Thermal barrier coating
Research background of thermal barrier coatings
- Since the successful development of the first gas turbine in 1920, the gas turbine has always played a pivotal role in the field of power generation and drive. In addition, with the development of industrial technology, the technical level of heavy-duty gas turbines is constantly improving, and how to improve the efficiency of heavy-duty gas turbines becomes more and more urgent. Turbine blade is one of the important components of heavy-duty gas turbine combustion system. Increasing turbine inlet temperature can effectively improve the efficiency of heavy-duty gas turbine. Therefore, the relevant researchers can work towards increasing the temperature of the turbine inlet. In order to meet the increasing demand for operating temperature of future efficient gas turbines, thermal barrier coatings are usually sprayed on the surface of hot-end components.
- In 1953, the concept of thermal barrier coating was first proposed by NASA-Lewis Research Institute in the United States [13], that is, ceramic coating is sprayed on the surface of parts working in high temperature environment through thermal spraying technology, so as to provide heat insulation and protection, reduce the temperature of blade surface, reduce the fuel consumption of the engine, and extend the service life of the blade. Thermal barrier coating has been widely used in the hot end components of industrial gas turbines and aeroengines (turbine blades and combustion chambers, etc.) due to its excellent characteristics such as low preparation cost and good thermal insulation protection, and is internationally recognized as a cutting-edge technology for heavy gas turbine manufacturing.
System structure of thermal barrier coating
With the progress and development of science and technology, the inlet temperature of gas turbines is getting higher and higher. In order to achieve better thermal insulation effect of thermal barrier coating, most studies around the world focus on designing the structure of thermal barrier coating, which is sufficient to show the importance of the structure of thermal barrier coating [14]. According to the different structure of coating, it can be divided into double layer, multi-layer and gradient structure [15].
Among them, the double-layer thermal barrier coating composed of ceramic layer and bond layer, as the simplest and more mature thermal barrier coating in all coating structures, has been widely used in thermal barrier coating technology. Among them, the most widely used double-layer structural thermal barrier coating takes 6 wt.% ~ 8 wt.% yttrium stabilized zirconia (6-8YSZ) as the external ceramic layer material, and MCrAlY (M=Ni, Co, Ni+Co, etc.) alloy as the metal bonding layer material [16]. However, due to the mismatch between the thermal expansion coefficient of the ceramic layer and the metal bonding layer, it is easy to produce stress in the coating and make the coating fall off early.
In order to improve the performance of the thermal barrier coating, the researchers prepared a multi-layer structural thermal barrier coating with a relatively complex structure (composite coating), that is, several layers of insulation and barrier layers are added on the basis of the double-layer structural thermal barrier coating, generally five layers. Among them, the most studied blocking layers mainly include Al2O3, NiAl, etc. [17]. FENG et al. [18] used APS to prepare YSZ thermal barrier coating and LZ/YSZ thermal barrier coating (La2Zr2O7 / ZrO2-Y2O3 double ceramic layer thermal barrier coating), and used laser remelting technology to remelt the coating surface, and then carried out high temperature oxidation test at 1 100℃. The results show that compared with YSZ thermal barrier coating, LZ/YSZ double ceramic thermal barrier coating has better oxidation resistance. Although the performance of multi-layer thermal barrier coating is better than that of double-layer thermal barrier coating, its structure and preparation process are more complex, and its thermal shock resistance is poor, so it is limited in practical application. Therefore, the gradient structure thermal barrier coating comes into being.
The gradient structure thermal barrier coating is characterized by the continuous gradient change of composition and structure along the direction of coating thickness, which results in an indistinct interlayer interface. Compared with double-layer and multi-layer structures, the gradient structure thermal barrier coating not only has outstanding thermal shock resistance, but also shows continuous gradient change in performance, so it has thermal stress relief characteristics and can be applied in harsh high temperature environment. The main thermal spraying technologies of functionally graded thermal barrier coatings were reviewed by Mr. Although there are various preparation methods, the gradient structure thermal barrier coating is bad in practice because of its complex preparation process, difficult to control structural components and high cost.
