Guide Vanes, a critical component in the aerospace and industrial sectors, play a pivotal role in controlling and directing airflow or fluid flow within engines, turbines, and other mechanical systems. These components are essential for optimizing the performance and efficiency of such systems by ensuring that the flow is precisely managed and regulated. When it comes to selecting materials for Guide Vanes, especially for applications involving high-temperature and corrosive environments, Inconel 600 stands out as a premier choice due to its exceptional properties and performance.
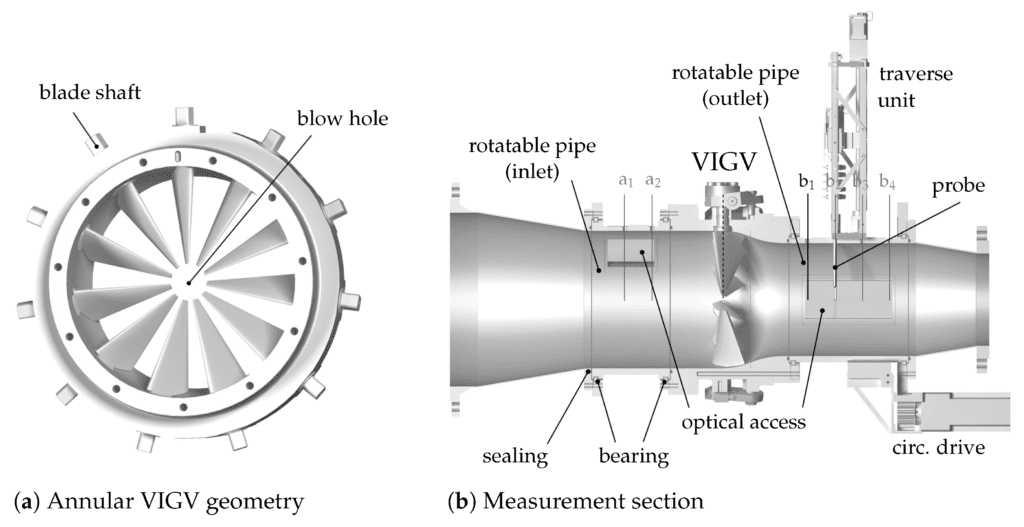
Superior Material Properties
Inconel 600, a member of the Inconel family of nickel-based superalloys, is renowned for its outstanding resistance to thermal fatigue, oxidation, and corrosion. This alloy is specifically formulated to withstand extreme conditions, making it an ideal material for Guide Vanes used in jet engines, gas turbines, and other high-performance systems. The unique composition of Inconel 600, which includes significant amounts of chromium and iron, contributes to its remarkable strength at elevated temperatures and its ability to maintain dimensional stability over time. Additionally, Inconel 600 exhibits excellent weldability and formability, allowing it to be easily fabricated into complex shapes required for Guide Vanes.
Advanced Manufacturing Techniques
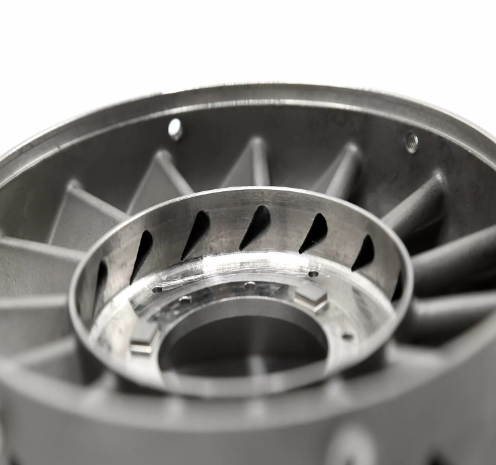
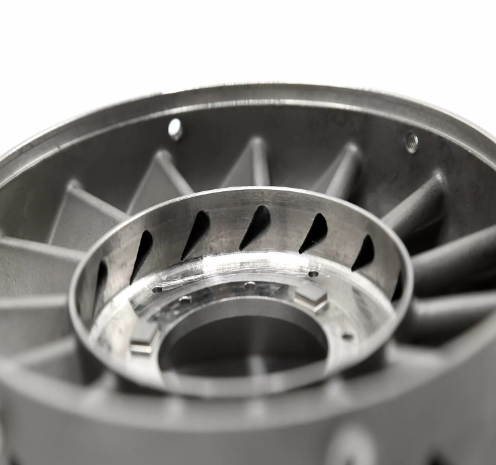
The design and manufacturing process of Guide Vanes made from Inconel 600 are critical to their performance and reliability. These components must meet the stringent standards of the aerospace and industrial sectors, taking into account the specific requirements of the application, including the operating environment, expected service life, and performance targets. Advanced manufacturing techniques, such as precision casting and additive manufacturing, are often employed to ensure that the Guide Vanes meet these high standards. Precision casting allows for the creation of intricate geometries that optimize flow dynamics, while additive manufacturing enables the production of highly complex and customized designs.
