Key properties of gas turbine thermal barrier coating
Because the work of ground heavy gas turbines is generally in a complex environment, and the maintenance cycle is long, it can be as high as 50,000 hours. Therefore, in order to improve gas turbine thermal barrier coating technology and extend the service life of thermal barrier coating, in recent years, researchers have conducted a lot of research on the key properties of thermal barrier coating, such as heat insulation, oxidation resistance, thermal shock resistance and CMAS corrosion resistance. Among them, the research and progress of thermal barrier coatings on heat insulation, oxidation resistance and thermal shock resistance are relatively sufficient, but the resistance to CMAS corrosion is relatively scarce. At the same time, CMAS corrosion has become a major failure mode of thermal barrier coatings, hindering the development of the next generation of high-performance gas turbines. Therefore, this section first briefly introduces the thermal insulation, oxidation resistance and thermal shock resistance of thermal barrier coatings, and then focuses on the research progress of CMAS corrosion mechanism and protection technology of thermal barrier coatings in Section 4.
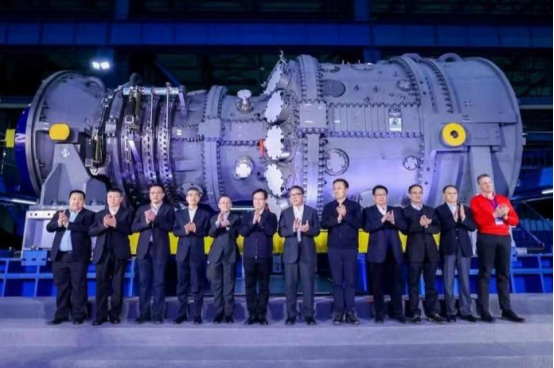
Heat insulation property
- With the development of industry, high performance gas turbines have put forward higher requirements for turbine inlet temperature. Therefore, it is very important to improve the thermal insulation of the thermal barrier coating. The thermal insulation of the thermal barrier coating is related to the material, structure and preparation process of the coating. In addition, the service environment of the thermal barrier coating will also affect its thermal insulation performance.
- Thermal conductivity is generally used as the evaluation index for the thermal insulation performance of thermal barrier coatings. Liu Yankuan et al. [48] prepared 2 mol.% Eu3+ doped YSZ coating with APS, and compared with YSZ coating, the results showed that the thermal conductivity of 2 mol.% Eu3+ doped YSZ coating was lower, that is, the thermal insulation of 2 mol.% Eu3+ doped YSZ coating was better. It is found that the spatial and geometric characteristics of the pores in the coating have a great influence on the thermal conductivity [49]. SUN et al. [50] conducted a comparative study on the thermal conductivity and elastic modulus of thermal barrier coatings with different pore structures. The results show that the thermal conductivity and elastic modulus of the thermal barrier coating decrease with the decrease of the pore size, and the higher the porosity, the lower the thermal conductivity. A large number of studies have shown that compared with EB-PVD coating, APS coating has better thermal insulation, because APS coating has higher porosity and lower thermal conductivity [51]. RATZER-SCHEIBE et al. [52] studied the effect of the coating thickness of EB-PVD PYSZ on the thermal conductivity, and the results showed that the coating thickness of EB-PVD PYSZ greatly affected its thermal conductivity, that is, the coating thickness was also one of the important factors affecting the thermal insulation performance of the thermal barrier coating. The research results of Gong Kaisheng et al. [53] also show that in the thickness range of the actual coating application, the thermal insulation performance of the coating is proportional to its thickness and environmental temperature difference. Although the thermal insulation performance of the thermal barrier coating will be enhanced with the increase of thickness, when the coating thickness continues to increase to a certain value, it is easy to cause stress concentration in the coating, resulting in early failure. Therefore, in order to enhance the thermal insulation performance of the coating and extend its service life, the coating thickness should be reasonably regulated.
Oxidation resistance
Under the condition of high temperature oxidation, a layer of TGO is easily formed in the thermal barrier coating. The influence of TGO on the thermal barrier coating [54] has two sides: On the one hand, the formed TGO can prevent oxygen from continuing to diffuse inward and reduce the external influence on the oxidation of the alloy matrix. On the other hand, with the continuous thickening of TGO, due to its large elastic modulus and the large difference between its thermal expansion coefficient and the adhesive layer, it is also relatively easy to produce large stress during the cooling process, which will make the coating fall off quickly. Therefore, in order to extend the life of the thermal barrier coating, it is urgent to improve the oxidation resistance of the coating.