In summary, the double-layer thermal barrier coating is widely used and the process is mature, and it is still the preferred structural form of thermal barrier coating. The ceramic layer and the bonding layer [20] are deposited on the alloy matrix by thermal spraying technology. Under the condition of high temperature oxidation, a thin layer of heat-grown oxide is formed on the surface of the bonding layer after oxidation, as shown in Figure 1. Among them, the alloy matrix, as a component protected by thermal barrier coating, can play a role in bearing external mechanical loads, and its material is mainly nickel based superalloy with high temperature resistance and oxidation resistance. The role of the bonding layer is to enhance the bonding force between the ceramic layer and the alloy matrix, the thickness is generally 50 ~ 150µm, and the material is usually selected MCrAlY (M=Ni/Co/Ni+Co), which has a small difference in the thermal expansion coefficient of the alloy matrix. Thermal growth oxide (TGO) is mainly a kind of α-Al2O3 thin film formed between the ceramic layer and the bond layer under high temperature oxidation environment, with a thickness of 1 ~ 10 µm, which has a great influence on the coating. The ceramic layer has the functions of heat insulation, corrosion resistance and impact resistance [21], the thickness is usually 100 ~ 400 μm, and the material is mainly 6-8YSZ with low thermal conductivity and relatively high coefficient of thermal expansion [22].
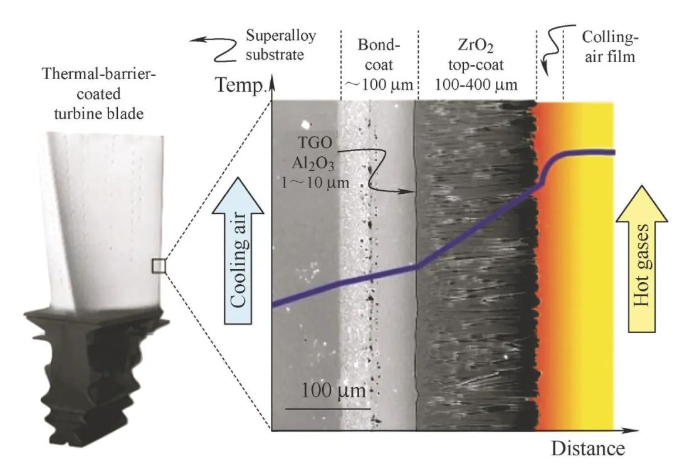
Materials of thermal barrier coating
The inlet temperature of the turbine blade is closely related to its working efficiency. Only by increasing the inlet temperature of the turbine blade can the working efficiency be improved. However, with the development of science and technology and industry, the working temperature of the hot end parts of heavy-duty gas turbines is still increasing, and the limit temperature of the nickel-based alloy turbine blade is 1150℃, which can no longer work at higher temperatures. Therefore, it is particularly urgent to find and develop thermal barrier coating materials with excellent properties. Among them, because the service conditions of thermal barrier coating are very bad, the selection conditions of thermal barrier coating materials are more stringent in the actual process. Ceramic layer materials are usually required to have low thermal conductivity and high melting point, and are not easy to undergo phase transformation in the range from room temperature to service temperature, and also need high thermal expansion coefficient, outstanding thermal shock resistance, sintering resistance and corrosion resistance [24]. The bonding layer material is required to have corrosion resistance, oxidation resistance, good bonding strength and other properties [25-26].
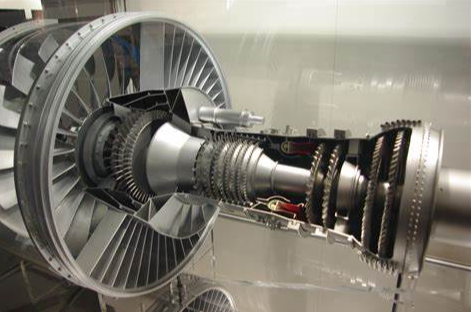
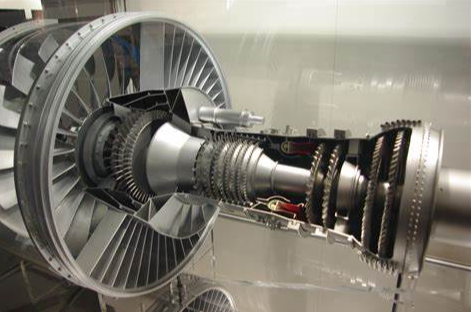
Ceramic layer material
The harsh service conditions of thermal barrier coating limit the selection of its materials. Currently, the thermal barrier coating materials suitable for practical application are very limited, mainly YSZ materials and rare earth oxide doped YSZ materials.