Surface Finish and Treatment
The surface finish of Guide Vanes made from Inconel 600 is a crucial factor in their performance. A smooth, polished surface can significantly reduce friction and turbulence, leading to improved aerodynamic or hydrodynamic characteristics. Various surface treatments, such as polishing, grinding, and coating, are applied to achieve the desired finish and to further enhance the corrosion resistance of the material. These treatments are carefully selected based on the specific application and the environmental conditions the Guide Vanes will encounter. For example, electroplating or thermal spray coatings can be used to provide additional protection against wear and corrosion.
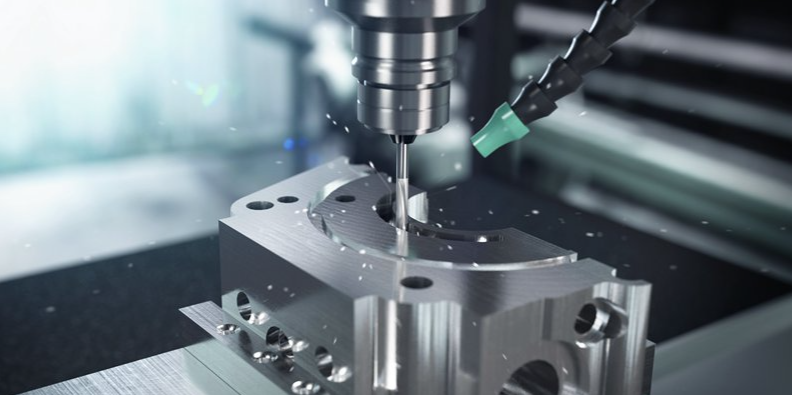
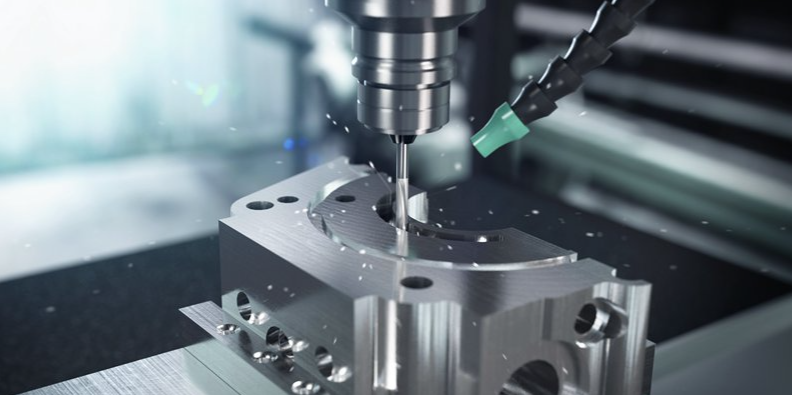
Durability and Reliability
The durability and reliability of Guide Vanes made from Inconel 600 are essential considerations, especially in high-stress environments. The longevity of these components can significantly impact the maintenance schedule and operational costs of the system. Inconel 600’s inherent strength and resistance to degradation make it a cost-effective solution in the long term, reducing the need for frequent replacements and minimizing downtime. This material’s ability to perform consistently under extreme conditions ensures that the system operates efficiently and reliably over its entire service life.
Compatibility with Other High-Performance Materials
Another significant advantage of using Inconel 600 in Guide Vanes is its compatibility with other high-performance materials commonly found in aerospace and industrial applications. This material can be effectively integrated into systems that utilize other advanced alloys, ceramics, and composites, ensuring a cohesive and optimized design. The ability to work seamlessly with a variety of materials is particularly valuable in complex systems where multiple components interact to achieve optimal performance. For instance, Inconel 600 can be paired with ceramic coatings or carbon fiber composites to create hybrid components that combine the best properties of each material.
Real-World Applications
Inconel 600 Guide Vanes have been successfully used in a wide range of applications, from commercial and military aircraft engines to industrial gas turbines and power generation systems. In jet engines, these Guide Vanes help to regulate the airflow through the compressor and turbine stages, improving fuel efficiency and reducing emissions. In gas turbines, they ensure optimal gas flow, enhancing the overall performance and reliability of the system. The versatility of Inconel 600 makes it suitable for both new designs and retrofit projects, providing a reliable solution for upgrading existing systems.
