As one of the most critical components, the gas turbine nozzle ring must have the characteristics of high temperature and pressure resistance and strong corrosion resistance, and the choice of material is directly related to the service life and mechanical properties of the parts and even the whole engine. Relatively speaking, nickel-based alloys are our best choice, especially inconel625, with its excellent strength and super corrosion resistance and oxidation resistance, becoming our ideal material. This article will describe our company’s precision production process for nozzle rings and the product advantages of the final product.

1. Precision manufacturing process of Inconel 625 nozzle ring
The manufacture of the Inconel 625 nozzle ring is a complex process that typically involves the following steps:


1) Material preparation
- Selection of material: The appropriate Inconel 625 raw material is selected according to the design requirements, usually in the form of bar, sheet or tube.
- Material inspection: to ensure that the material meets the specifications, chemical composition analysis and physical properties test.
2) Preliminary molding
- Heat treatment: Solution treatment of the billet to improve its mechanical properties, usually involving heating to a specific temperature followed by rapid cooling, such as water quenching.
- Cutting: According to the size requirements of the final product, using sawing or laser cutting to cut the blank from the raw material in the desired shape and size.
3) Molding processing
- Forging: For some applications requiring high strength and toughness, further forming may be required by hot or cold forging.
- Machining: Using CNC machine tools and other precision equipment to turn, mill, drill and other operations to achieve the exact size and surface finish requirements.
- Welding: If the design requires it, it may involve welding multiple parts together to form a complete nozzle ring structure. Inconel 625 has good weldability, but attention should be paid to controlling welding parameters to avoid cracks.
4) Precision machining and surface treatment
- Surface treatment: In order to improve the corrosion resistance and surface quality, polishing, sandblasting, electroplating and other methods can be used for surface treatment.
- Finishing: After the initial molding is completed, fine machining is required to ensure that all dimensions are within tolerances.
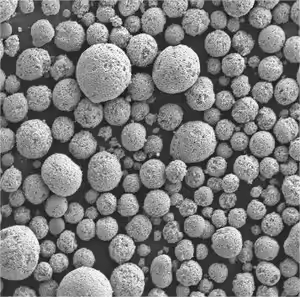

5) Quality inspection
- Non-destructive testing: Use X-ray, ultrasonic and other technology to check internal defects.
- Dimensional inspection: dimensional accuracy inspection of finished products is carried out by using coordinate measuring machine (CMM) and other tools.
- Performance test: According to the specific application requirements, the pressure resistance, temperature resistance, fatigue life and other aspects of the test.
6) Packaging and delivery
- Delivery: Delivery of the finished product to the designated location.
- Cleaning: Remove surface oil and other residue.
- Packing: properly pack according to customer’s requirements to prevent damage during transportation.
2. Technological advantages
- High precision: Our technical department adopts advanced CNC machining technology and precision measurement technology in research and comparison to ensure that the dimensional accuracy and geometry of the products are perfectly in line with the needs of customers.
- High efficiency: We use mechanized automation and precision manufacturing processes and processes to ensure our production efficiency and accuracy, and improve the production efficiency of products.
- High reliability: Our engineers strictly control the quality and carry out precise non-destructive testing on the finished product to ensure the reliability and long service life of the product.
- Repeatability: Our factory has a series of complete manufacturing processes and supervision systems to ensure the production consistency of workers and equipment, to ensure the consistency and repeatability of product performance and quality.


3. Product advantages
- Excellent high temperature strength: inconel 625 This material not only ensures the strength of the product under high temperature and high pressure environment, but also ensures the product’s waxy resistance.
- Strong corrosion resistance: The material we selected for this model has excellent characteristics that can resist high temperature corrosive gases, which not only ensures the coordination of components and engines, but also ensures the performance of components and engines.
- Long service life: Our forging and machining processes not only ensure accuracy, but also extend the service life of components and reduce maintenance costs.
- Lightweight design: Through optimized design and precision molding process, the nozzle ring can be lightweight, reduce the weight of the engine, and improve fuel efficiency.
4. Conclusion
Our factory uses inconel 625 materials combined with advanced manufacturing equipment and precision manufacturing process to produce high-precision and high-performance products that meet the requirements of customers. Its excellent mechanical properties and longer service life provide a strong guarantee for improving the coordination and efficiency of various components of the gas turbine. Our factories are dedicated to developing more accurate processes, optimizing product performance, and improving usage efficiency to meet the needs of customers in different usage scenarios.
Thank you for your interest in our company! As a professional gas turbine parts manufacturing company, we will continue to be committed to technological innovation and service improvement, to provide more high-quality solutions for customers around the world.If you have any questions, suggestions or cooperation intentions, we are more than happy to help you. Please contact us in the following ways:
- WhatsAPP:+86 135 4409 5201
- E-mail:peter@turbineblade.net