(1) yttrium oxide stabiliz ed zirconia
At present, among ceramic materials, ZrO2 stands out for its high melting point, low thermal conductivity, high coefficient of thermal expansion and good fracture toughness. However, pure ZrO2 has three crystal forms: monoclinic (m) phase, cubic (c) phase and tetragonal (t) phase, and pure ZrO2 is easy to undergo phase transformation, resulting in volume change, which has adverse effects on the coating life. Therefore, ZrO2 is often doped with stabilizers such as Y2O3, CaO, MgO and Sc2O3 to improve its phase stability. Among them, 8YSZ has the best performance, It has sufficient hardness (~ 14 GPa), low density (~ 6.4 Mg·m-3), low thermal conductivity (~ 2.3 W·m-1 ·K-1 at 1 000℃), high melting point (~ 2 700℃), high coefficient of thermal expansion (1.1×10-5 K-1) and other excellent properties. Therefore, as a ceramic layer material, it is widely used in thermal barrier coatings.
(2) Rare earth oxides doped YSZ
When YSZ works in an environment above 1 200 ° C for a long time, phase transition and sintering usually occur. On the one hand, the non-equilibrium tetragonal phase t ‘is transformed into a mixture of cubic phase c and tetragonal phase t, and during cooling, t’ is transformed into monoclinic phase m, and the phase transition occurs continuously with the change of volume, thus rapidly shedding the coating [27]. On the other hand, sintering reduces the porosity in the coating, reduces the thermal insulation performance and strain tolerance of the coating, and increases the hardness and elastic modulus, which greatly affects the performance and life of the coating. Therefore, YSZ cannot be applied to the next generation of heavy-duty gas turbine engines.
In general, the performance of YSZ can be improved by changing or increasing the type of stabilizer of zirconia, such as the method of doping YSZ with rare earth oxides [28-30]. It has been found that the larger the radius difference between Zr ions and doped ions, the higher the concentration of defects, which can improve phonon scattering and reduce thermal conductivity [31]. CHEN et al. [32] used APS to prepare a thermal barrier coating ceramic layer (LGYYSZ) with La2O3, Yb2O3 and Gd2O3 co-doped YSZ, and obtained the thermal expansion coefficient and thermal conductivity of the thermal barrier coating through measurement and calculation, and conducted a thermal cycle test at 1 400℃. The results show that compared with YSZ coating, LGYYSZ coating has lower thermal conductivity, longer thermal cycle life and good phase stability at 1 500℃. Li Jia et al. [33] prepared Gd2O3 and Yb2O3 co-doped YSZ powder by chemical co-precipitation method and prepared Gd2O3 and Yb2O3 co-doped YSZ coating by APS, and studied the influence of different oxide doping amounts on the stability of coating phase. The results show that the phase stability of Gd2O3 and Yb2O3 co-doped YSZ coating is better than that of traditional 8YSZ coating. The phase m phase is less after heat treatment at high temperature when the doping amount is low, and the stable cubic phase is produced when the doping amount is high.
Compared with the traditional YSZ, the new modified YSZ ceramic material has lower thermal conductivity, which makes the thermal barrier coating have better thermal insulation performance, and provides an important basis for the research of high performance thermal barrier coating. However, the comprehensive performance of traditional YSZ is good, and it is widely used, and can not be replaced by any modified YSZ.
