The combustion chamber, the “heart” of aircraft engines and gas turbines, have struggled to overcome issues such as long production cycles (8-12 weeks), low yield rates for complex structures (<70%), and high mold costs (30% of total expenses) for some time. As the global gas turbine market is expected to exceed $30.8 billion by 2025 (Grand View Research), traditional casting methodologies cannot meet demands for light weighting, high precision and rapid iteration.
The combustion chamber, the “heart” of aircraft engines and gas turbines, have struggled to overcome issues such as long production cycles (8-12 weeks), low yield rates for complex structures (<70%), and high mold costs (30% of total expenses) for some time. As the global gas turbine market is expected to exceed $30.8 billion by 2025 (Grand View Research), traditional casting methodologies cannot meet demands for light weighting, high precision and rapid iteration.
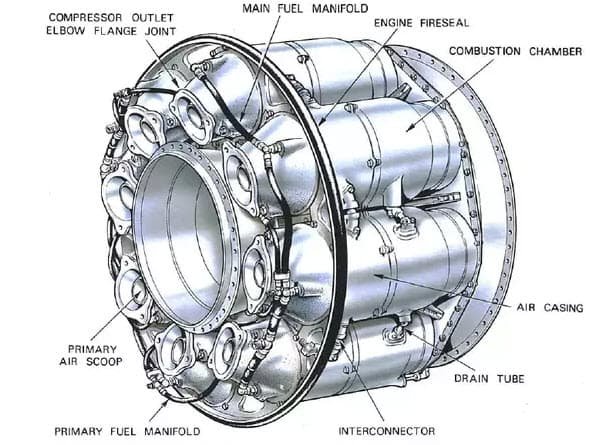
Breakthroughs in CNC and 3D Printing Technologies
- CNC Machining: The Gold Standard for Precision
5-Axis Machining: 5-axis CNC machines can handle complex geometries such as curved surfaces and cooling channels at an accuracy of ±0.01mm and surface roughness Ra≤0.8 (compared to Ra3.2 for traditional methods). A German client was able to shorten their delivery from 8 weeks to 4 weeks with this technology and saw a 25% increase in orders.
High-Temperature Alloy Optimization: For materials such as Inconel 718, optimized parameters (2,000 rpm spindle speed, 0.1mm/tooth feed rate) corresponding with ceramic-coated tools can improve tool life by 50%, driving the cost per batch to $1,200/unit.
Applications: Aerospace combustion chambers, high-precision or custom components for high power gas turbines.
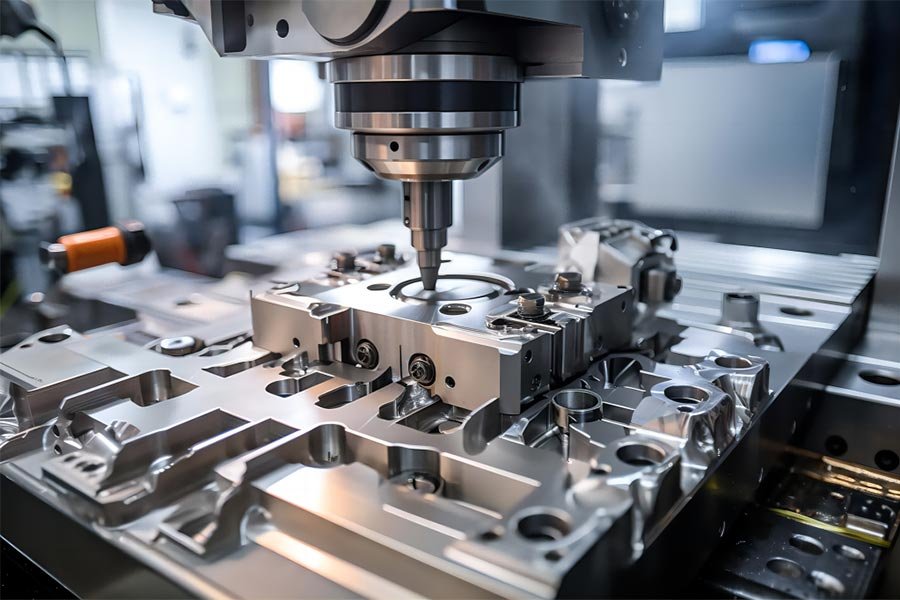
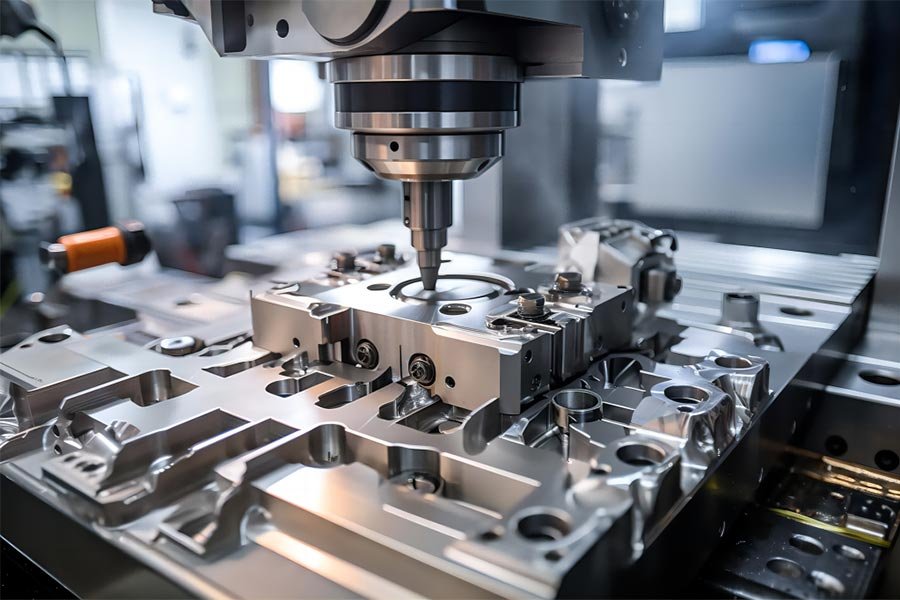
- 3D Printing: Revolutionizing Complex Structures
Metal Additive Manufacturing (SLM/DMLS): Laser powder bed fusion technology enables the creation of complex honeycomb cooling channels that would not be possible with conventional methods, and it also eliminates the risk of weld defects. A manufacturer in China used 3D printing technology to produce a gas turbine engine combustion chamber that utilized 95% material efficiency, reduced costs by 50%, and achieved the ASME certification for exports to any Middle East country.