XIE et al. [55] studied the formation and growth behavior of TGO, which was mainly divided into two stages: first, a dense α-Al2O3 film was formed on the bonding layer, and then a porous mixed oxide was formed between the ceramic layer and α-Al2O3. The results show that the main substance causing cracks in the thermal barrier coating is the porous mixed oxide in TGO, not α-Al2O3. LIU et al. [56] proposed an improved method to simulate the growth rate of TGO through numerical analysis of stress evolution in two stages, so as to accurately predict the life of thermal barrier coatings. Therefore, the thickness of TGO can be effectively controlled by controlling the growth rate of porous harmful mixed oxides, so as to avoid premature failure of thermal barrier coatings. The results show that the growth of TGO can be delayed by using dual-ceramic thermal barrier coating, deposition of protective layer on the surface of the coating and improving the density of the coating surface, and the oxidation resistance of the coating can be improved to a certain extent. AN et al. [57] used APS technology to prepare two kinds of thermal barrier coatings: The formation and growth behavior of TGO were studied by isothermal oxidation tests at 1 100℃. The first is YAG/YSZ double ceramic barrier coating (DCL TBC) and the second is YSZ single ceramic barrier coating (SCL TBC). The research results show that the formation and growth process of TGO follow the laws of thermodynamics, as shown in Figure 5: According to formula (1) ~ (8), Al2O3 is formed at first, and then Y ion oxidation forms an extremely thin layer of Y2O3 on the surface of Al2O3 TGO, and the two react with each other to form Y3Al5O12. When Al ion is reduced to a certain value, other metal elements in the bond layer oxidized before and after forming mixed oxides (Cr2O3, CoO, NiO and spinel oxides, etc.), first forming Cr2O3, CoO, NiO, and then reacting with (Ni, Co) O and Al2O3 to form (Ni, Co) Al2O4. (Ni, Co) O reacts with Cr2O3 to form (Ni, Co) Al2O4. Compared with SCL TBC, the formation and growth rate of TGO in DCL TBC is slower, so it has better high-temperature antioxidant properties. Xu Shiming et al. [58] used magnetron sputtering to deposit a film on the surface of the 7YSZ coating. After heat treatment, α-Al2O3 layer was generated by in-situ reaction. The study showed that the α-Al2O3 layer formed on the surface of the coating could improve the oxidation resistance of the coating by preventing oxygen ion diffusion. FENG et al. [59] showed that laser remelting of APS YSZ coating surface can improve the oxidation resistance of the coating, mainly because laser remelting can improve the densification of the coating, thus delaying the growth of TGO.