Bonding layer material
The bonding layer is very important in the thermal barrier coating. In addition, the ceramic layer can be closely bonded to the alloy matrix, and the internal stress caused by the mismatch of thermal expansion coefficient in the coating can be reduced. In addition, the thermal corrosion resistance and oxidation resistance of the entire coating system can be improved by forming a dense oxide film at high temperature, thus prolonging the life of the thermal barrier coating. At present, the material used for the bonding layer is usually MCrAlY alloy (M is Ni, Co or Ni+Co, depending on the use). Among them, NiCoCrAlY is widely used in heavy-duty gas turbines because of its good comprehensive properties such as oxidation resistance and corrosion resistance. In MCrAlY system, Ni and Co are used as matrix elements. Due to the good oxidation resistance of Ni and the good fatigue resistance of Co, the comprehensive properties of Ni+Co (such as oxidation resistance and corrosion resistance) are good. While Cr is used to improve the corrosion resistance of the coating, Al can enhance the oxidation resistance of the coating, and Y can improve the corrosion resistance and thermal shock resistance of the coating.
The performance of the MCrAlY system is excellent, but it can only be used for work below 1 100℃. In order to increase the service temperature, the relevant manufacturers and researchers have carried out a lot of research on the modification of MCrAlY coating. For example, doping other alloying elements such as W, Ta, Hf and Zr [34] to improve the performance of the bond layer. YU et al. [35] sprayed a thermal barrier coating composed of Pt modified NiCoCrAlY bond layer and nanostructured 4 wt.% yttrium-stabilized zirconia (4YSZ) ceramic layer on the second generation nickel-based superalloy. The thermal cycling behavior of NiCoCrAlY-4YSZ thermal barrier coating in air and the effect of Pt on the formation and oxidation resistance of TGO were investigated at 1 100℃. The results show that compared with Nicocraly-4YSZ, the modification of NiCoCrAlY by Pt is beneficial to the formation of α-Al2O3 and the reduction of TGO growth rate, thus extending the life of the thermal barrier coating. GHADAMI et al. [36] prepared NiCoCrAlY nanocomposite coating by supersonic flame spraying with nanoCEO2. The NiCoCrAlY nanocomposite coatings with 0.5, 1 and 2 wt.% nanoCEO2 were compared with the conventional NiCoCrAlY coatings. The results show that NICocRALy-1 wt.% nano-CEO2 composite coating has better oxidation resistance, higher hardness and lower porosity than other conventional NiCoCrAlY coatings and NiCoCrAlY nano-composite coatings.
At present, in addition to the MCrAlY system can be applied to the bond layer, NiAl is also a key bond layer material. NiAl is mainly composed of β-NiAl, which forms a continuous dense oxide film on the coating surface at temperatures higher than 1 200℃, and is recognized as the most potential candidate material for a new generation of metal bonding layers. Compared with MCrAlY and traditional β-NiAl coatings, PT-modified β-NiAl coatings have better oxidation resistance and corrosion resistance. However, the oxide film formed at high temperatures has poor adhesion, which will greatly shorten the life of the coating. Therefore, in order to improve the performance of NiAl, researchers carried out doping modification studies on NiAl. Yang Yingfei et al. [37] prepared NiCrAlY coating, NiAl coating, PT-modified NiAl coating and Pt+Hf co-doped NiAl coating, and compared the oxidation resistance of these four coatings at 1 100℃. The final results show that the best oxidation resistance is the Pt+Hf co-doped NiAl coating. Qiu Lin [38] prepared NiAl block alloy with different Al content and β-NiAl block alloy with different Hf/Zr content by vacuum arc melting, and studied the effects of Al, Hf and Zr on the oxidation resistance of NiAl alloy. The results showed that the oxidation resistance of NiAl alloy increased with the increase of Al content, and the addition of Hf/Zr in β-NiAl alloy was beneficial to improve the oxidation resistance, and the optimal doping amounts were 0.1 at.% and 0.3 at.%, respectively. LI et Al. [39] prepared a new rare-earth modified β- (Ni, Pt) Al coating on Mo-rich Ni2Al-based superalloy by electrodeposition and low activity aluminizing technology, and compared the rare-earth modified β- (Ni, Pt) Al coating with the traditional β- (Ni, Pt) Al coating. Isothermal oxidation behavior of Pt) Al coating at 1 100℃. The results show that rare earth elements can improve the oxidation resistance of the coating.
In summary, MCrAlY and NiAl coatings have their own advantages and disadvantages, so researchers should continue to persist in modification research on the basis of these two coating materials, looking for the development of new metal bonding layer materials, so that the service temperature of the thermal barrier coating for heavy gas turbines can be higher.