Replacing fossil fuels with renewable energy sources such as hydrogen can significantly reduce carbon emissions. In the field of gas turbines, domestic and foreign manufacturers have focused on laying out hydrogen gas turbines. At present, there are significant technical challenges for pure hydrogen gas turbines [1], and hydrogen blending gas turbines are the key development direction at present and for a period of time.
Domestic and foreign scholars have conducted research on the basic combustion characteristics, turbulent combustion characteristics, and gas turbine combustion characteristics of mixed fuels (known as “hydrogen rich gas”) mixed with hydrogen in methane. In terms of basic combustion characteristics, Zhang et al. [2] studied the ignition delay characteristics of hydrogen rich gas and revealed that the ignition enhancement of mixed fuels with different hydrogen blending ratios is dominated by different mechanisms. The laminar flame propagation speed of hydrogen rich gas has also been widely studied [3-7], and it has been found that hydrogen addition can significantly improve the flame propagation speed. When the hydrogen addition ratio exceeds 70%, its combustion characteristics are basically similar to pure hydrogen gas. In terms of turbulent combustion characteristics, domestic and foreign scholars have focused on the issue of backfire in hydrogen rich gas combustion [8-11]. Research has found that there are two tempering modes in swirling flames: boundary layer tempering and central recirculation zone tempering. Parameters such as fuel preheating temperature, pressure, and hydrogen doping ratio have an impact on the boundary layer tempering limit. In addition, hydrogen doping also has a significant impact on the thermoacoustic oscillation characteristics of methane flames [12-17]. Research has found that hydrogen doping affects the thermoacoustic response of unstable combustion systems by altering the macroscopic shape and heat release characteristics of the flame.
In terms of combustion characteristics of gas turbines, the impact of hydrogen doping on combustion stability and pollution emission characteristics is the main focus of attention. Dukata et al. [18] and Kashir et al. [19] studied blunt body swirl stabilized burners, while Pashchenko et al. [20] compared the NOx emission characteristics of hydrogen rich gas, methane, and carbon monoxide using tangential swirl burners. Fu et al. [21] and Cellek et al. [22] used numerical simulation methods to study the combustion performance of methane mixed with hydrogen in the combustion chamber of micro gas turbines. The above study suggests that hydrogen doping can lead to a slight increase in NOx emissions at the outlet, and optimization design is needed. At present, there is relatively little research on the characteristics of swirling flames based on hydrogen rich gas, and further research is needed to deepen the understanding of the dynamic characteristics of swirling flames.
This article is based on a gas turbine model combustion chamber and conducts experimental research on the swirl premixed flame of hydrogen rich gas with different hydrogen blending ratios. Laser diagnosis and flue gas analysis methods are used to obtain its basic combustion characteristics and pollution emission characteristics, and to grasp the influence of hydrogen blending on the swirl flame morphology, stable boundary, and outlet emissions.
2.research method
2.1 Experimental Methods
A single swirl model combustion chamber was used to study the premixed flame of hydrogen rich gas (methane/hydrogen) under normal temperature and pressure conditions. As shown in Figure 1 (a), the main components of the combustion chamber experimental device of the model include the intake chamber, water-cooled head, radial swirl generator, and central blunt body. The detailed structural parameters have been described in previous research works [23-25]. In addition, Figure 1 (b) shows the cyclone and central blunt body structure, which adopts a radial blade design and achieves a moderate swirl number (about 0.8), exceeding the critical swirl number (0.6) for vortex shedding and backflow generation [26], sufficient to form an effective recirculation zone for stable flames [27]. The fuel/air is pre mixed before entering the combustion chamber and is rectified by a combination of porous plates and honeycomb structures in the intake chamber to ensure uniform flow of the mixture. Three mass flow control meters (Sevenstar70D) are used to accurately control and continuously monitor the flow rates of methane, hydrogen, and air, with a control accuracy of ± 1%.
![A single swirl model combustion chamber was used to study the premixed flame of hydrogen rich gas (methane/hydrogen) under normal temperature and pressure conditions. As shown in Figure 1 (a), the main components of the combustion chamber experimental device of the model include the intake chamber, water-cooled head, radial swirl generator, and central blunt body. The detailed structural parameters have been described in previous research works [23-25]. In addition, Figure 1 (b) shows the cyclone and central blunt body structure, which adopts a radial blade design and achieves a moderate swirl number (about 0.8), exceeding the critical swirl number (0.6) for vortex shedding and backflow generation [26], sufficient to form an effective recirculation zone for stable flames [27]. The fuel/air is pre mixed before entering the combustion chamber and is rectified by a combination of porous plates and honeycomb structures in the intake chamber to ensure uniform flow of the mixture. Three mass flow control meters (Sevenstar70D) are used to accurately control and continuously monitor the flow rates of methane, hydrogen, and air, with a control accuracy of ± 1%.](https://turbineblade.net/wp-content/uploads/2025/01/图片1.png)
A quartz cylinder with a diameter of 90mm and a length of 200mm is placed on the water-cooled head wall panel to form a vortex flame confinement zone. The quartz cylinder has good optical transmission performance in the full wavelength range from ultraviolet to infrared. Particle image velocimetry (PIV) and planar laser induced fluorescence (PLIF) images are processed and displayed using a Cartesian coordinate system. The position vector and corresponding velocity vector are represented as x=(x, z) T and u=(ux, uz) T, respectively. In Figure 1 (a), the axis direction of the Cartesian coordinate system is shown, where the z-axis coincides with the axis of the cyclone and the central blunt body, and is aligned with the flow direction. The coordinate origin position is level with the outlet of the cyclone. The size of the optical testing area (ROI) shown by the dashed box in the figure is approximately 90mm × 80mm, which can effectively capture the macroscopic structure and flow field characteristics of the flame. Measure the concentrations of NO, CO, and O2 in the gas at the outlet of the combustion chamber using a smoke analyzer Testo350.