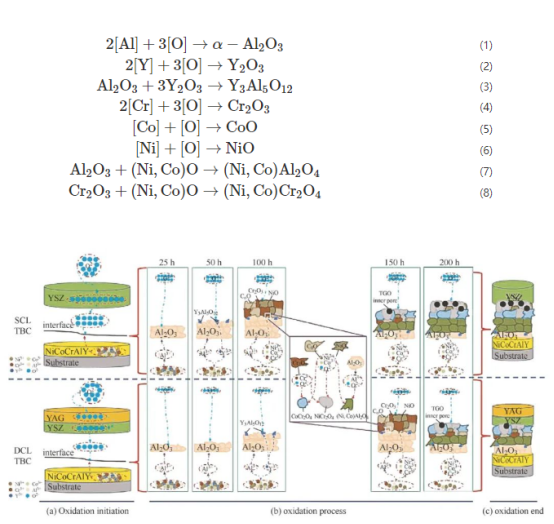
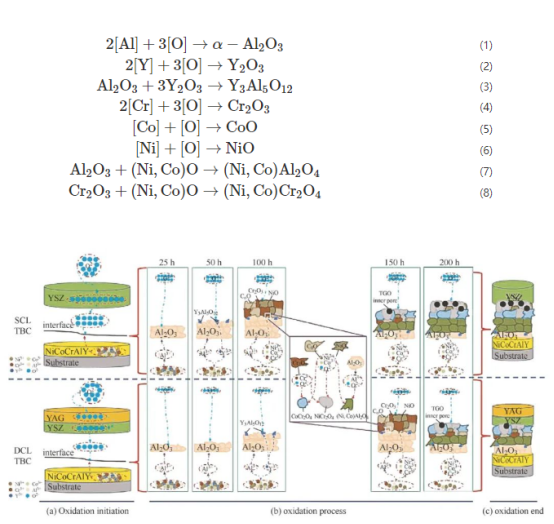
Thermal shock resistance
When the hot end components of heavy-duty gas turbines are in service in high temperature environment, they often suffer thermal shock caused by rapid temperature change. Therefore, the alloy parts can be protected by improving the thermal shock resistance of the thermal barrier coating. The thermal shock resistance of the thermal barrier coating is generally tested by thermal cycling (thermal shock) test, first held at high temperature for a period of time, and then removed for air/water cooling is a thermal cycle. The thermal shock resistance of the thermal barrier coating is evaluated by comparing the number of thermal cycles experienced by the coating when it fails. Studies have shown that the thermal shock resistance of gradient structure thermal barrier coating is better, mainly because the thickness of gradient structure thermal barrier coating is small, which can delay the thermal stress in the coating [60]. ZHANG et al. [61] carried out thermal cycle tests at 1 000℃ on the three forms of spot, streak and grid thermal barrier coatings obtained by laser remelting of NiCrAlY / 7YSZ thermal barrier coating, and studied the thermal shock resistance of sprayed specimens and three samples with different shapes after laser treatment. The results show that the dot sample has the best thermal shock resistance and the thermal cycle life is twice that of spray sample. However, the thermal shock resistance of the striped and grid samples is worse than that of the spray samples, as shown in Figure 6. In addition, a large number of studies have shown that some new coating materials have good thermal shock resistance, such as SrAl12O19 [62] proposed by ZHOU et al., LaMgAl11O19 [63] proposed by LIU et al., and Sm2 (Zr0.7Ce0.3) 2O7 [64] proposed by HUO et al. Therefore, in order to improve the thermal shock resistance of the thermal barrier coating, in addition to the structural design and optimization of the coating, it is possible to find and develop new materials with good thermal shock resistance.
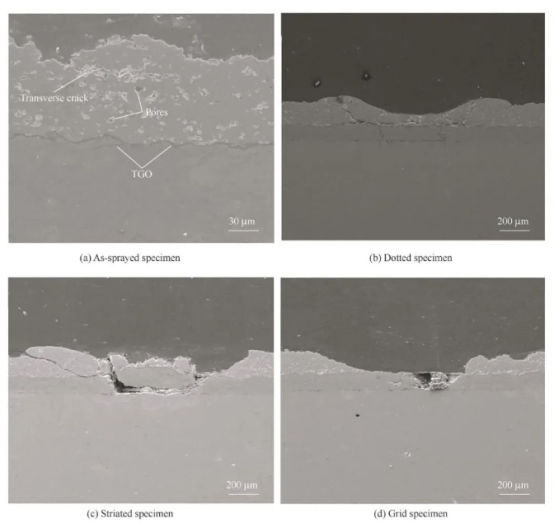
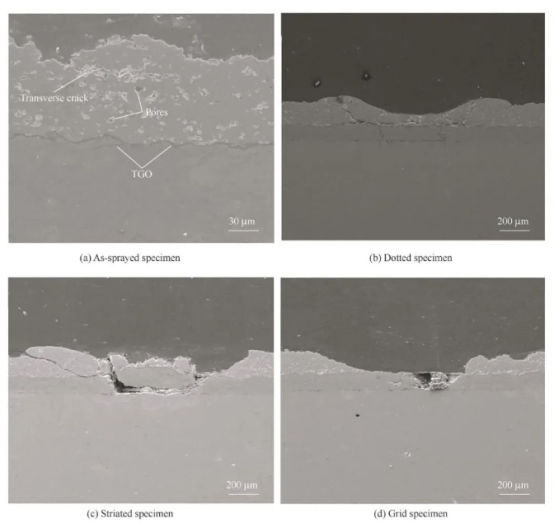