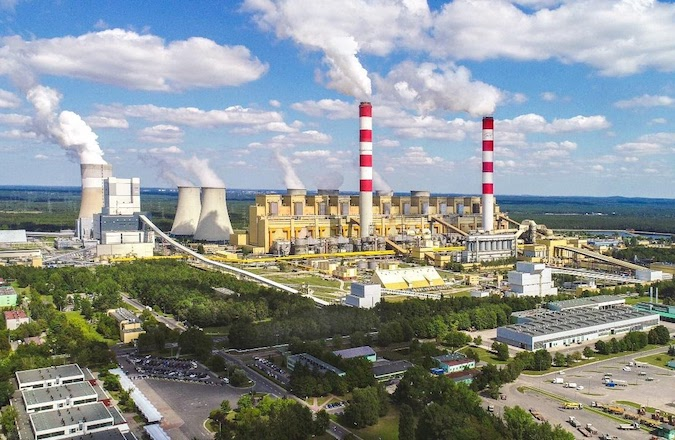
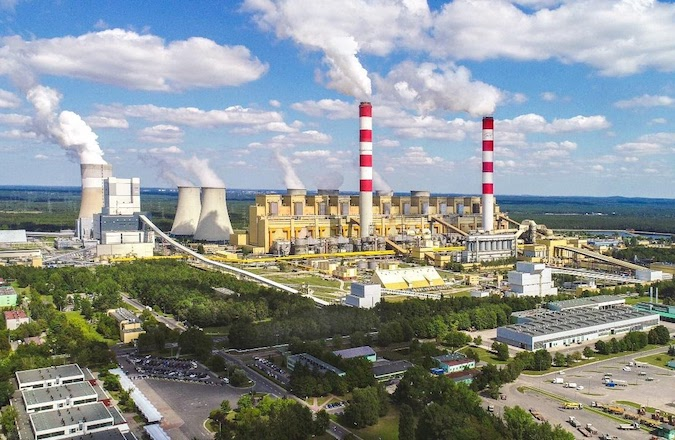
Environmental Considerations
Environmental factors are increasingly important in the design and selection of materials for aerospace and industrial applications. Inconel 600 not only meets the performance requirements but also aligns with environmental standards and regulations. Its resistance to corrosion and degradation means that it requires less maintenance and fewer replacements, reducing the environmental impact of the system. Additionally, the material’s recyclability contributes to sustainable practices in the industry.
Case Studies and Success Stories
One notable example of the successful application of Inconel 600 Guide Vanes is in the aerospace industry, where they have been used in the engines of several commercial and military aircraft. These Guide Vanes have demonstrated exceptional performance and reliability, contributing to the overall efficiency and safety of the aircraft. Another example is in the power generation sector, where Inconel 600 Guide Vanes have been installed in gas turbines, resulting in significant improvements in fuel efficiency and reduced maintenance costs.
Future Trends and Innovations
The future of Guide Vanes made from Inconel 600 looks promising, with ongoing research and development aimed at further enhancing their performance and capabilities. Advances in material science and manufacturing technologies are expected to lead to even more durable and efficient Guide Vanes. For instance, the integration of smart materials and sensors could enable real-time monitoring and optimization of flow dynamics, further improving the performance of aerospace and industrial systems.
Customization and Design Flexibility
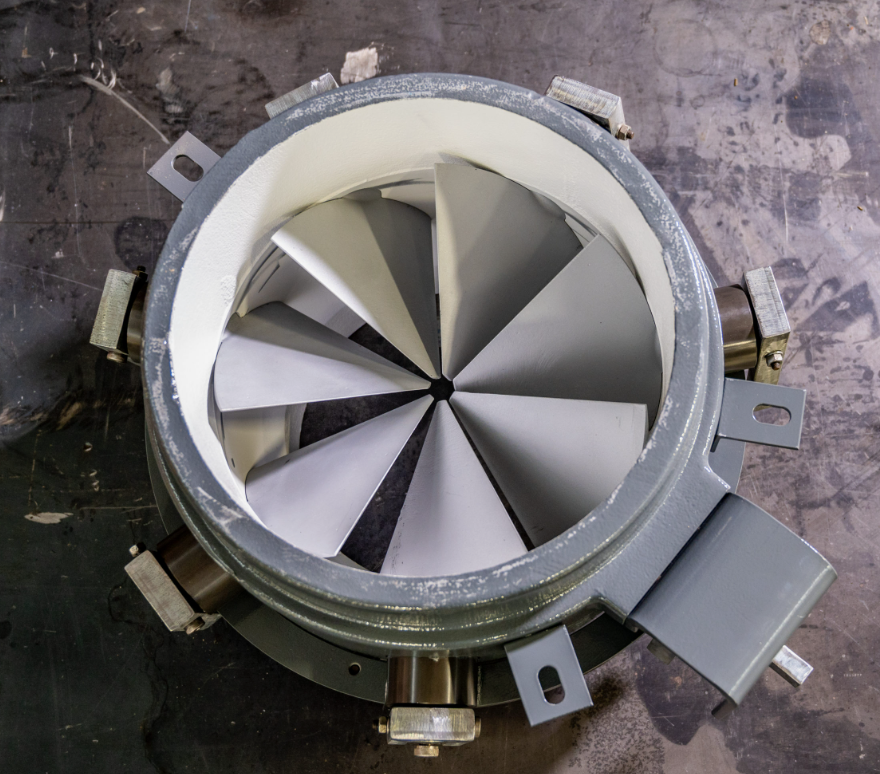
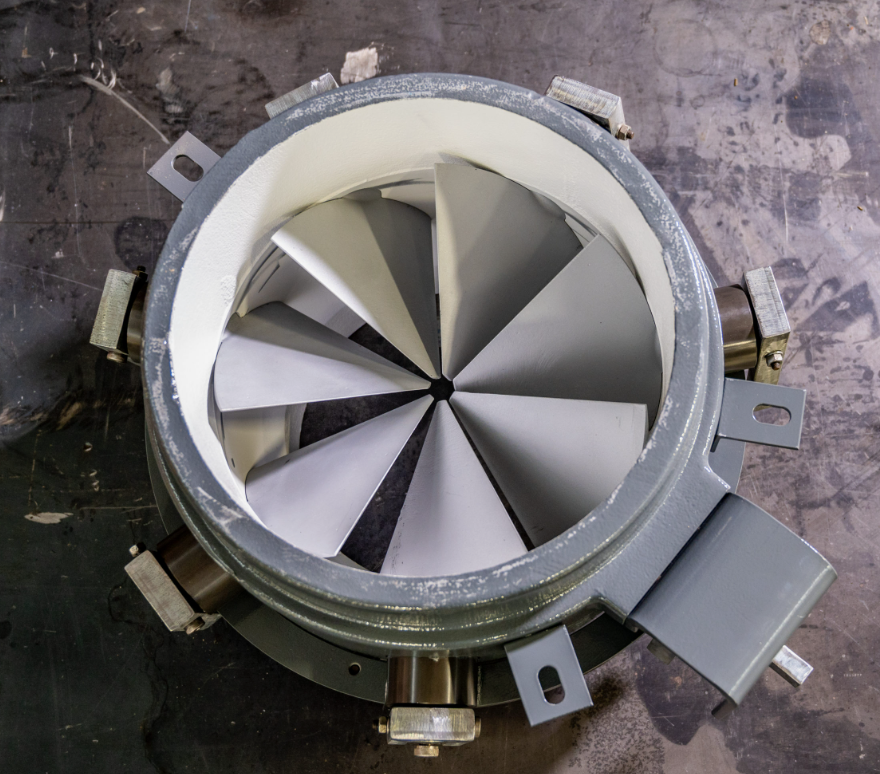
Inconel 600 Guide Vanes offer a high degree of customization and design flexibility. Engineers can tailor the design to meet specific application requirements, whether it involves optimizing flow patterns, enhancing structural integrity, or improving thermal management. This flexibility allows for the creation of bespoke components that can address unique challenges and performance needs. Advanced CAD software and simulation tools are often used to model and test different designs before final production, ensuring that the final product meets all necessary specifications and performance criteria.
