical strength design, engine strength design is a time-consuming and costly system engineering, and its design accuracy requires a large amount of continuously improved design practice and product application as a basis. Therefore, the maturity and development of engine strength design technology is more difficult and long compared with the development of aerodynamics and thermal dynamics.
In addition, the application of new materials such as ceramic composites, fiber-reinforced composites, and new processes such as additive manufacturing technology, laser surface strengthening and laser repair technology in aviation gas turbine engines has brought new technical challenges to strength engineers.
The influence and restriction of materials and processes on strength design
The core of strength design technology is to objectively understand and accurately predict the response of a structure under the use environment and load. The materials and process used to manufacture a specific structure directly determine the mechanical properties of the specific structure under a specific environment and a given load, and thus determine the specific structure’s response to the environment and load, from deformation, vibration, damage to mechanical performance degradation. When a component is manufactured and assembled on the engine, its mechanical properties continue to decline as the use time increases. Therefore, strength design is inseparable from the mastery of various material properties.
The influence and restriction of design material performance data on strength design
The performance data of design materials is the basis of engine structure analysis and strength design. Without the performance data of design materials, structure analysis and strength design will become castles in the air. Therefore, the systematicness, integrity and reliability of the performance data of design materials reflect to a certain extent how solid the foundation of engine structure analysis and strength design is, how deep the practice is, how wide the practice is, and to a certain extent, it reflects the engineering practice level of structure analysis and strength design.
Engine structural analysis and strength design require design material performance data that represents the mechanical properties of specific parts of real components and has a certain degree of confidence and reliability. It needs to include basic physical properties and short-term mechanical performance data, including not only low-cycle fatigue performance of different material process states, different parts (typically such as wheel rim, spoke plate, wheel center), different directions (typically such as single crystal, directional crystallization), typical temperature range, typical stress/strain/strain ratio, but also high-cycle fatigue performance of different temperatures, different process states (including surface state), different parts, and different stress concentration parts. For high-temperature alloys, performance data such as endurance performance, creep performance, and thermal fatigue performance at different temperatures, different stresses, and different durations are also required.
As a mechanical product, the structural strength design of aviation gas turbine engines is a process of gradual accumulation and improvement, which is also reflected in the gradual accumulation and improvement of design performance data. The measurement cost of these design performance data is high and the cycle is long. When applying new materials and new processes, the testing of design performance data may be carried out simultaneously with the development process and application research and verification of materials and processes, and the lack of design material performance data is more prominent. Design material performance data should not only be comprehensive, complete and reliable, but also effectively managed and convenient for users to use, as well as the accumulation of new data and organic integration into existing measurement data (library).
To carry out civil aviation power plant design, whether the design material performance data meets the requirements is the first hurdle that must be overcome to obtain an airworthiness certificate.
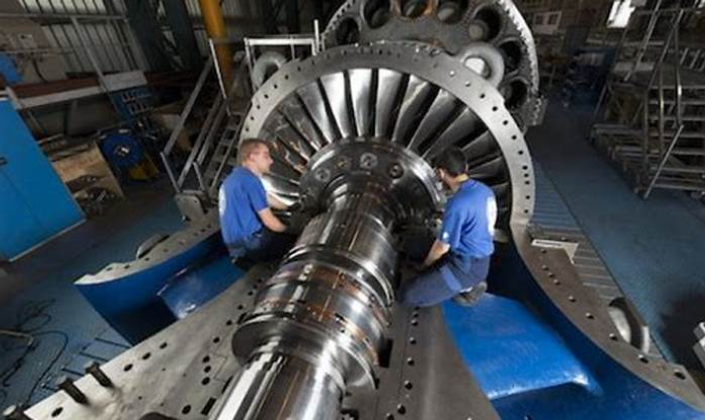
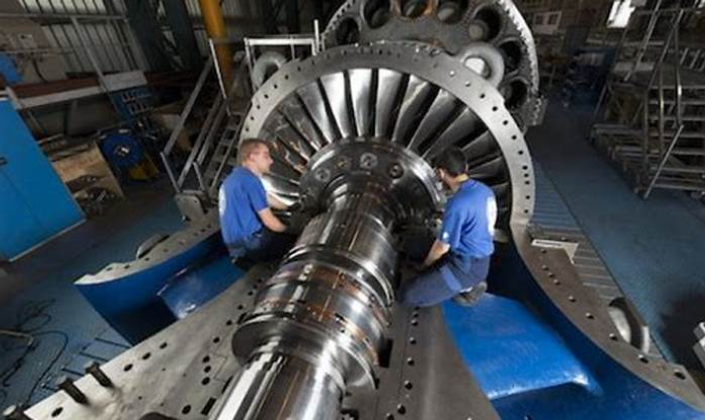
Contact us
Thank you for your interest in our company! As a professional gas turbine parts manufacturing company, we will continue to be committed to technological innovation and service improvement, to provide more high-quality solutions for customers around the world.If you have any questions, suggestions or cooperation intentions, we are more than happy to help you. Please contact us in the following ways:
WhatsAPP:+86 135 4409 5201
E-mail:peter@turbineblade.net