Figure 2 shows a schematic diagram of a laser diagnostic system, which uses PIV to measure the two-dimensional velocity field and OH-PLIF to measure the transient flame structure [28-29]. Two pulsed lasers overlap in space and pass through a beam expander consisting of a cylindrical lens and a spherical lens to form a diverging beam with a width of approximately 100mm. In the measured flame area, the thickness of the PIV laser beam is about 1.0mm, while the thickness of the OH-PLIF laser beam is controlled within 0.5mm.
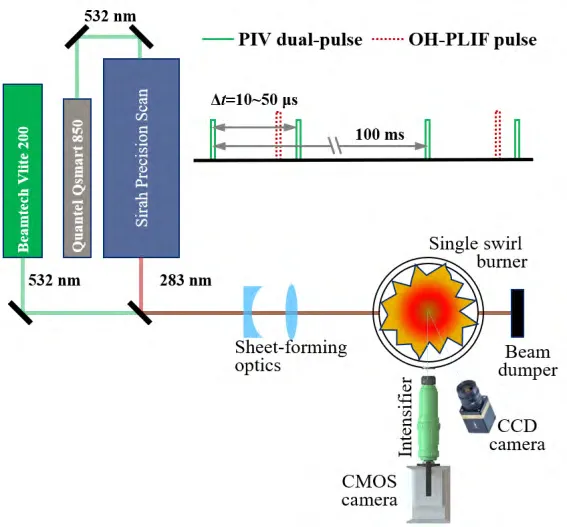
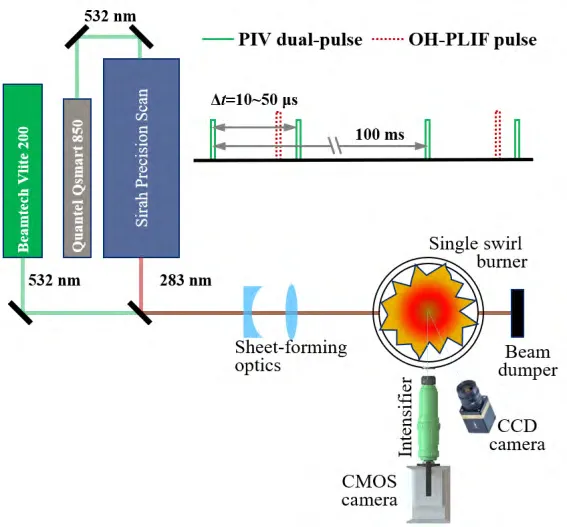
PIV measurement uses a dual cavity Q-modulated Nd: YAG laser (Beamtech Vlite-200) to generate a 10Hz dual pulse laser with a wavelength of 532nm and a pulse energy of approximately 10mJ. The time interval (Δ t) between dual pulse lasers is determined based on the speed range under different conditions, ranging from 10 to 50 μ s. Mie scattering images were recorded using a dual shutter CCD camera (ImperXBobcatB19221940 × 1460 pixels) combined with a Nikon lens and a bandpass filter plate (Edmund Optics, (532 ± 5) nm). Use titanium dioxide particles with an average diameter of about 1 μ m as tracer particles to ensure that the Stokes number St [30] is less than 1. For each measurement, record hundreds of images to achieve statistical convergence of average velocity and root mean square velocity fluctuations. Use LaVisionDaVis8.4 software for post-processing of Mie scattering images. For OH-PLIF measurement, a 10Hz frequency doubled Nd: YAG laser (QuantelQ-smart850) was used as the pump light source, and a pulsed laser with a center wavelength of about 283nm was obtained through a dye laser and a frequency doubling crystal. The average pulse energy was about 20mJ, which was used to excite Q1 (8) transition OH fluorescence in the A2 ∑+₋Τ 2 π (0-0) band [24]. Record OH fluorescence images perpendicular to the direction of the light plate using a CMOS camera (AMETEK Phantom, 2012) combined with an image intensifier (Lambert Hi CATT), ultraviolet lens, and bandpass filter plate (Edmund Optics, (310 ± 5) nm). In order to reduce the interference of flame chemiluminescence signals, the exposure time of the image intensifier is limited to within 200ns.
This study focuses on the flow field, OH component field, lean flame extinction boundary, and outlet emissions measurements of hydrogen rich gas/air premixed swirling flames with different hydrogen blending ratios α (hydrogen volume fraction in fuel, α=[H2]/([H2]+[CH4]), where [] represents molar concentration). The equivalence ratio range is 0.4~0.8, and the experimental conditions are shown in Table 1. Among them, α is 0, 30%, and 50%, respectively, denoted as 100M, 70M30H, and 50M50H.
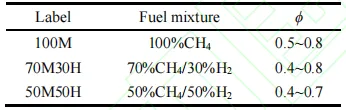
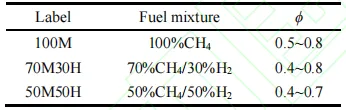
2.2 Simulation analysis methods
Chemkin Pro software [31] and GRI-Mech3.0 [32] were used to simulate and analyze the combustion reaction kinetics of hydrogen rich gas with different alpha values based on chemical reaction mechanisms. Similar analytical approaches have been used in previous studies to analyze the swirling combustion characteristics of other mixed fuels, such as ammonia/hydrogen [33] and biogas/dimethyl ether [25]. Among them, the laminar flame propagation velocity (SL) was simulated using the premixed laminar flame propagation velocity calculation module in Chemkin Pro software, taking into account the thermal diffusion equation and multi-component transport; The adiabatic flame temperature (Tad) is simulated using chemical and phase equilibrium calculation modules.