Rapid Prototyping & Light weighting: 3D printing decreases design-to-prototype duration to 2 weeks (compared to 8 weeks for casting) while providing topology-optimized structures that will reduce weight by 20% and increase combustion efficiency.
Case Study: U.S.-based Launcher utilized 3D-printed copper alloy combustion chambers to achieve 2.77KN thrust and minimize testing cycles by as much as 70%.


- Technology Comparison: Choosing the Optimal Solution
Metric | Traditional Casting | CNC Machining | 3D Printing |
Cycle Time | 8-12 weeks | 4-6 weeks | 2-3 weeks |
Unit Cost | $800 (high-volume) | $1,200 (mid-volume) | $1,500 (low-volume) |
Complexity | Low (simple shapes) | Medium (curved surfaces) | High (topology-optimized) |
Sustainability | High energy waste | Moderate energy use | Low waste, energy-efficient |
Decision Guide:Standardization at scale → Traditional casting (most economical). High precision and customization→ CNC machining (tightest tolerances). Low volume and complex geometries → 3D printing (freedom to design).
Future Trends & Core Value
Hybrid Manufacturing (CNC + 3D Printing): Integrating an additive roughing step with a CNC finishing step can increase throughput by 30%, as seen in DMG MORI’s industrial solutions. Smart Manufacturing: AI-assisted parameter optimization (e.g. Siemens NX modules) enables users to run simplications to lead times or trial-and-error costs and eliminate waste as throw-outs and supports educational learning from a yield standpoint when ramping up production with a new tooling solution.
Take Action Now
- Get Custom Solutions:
Contact Experts: peter@turbineblade.net
WhatsApp: +86 135 4409 5201
- Our Distinctive Advantage:
More than 20 years of combustion chamber manufacturing experience with over 50 customers around the world.
Process certifications (AS9100/ISO 9001) allowing integration of CNC and 3D printing.
Advanced facilities: 5-axis CNC, metal 3D printers, CMM inspection.