Maintenance and Inspection
Regular maintenance and inspection are crucial for ensuring the continued performance and reliability of Inconel 600 Guide Vanes. Non-destructive testing (NDT) methods, such as ultrasonic testing, radiographic testing, and eddy current testing, are commonly used to detect any signs of wear, corrosion, or structural issues. These inspections help identify potential problems early, allowing for timely repairs or replacements. Proper maintenance practices, combined with the robust nature of Inconel 600, can significantly extend the service life of Guide Vanes and reduce overall operational costs.
Conclusion
In conclusion, Guide Vanes made from Inconel 600 offer a combination of superior material properties, advanced manufacturing techniques, and enhanced surface finishes that make them ideal for demanding applications. Whether used in jet engines, gas turbines, or other high-performance systems, Inconel 600 Guide Vanes provide the reliability, efficiency, and durability needed to meet the highest standards of the aerospace and industrial sectors. Their ability to perform consistently under extreme conditions and their compatibility with other high-performance materials make them a cost-effective and sustainable choice for modern engineering challenges.
Contact Us
If you are looking for high-quality Guide Vanes made from Inconel 600, our company is here to help. We specialize in the design, manufacturing, and testing of Guide Vanes for a wide range of applications. Our team of experienced engineers and technicians is dedicated to delivering products that meet your specific requirements and exceed your expectations. Whether you need custom-designed components for a new project or reliable solutions for an existing system, we are committed to providing the highest level of service and support. Contact us today to discuss your project and learn more about how we can support your needs.